7 Advantages of In-Situ Rotor Shaft Grinding for Turbines
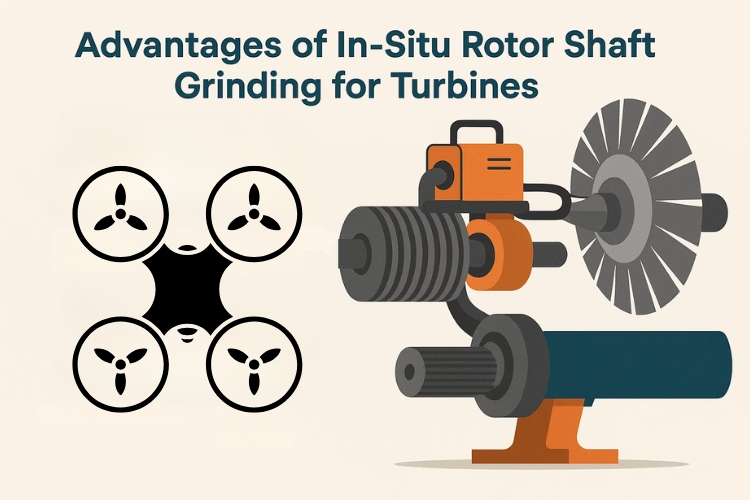
In industries where turbines play a vital role—like marine, power generation, and heavy manufacturing—any downtime due to shaft damage can lead to massive operational and financial losses. Over time, even the most robust turbines are prone to wear, misalignment, or scoring on the rotor shaft. Traditionally, such issues meant dismantling the entire turbine and transporting the rotor shaft to a workshop for repairs—a process that could take days or even weeks.
But today, thanks to advancements in portable machining technology, in-situ rotor shaft grinding offers a smarter, faster, and more cost-effective solution. Let's explore what in-situ rotor shaft grinding is and why it has become the preferred method for turbine maintenance and repair.
What is In-Situ Rotor Shaft Grinding?
In-situ rotor shaft grinding refers to the process of reconditioning or repairing the shaft directly at the site of operation, without the need to dismantle or transport the equipment. This is done using specialized portable grinding machines operated by trained technicians who can restore the shaft’s surface to OEM standards.
This process is particularly beneficial for large and heavy equipment such as gas turbines, steam turbines, marine propulsion systems, and diesel generator sets.
1. Minimizes Downtime Significantly
One of the biggest advantages of in-situ grinding is the drastic reduction in downtime. Dismantling a turbine, arranging for transportation, and reassembling it after workshop repairs can take weeks. In contrast, in-situ grinding is completed at the site in a matter of hours or days, depending on the damage.
For industries like power plants or shipping companies, where equipment uptime directly impacts productivity and revenue, every hour saved is crucial. In-situ repairs help restore functionality without extended interruption, helping businesses stay operational.
2. Eliminates the Need for Dismantling and Transportation
Imagine the complexity of removing a rotor shaft from a large marine engine or steam turbine. You’d need heavy lifting equipment, transport arrangements, and multiple technicians working around the clock. Not only is this process labor-intensive, but it also introduces risk during disassembly and transit.
With Rotor Shaft Grinding Onsite, all of that is avoided. The shaft remains mounted, and repairs are done right there—saving both effort and money. This method also reduces the chances of collateral damage that might occur during equipment handling or reinstallation.
3. Restores Original Precision and Performance
Rotor shafts are precision-engineered components. Any irregularity in roundness, taper, or surface finish can compromise the overall balance and performance of the turbine, leading to vibrations, reduced efficiency, and long-term damage.
During in-situ grinding, technicians use calibrated tools and instruments to achieve tolerances as tight as those maintained in high-end workshops. This ensures that the shaft’s surface finish and concentricity meet the exact specifications set by the OEM (Original Equipment Manufacturer).
The result? Your turbine runs as efficiently and smoothly as it did when it was first commissioned.
4. Cost-Effective Solution
Cost-saving is another huge benefit of in-situ rotor shaft grinding. Think about all the expenses involved in conventional repair: transportation of heavy parts, equipment rental, extra labor, and extended downtime.
In comparison, in-situ grinding involves fewer resources and is completed in a shorter time frame, which directly reduces both fixed and variable costs. Moreover, since there’s no need for reinstallation, the associated risks and expenses of potential rework are eliminated.
It’s a win-win for businesses looking to cut down on operational repair costs without compromising quality.
5. Enhances Safety During Repair
Safety is a top concern, especially in industries where heavy machinery and high-pressure systems are involved. Traditional repair methods require heavy lifting, rigging, and disassembly of large turbine parts—activities that inherently carry a higher safety risk.
In-situ grinding minimizes these hazards. Since the shaft remains in its original setup and alignment, technicians perform the repair without major movement or handling of components. This ensures a safer work environment for both maintenance teams and surrounding operations.
6. Suitable for Emergency Repairs
Turbine shaft failure can happen suddenly and unexpectedly, especially in older systems or in harsh working environments like marine vessels or offshore power plants. In such scenarios, you need a quick response to avoid heavy losses or potential disasters.
In-situ rotor shaft grinding services are mobile, and trained teams can reach your site on short notice. This makes them ideal for emergency breakdowns where immediate action is required to restore turbine function and prevent further damage.
Additionally, some service providers offer round-the-clock availability for urgent repair needs, making in-situ grinding an essential part of any contingency plan.
7. Versatile and Applicable to Various Engine Types
Whether you are dealing with a marine diesel engine, a hydro turbine, or a power plant gas turbine, in-situ grinding can be adapted to a wide range of engine models and sizes. The grinding machines are custom-designed to accommodate different shaft diameters, lengths, and orientations.
This flexibility makes in-situ grinding a go-to solution for industries like:
- Marine shipping (engine and propulsion shaft repairs)
- Power generation (turbines and alternator shafts)
- Cement and steel plants (rotary kiln and mill shafts)
- Oil & gas (compressors and pump shafts)
It also complements other advanced techniques like In-situ Grinding of Crankshaft, ensuring a comprehensive repair solution for critical rotating components.
Final Thoughts
Turbine shaft damage is inevitable over time due to mechanical stress, misalignment, or operational wear. But how you choose to handle that damage can make a big difference in your plant’s efficiency, safety, and repair costs.
In-situ rotor shaft grinding is not just a repair method—it’s a strategic maintenance solution. By reducing downtime, cutting costs, and maintaining OEM-level precision, this technique proves invaluable for industries that depend on uninterrupted turbine performance.
Whether you're operating a marine engine on a cargo vessel, managing a power plant, or overseeing heavy industrial machinery, consider the many benefits of onsite rotor shaft grinding before opting for conventional workshop repairs.
FAQs
Q1: How long does in-situ rotor shaft grinding take?
Answer: Depending on the shaft size and extent of damage, in-situ grinding can take anywhere from a few hours to 2–3 days.
Q2: Can all types of damage be repaired using in-situ grinding?
Answer: Minor to moderate wear, scoring, taper, and ovality issues can be repaired. For severe cracks or deep damage, further evaluation is needed.
Q3: Is in-situ rotor shaft grinding safe for marine engines?
Answer: Yes. It is widely used in marine industries as it eliminates the need for removing the shaft from cramped engine rooms, making it a safer and more practical option.
Q4: What kind of tolerance can be achieved through onsite grinding?
Answer: Tolerances as tight as 0.02 mm are achievable, which meets or exceeds OEM standards in most cases.
Q5: What are the prerequisites for in-situ grinding?
Answer: Access to the shaft, power supply, stable working conditions, and adequate space around the shaft are essential for efficient in-situ grinding.
Let your next turbine repair be faster, safer, and more economical—with in-situ rotor shaft grinding done right at your site.
Note: IndiBlogHub features both user-submitted and editorial content. We do not verify third-party contributions. Read our Disclaimer and Privacy Policyfor details.