Anilox Coating Attachment: Revolutionizing Coating Applications in Printing Industry
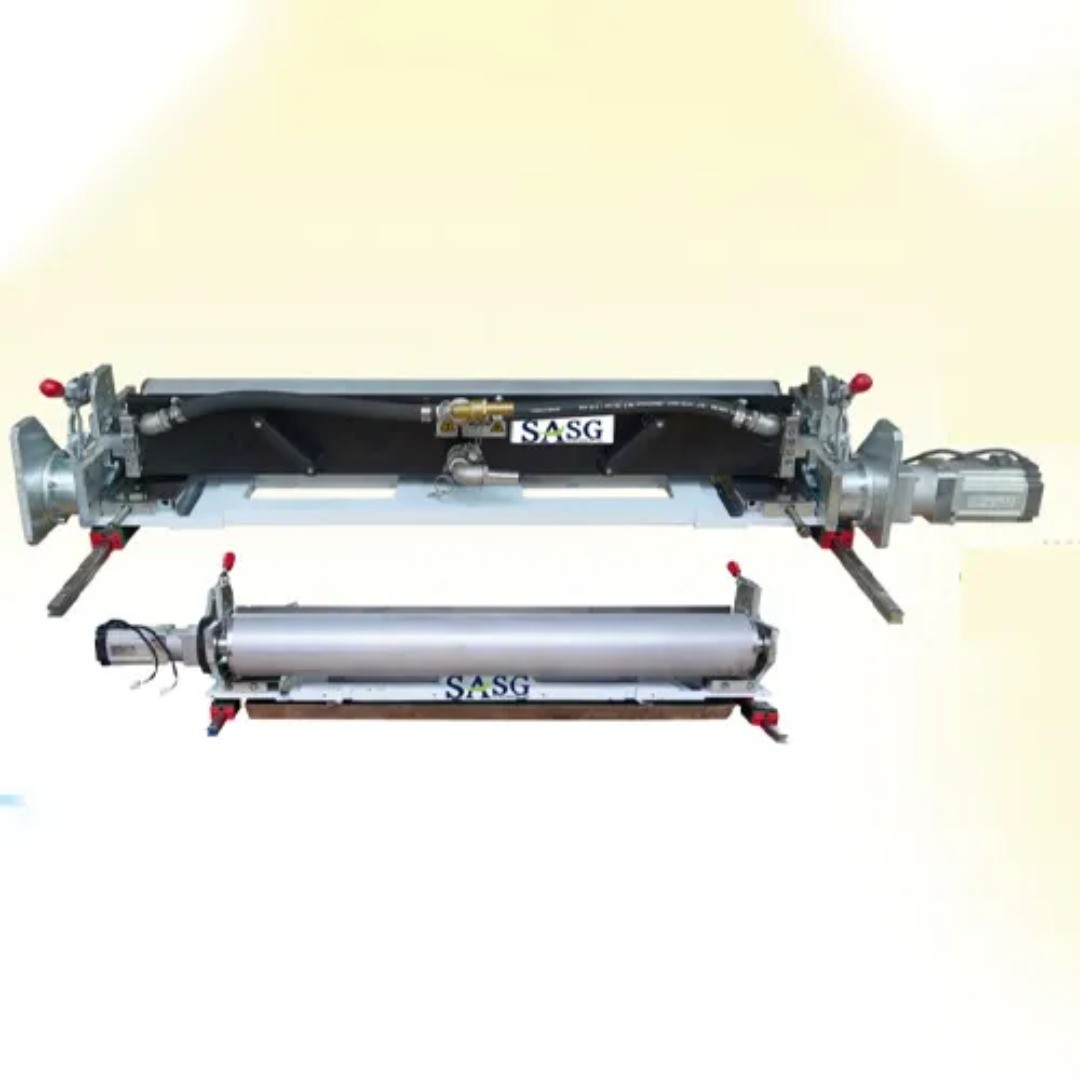
In the ever-evolving world of printing technology, the Anilox Coating Attachment has emerged as a crucial innovation. Designed to enhance the efficiency and quality of coating applications in the printing industry, this specialized device is helping businesses achieve high-performance results with precision and consistency. In this article, we will explore what an Anilox Coating Attachment is, how it works, its benefits, and its role in the modern printing process.
What is an Anilox Coating Attachment?
An Anilox Coating Attachment is a key component used in flexographic printing presses, primarily for the application of coatings to substrates such as paper, cardboard, plastic films, and more. The device features a rotating cylinder with a surface covered in microscopic cells, which are filled with coating material and transferred to the printing surface. These cells ensure that the correct amount of coating is applied, preventing wastage while providing an even and consistent coating layer.
The Anilox system is commonly used in combination with various types of coatings, including UV (ultraviolet), water-based, and solvent-based coatings. Its versatility makes it a staple in industries ranging from packaging to labels, creating a wide range of printed materials with enhanced durability, gloss, and protection.
How Does It Work?
The Anilox Coating Attachment is typically installed on a flexographic printing press, and its operation relies on precision engineering to ensure the coating is applied evenly across the surface. Here’s a breakdown of how it works:
- Rotating Anilox Roller: The core of the system is a ceramic or steel roller, which features a laser-engraved or mechanically engraved surface covered in tiny cells. These cells are designed to hold the coating material and release it onto the substrate.
- Coating Supply: The coating material is supplied to the Anilox roller, where it fills the microscopic cells. The roller rotates at a constant speed and transfers a controlled amount of the coating material to a doctor blade or chamber that regulates the amount of material applied.
- Transfer to Substrate: As the roller continues to rotate, it contacts the printing substrate, which is moving through the press. The coating material from the cells is then transferred onto the substrate, ensuring an even coating thickness across the entire surface.
- Drying and Curing: Depending on the type of coating, the coated material undergoes a drying or curing process. For UV coatings, for example, ultraviolet light is used to cure the coating almost instantly, enhancing durability and gloss.
Benefits of Anilox Coating Attachment
- Precision and Consistency: One of the primary benefits of an Anilox Coating Attachment is its ability to apply coatings with high precision. The microscopic cells in the Anilox roller ensure a consistent amount of material is transferred every time, eliminating the risk of over or under-application. This results in a smoother, more uniform finish.
- Reduced Waste: Because the Anilox system precisely controls the coating transfer, waste is minimized. The coating is only applied where needed, which reduces the amount of material used and contributes to overall cost savings.
- Increased Efficiency: The ability to apply coatings in-line with the printing process, without the need for separate coating stations or manual interventions, improves overall efficiency. This integration speeds up production, reduces setup times, and ensures a quicker turnaround on printed products.
- High-Quality Finishes: Anilox coatings can achieve a variety of finishes, from matte to high-gloss, depending on the desired outcome. This versatility allows businesses to cater to different customer needs, offering enhanced aesthetics and durability.
- Customization and Flexibility: Different industries and applications require various coating specifications. The Anilox Coating Attachment is highly customizable, allowing for easy changes in coating types, patterns, and even coating volumes. This flexibility makes it suitable for a wide range of products.
Conclusion
The Anilox Coating Attachment has revolutionized the way coatings are applied in the printing industry. By offering unparalleled precision, consistency, and efficiency, it has become an indispensable tool for businesses seeking to improve their coating processes. Whether enhancing the quality of printed materials or reducing costs, the Anilox Coating Attachment continues to shape the future of printing technology, ensuring that companies can meet the ever-growing demands of the market while delivering superior results.
Note: IndiBlogHub features both user-submitted and editorial content. We do not verify third-party contributions. Read our Disclaimer and Privacy Policyfor details.