All Gear Types: A Comprehensive Overview of Gear Mechanisms
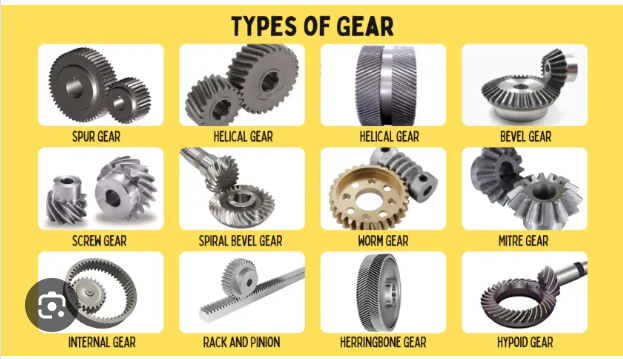
Gears are fundamental components in various mechanical systems, serving as essential elements for transmitting power and motion. They are used in everything from small household appliances to large industrial machines, making them crucial for efficiency and functionality. This article provides a detailed exploration of all gear types their designs, applications, advantages, and limitations. By understanding these gears, engineers, designers, and technicians can make informed decisions when selecting the right components for their projects.
Understanding Gears: The Mechanics Behind the Motion
At its core, a gear is a rotating machine part with teeth that mesh with another gear to transmit torque and motion. The interaction between the teeth of the gears allows them to transfer energy, resulting in the desired movement of the connected components. Gears are classified based on various factors, including tooth design, orientation, and the direction of power transmission.
Key Functions of Gears
1. Power Transmission: Gears are primarily designed to transfer mechanical energy from one part of a machine to another.
2. Speed Adjustment: Different gear types can adjust the rotational speed of the output shaft.
3. Torque Modification: Gears can increase or decrease the torque delivered to a load, allowing for precise control.
4. Directional Change: Gears enable the change of motion direction, essential for many mechanical applications.
Understanding the various types of gears is crucial for selecting the appropriate gear for specific applications.
Major Types of Gears
1. Spur Gears
• Description: Spur gears are the most basic type of gear, characterized by their straight, parallel teeth aligned with the axis of rotation. They are usually mounted on parallel shafts.
• Applications: Commonly found in clocks, conveyor belts, and various machinery where straightforward speed and torque requirements are needed.
• Advantages:
o Simple design and easy to manufacture.
o High efficiency due to minimal friction.
• Disadvantages:
o Can generate noise and vibration at high speeds.
o Limited to applications where shaft alignment is perfect.
2. Helical Gears
• Description: Helical gears have teeth cut at an angle to the axis of rotation. This angled design allows for gradual engagement, which enhances performance.
• Applications: Commonly used in automotive transmissions and industrial machinery where higher speeds and quieter operation are desired.
• Advantages:
o Smoother operation compared to spur gears due to gradual tooth engagement.
o Greater load capacity due to the increased surface area of the teeth.
• Disadvantages:
o More complex to manufacture and install than spur gears.
o Can be more expensive due to increased material and machining requirements.
3. Bevel Gears
• Description: Bevel gears are designed to transmit power between shafts that are typically oriented at 90 degrees to each other. They feature conical shapes with teeth that can be straight or curved.
• Applications: Widely used in automotive differentials and machinery where power needs to be transmitted at an angle.
• Advantages:
o Efficiently transmits power at angles.
o Compact design allows for space savings in machinery.
• Disadvantages:
o Requires precise alignment for effective operation.
o More complicated design compared to spur gears.
4. Worm Gears
• Description: Worm gears consist of a worm (a screw-like gear) that meshes with a worm wheel. This arrangement provides high torque and speed reduction.
• Applications: Frequently used in lifts, conveyor systems, and winches where significant reduction ratios are necessary.
• Advantages:
o Compact design with high torque output.
o Typically non-reversible, which prevents back-driving.
• Disadvantages:
o Lower efficiency due to the sliding contact between the worm and wheel.
o Generates heat due to friction, requiring good lubrication.
5. Rack and Pinion Gears
• Description: This system consists of a pinion gear that engages with a linear rack, effectively converting rotational motion into linear motion.
• Applications: Commonly used in steering mechanisms of vehicles and various automation applications.
• Advantages:
o Provides precise control of linear motion.
o Simple and effective design that is easy to implement.
• Disadvantages:
o Limited travel distance compared to other gear systems.
Industrial Applications of Gears
Gears find applications across a wide range of industries, each requiring specific gear types tailored to their operational needs. Here are some examples of gear applications in various sectors:
Automotive Industry
• Transmission Systems: Various gear types such as helical, spur, and bevel gears are critical in automotive transmissions, managing speed and torque for optimal vehicle performance.
• Differentials: Bevel and hypoid gears play a vital role in vehicle differentials, enabling power distribution during turns and maintaining vehicle stability.
Manufacturing and Industrial Machinery
• Manufacturing Equipment: Gears such as planetary and worm gears are commonly used in manufacturing applications for effective power transfer and control.
• Conveyor Systems: Rack and pinion gears are often employed in conveyor systems to provide linear motion and control.
Robotics
• Precision Control: Gears like cycloidal and planetary are utilized in robotics to ensure accurate movements and high torque outputs, essential for robotic arms and automated systems.
• Adaptability: Flexible gears are increasingly integrated into robotic systems to accommodate misalignment and provide adaptability in dynamic environments.
Aerospace and Defense
• Engine Systems: Specialized gears such as timing and cam gears are critical in aircraft engines, ensuring synchronization and efficiency in high-performance settings.
• Control Mechanisms: Gears are used in flight control systems, providing precise motion control necessary for aircraft stability and maneuverability.
Conclusion
Gears are indispensable components in mechanical systems, facilitating the transfer of motion and power across various applications. Understanding all gear types, their features, and their applications allows engineers and designers to choose the most suitable gear for specific tasks. As technology continues to evolve, the development of new gear types and configurations will enhance the efficiency and functionality of machinery, making gears an ever-evolving field in engineering and design. By mastering the knowledge of gears, professionals can ensure optimal performance and reliability in their mechanical systems.
Note: IndiBlogHub features both user-submitted and editorial content. We do not verify third-party contributions. Read our Disclaimer and Privacy Policyfor details.