Abrasive Paper Manufacturing Plant Project Report 2025: Manufacturing Plant Setup and Operations
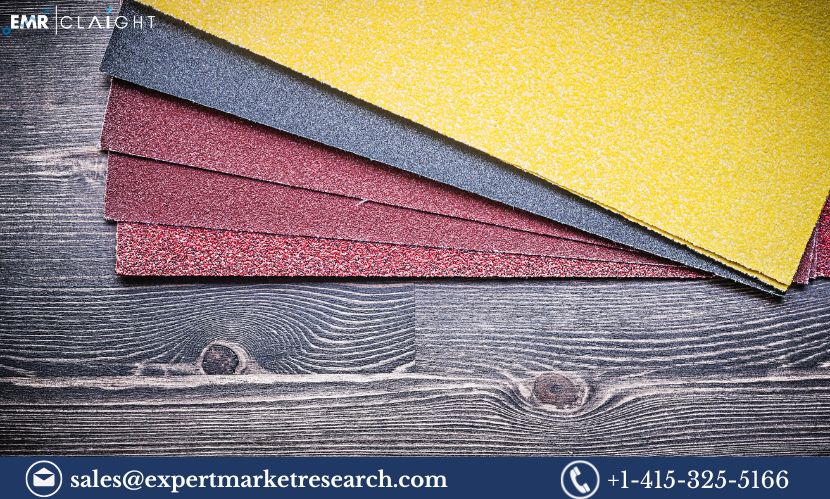
Introduction
Abrasive paper, commonly known as sandpaper, is a versatile material used for smoothing, polishing, and finishing surfaces by abrasion. It consists of a paper backing coated with abrasive particles such as aluminum oxide, silicon carbide, or garnet. These abrasives are used in a wide range of industries, including automotive, construction, woodworking, metalworking, and consumer goods manufacturing. The global demand for abrasive paper is steadily growing due to its essential role in various applications that require surface preparation and finishing. This Abrasive Paper Manufacturing Plant Project Reportย aims to provide a comprehensive overview of setting up a manufacturing plant for abrasive paper. It outlines the necessary steps involved in the production process, market analysis, equipment requirements, raw materials, regulatory compliance, and financial considerations. Whether you're an entrepreneur looking to venture into the abrasive materials market or an established business aiming to expand, this report will serve as a valuable guide to understanding the intricacies of establishing an abrasive paper manufacturing facility.
Market Overview of Abrasive Paper
Abrasive paper is widely used across industries for tasks such as sanding, polishing, and cleaning various surfaces. The most common application of abrasive paper is in the automotive and woodworking sectors. However, it is also extensively used in metalworking, construction, and electronics. The growing demand for high-quality finishes, durability, and efficiency across different industries continues to drive the market for abrasive paper.
Key Market Drivers
Construction and Renovation Industry: The construction industry requires abrasive paper for surface finishing, preparing walls, floors, and furniture, especially in the painting, plastering, and finishing stages.
Automotive Sector: The automotive industry uses abrasive paper for sanding vehicle body parts, especially during the repair and repainting processes. The rising demand for automotive repairs and refinishing further fuels the growth of the abrasive paper market.
Woodworking and Furniture Manufacturing: Woodworking businesses, including furniture manufacturing, require abrasive paper for smoothing, sanding, and finishing wood surfaces. As the demand for custom and high-quality furniture grows, so does the demand for abrasive paper.
Metalworking and Manufacturing: In metalworking, abrasive paper is used to prepare metal surfaces before painting or coating. This sector includes industries involved in machinery production, automotive parts, and electronics, among others.
Consumer Goods and Electronics: Abrasive papers are used in the production of consumer electronics and various other consumer goods for polishing and surface treatment. With increasing demand for high-quality electronic products, the need for abrasive materials also grows.
Get a Free Sample Report with Table of Contents@
https://www.expertmarketresearch.com/prefeasibility-reports/abrasive-paper-manufacturing-plant-project-report/requestsample
Types of Abrasive Paper
Aluminum Oxide Abrasive Paper: Known for its durability, this type of abrasive paper is often used in woodworking and metalworking applications.
Silicon Carbide Abrasive Paper: Known for its sharpness, this abrasive paper is used for sanding harder materials, including glass and ceramics.
Garnet Abrasive Paper: A natural abrasive that is ideal for woodworking, providing a fine finish.
Ceramic Abrasive Paper: Made from ceramic particles, this paper is suitable for heavy-duty applications and aggressive material removal.
Manufacturing Process of Abrasive Paper
The production of abrasive paper involves a series of well-coordinated processes that include the preparation of raw materials, coating the paper with abrasive particles, curing, and finishing. Below is a detailed breakdown of the manufacturing process:
1. Raw Material Procurement
The primary raw materials for abrasive paper production include:
Paper Backing: The paper used as the backing material is typically kraft paper, which provides strength and flexibility. The paper is selected based on its weight and quality, which will affect the durability and flexibility of the final product.
Abrasive Particles: Common abrasive particles include aluminum oxide, silicon carbide, and garnet. These particles are chosen based on the desired abrasiveness and the type of material the paper will be used on.
Adhesive (Bonding Agent): A resin or glue is used to bond the abrasive particles to the paper backing. The adhesive must be durable enough to withstand the wear and tear during sanding while maintaining flexibility.
Back Coating: Some abrasive papers are coated with a layer on the back to enhance the paper's resistance to tearing or curling during use.
Curing Agents: Chemical agents are used to cure the adhesive and ensure a strong bond between the abrasive particles and the paper backing.
2. Paper Preparation
The first step in the manufacturing process is the preparation of the paper backing. The paper is usually processed to the desired thickness, length, and width before it is coated with abrasives. Depending on the intended use of the abrasive paper, the paper backing may be treated to enhance its flexibility and strength.
3. Abrasive Coating
Once the paper backing is prepared, the next step is to coat it with abrasive particles. The paper is passed through a coating machine where a slurry or paste of adhesive and abrasive particles is applied evenly to the paper surface. The key steps in the coating process include:
Preparation of Coating Solution: The adhesive is mixed with abrasive particles to create a slurry that will be applied to the paper backing.
Coating the Paper: The prepared coating solution is spread uniformly over the paper using coating machines. The coating method may vary, depending on the type of abrasive paper being produced (e.g., resin coating, electrostatic coating).
4. Curing and Drying
After the paper is coated with abrasive particles, it is sent through a curing process. The paper is placed in a curing oven, where it is heated to solidify the adhesive and ensure the particles are securely bonded to the backing material. This step ensures that the abrasive paper maintains its durability during use.
5. Grading and Cutting
Once the abrasive paper is cured and dried, it is graded based on the size and uniformity of the abrasive particles. The paper is then cut into the desired sizes, typically sheets, rolls, or discs, depending on the end-use requirements.
Grading: Abrasive papers are graded according to the particle size of the abrasives. Finer grits are used for finishing surfaces, while coarser grits are used for heavy material removal.
Cutting: The paper is cut into sheets, rolls, or discs according to customer specifications or standard sizes.
6. Finishing and Inspection
At this stage, the abrasive paper undergoes a final inspection to ensure quality and consistency. The key checks include:
Visual Inspection: To ensure there are no defects such as gaps, wrinkles, or uneven coatings.
Strength Testing: To ensure that the paper backing is strong enough to withstand use.
Adhesion Testing: To verify that the abrasive particles are securely bonded to the paper.
Any paper that does not meet the quality standards is rejected or reprocessed.
7. Packaging
After passing the inspection process, the final abrasive paper product is packaged according to customer requirements. The paper may be packaged in individual sheets, rolls, or bulk packaging. Packaging is designed to protect the product from damage during storage and transportation.
Key Considerations for Setting Up an Abrasive Paper Manufacturing Plant
1. Location Selection
Choosing the right location for the manufacturing plant is crucial to minimizing operational costs. Ideally, the plant should be situated near suppliers of raw materials (abrasive particles, paper, adhesives) and transportation hubs for easy distribution. The proximity to key markets, such as automotive, construction, and furniture manufacturing industries, should also be considered.
2. Technology and Equipment
A wide range of equipment is required to manufacture abrasive paper, including:
Coating machines: For applying abrasive particles to the paper.
Curing ovens: For drying and curing the paper after it is coated with abrasives.
Cutting machines: For cutting the paper into sheets, rolls, or discs.
Grading machines: To grade the abrasive paper based on particle size.
Investing in advanced technology will improve production efficiency, consistency, and overall product quality.
3. Raw Material Sourcing
Reliable sourcing of high-quality raw materials is essential for producing abrasive paper. Establishing strong relationships with suppliers of paper, abrasive particles, and adhesives will ensure a consistent supply of materials. Negotiating bulk purchasing agreements can help reduce material costs.
4. Labor and Workforce
The plant will require a skilled workforce, including machine operators, quality control inspectors, and maintenance personnel. Proper training and a focus on worker safety are critical to maintaining high productivity and minimizing downtime.
5. Regulatory Compliance
The manufacturing of abrasive paper is subject to environmental and safety regulations. The plant must comply with local regulations regarding the use of chemicals, waste disposal, and worker safety. It may also need to obtain relevant certifications to ensure product quality.
6. Waste Management
The manufacturing process generates waste materials, including paper scraps and unused abrasive particles. Implementing efficient waste management practices will help minimize environmental impact and reduce operational costs. Recycling and reprocessing waste materials can also enhance profitability.
Financial Considerations
1. Initial Investment
The initial capital investment for setting up an abrasive paper manufacturing plant includes the cost of land, building, machinery, and raw materials. Additionally, costs for obtaining licenses and regulatory approvals, as well as initial working capital, should be factored in.
2. Operational Costs
Ongoing operational costs include raw material procurement, labor wages, energy consumption, machine maintenance, and packaging. Efficient management of these costs is essential for maintaining profitability.
3. Revenue Generation
Revenue is generated by selling the abrasive paper to manufacturers in industries such as automotive, construction, woodworking, and metalworking. Establishing a strong customer base and effective distribution channels is key to generating consistent revenue.
4. Return on Investment (ROI)
The ROI for an abrasive paper manufacturing plant will depend on production efficiency, raw material costs, labor costs, and market demand. With proper management and high product quality, the plant can generate a positive ROI within a few years.
Media Contact
Company Name: Claight Corporation
Contact Person: Peter Fernandas, Corporate Sales Specialist โ U.S.A.
Email: [email protected]
Toll Free Number: +1โ415โ325โ5166 | +44โ702โ402โ5790
Address: 30 North Gould Street, Sheridan, WY 82801, USA
Note: IndiBlogHub features both user-submitted and editorial content. We do not verify third-party contributions. Read our Disclaimer and Privacy Policyfor details.