Best Paper and Packaging Testing Instruments for Industries
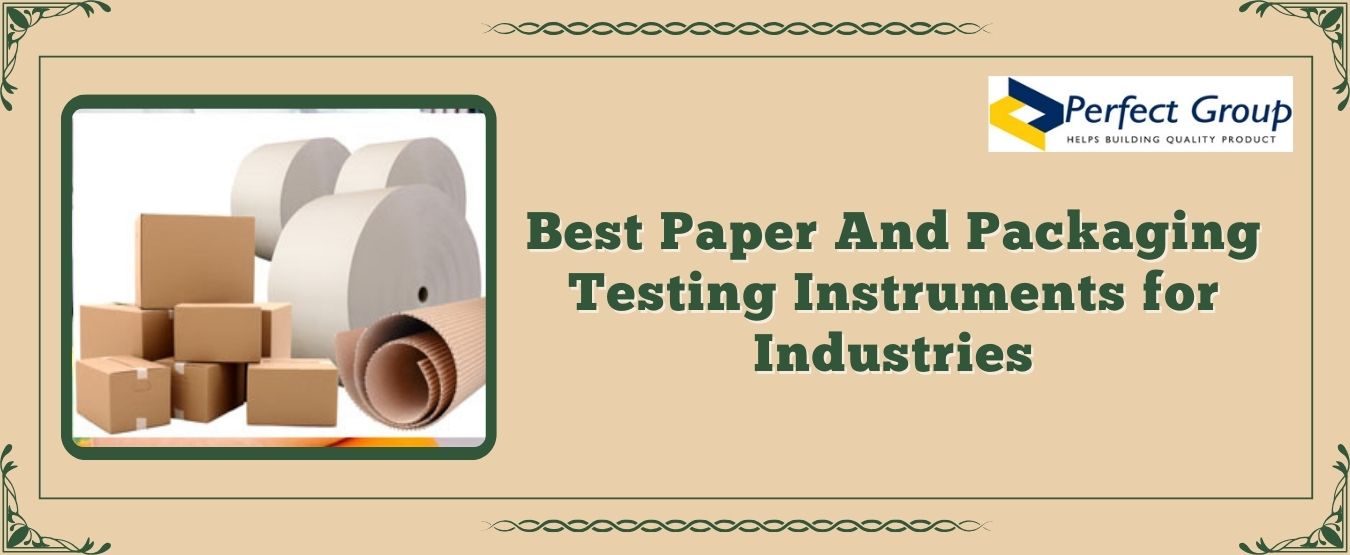
Introduction
For industries to verify the quality, strength and durability of materials used in the manufacturing of paper and packaging testing instruments are important. These devices help businesses to make sure their products fulfill industry requirements and function properly in various situations. These equipment cover a range of quality control measures, from testing seal quality to checking compression strength. They are widely used to increase reliability and decrease product failures in the paper, printing and packaging industries. These instruments, which use modern technology to provide accurate outcomes, are an excellent choice for companies looking to maintain premium paper and packaging products in highly competitive markets.
Importance of Paper and Packaging Testing Instruments
Paper and packaging testing instruments are important for guaranteeing the durability and quality of packaging materials. Manufacturers can check compression, bursting strength, seal reliability and other important factors with the help of these devices. Perfect testing reduces losses and increases customer satisfaction by avoiding damage during storage and transport. These equipment are needed by the food and transport industries in order to maintain packaging standards. Through the use of these equipments these industries can guarantee:
Follow international packaging standards
Improved product safety and durability
Reduce material wastage
Increase brand reputation
Essential Paper and Packaging Testing Instruments
1. Bursting Strength Tester
Paper, cardboard and packaging materials' ability to withstand breaking under pressure is measured by the Bursting Strength Tester. It is a required instrument to measure the durability of packaging used to move large or breakable items. This paper and packaging testing instruments helps companies to make sure that the materials used for packaging can withstand external forces without cracking.
2. Box Compression Tester
The capacity of corrugated boxes and cartons to withstand stacking pressure is measured by a box compression tester. For businesses that ship and maintain products in large quantities this device is important. It helps in figuring out how much weight can be placed and makes sure that the packaging can withstand pressure when it's transported.
3. Cobb Sizing Tester
The Cobb Sizing Tester analyzes how well paper and packaging materials use water. Businesses handling liquid or moisture products must perform this test to make sure the packaging does not retain too much moisture which can affect the durability and safety of the product.
4. Drop Tester
By following free-fall conditions, a drop tester analyzes the impact resistance of paper and packaging testing instruments. It is important for delicate or expensive items since it gauges how well a package can protect its contents from harm from unintentional drops.
5. Digital Tensile Testing
The greatest force that paper and packaging testing instruments can withstand before breaking is measured by the Digital Tensile Testing. To make sure that packaging materials are strong to withstand tearing or breaking under pressure this test is important.
6. Edge Crush Tester (ECT)
This material cardboard's cross compressive strength is measured by the Edge Crush Tester. This test is important to checking how well boxes stack and for making sure that the materials used for packaging can withstand vertical pressure while being stored and transported.
7. Peel Strength Tester
The Peel Strength Tester measures how well laminates, labels and seals follow one another. By keeping packaging closures in place, it protects against damage, tampering and leaks.
8. Puncture Resistance Tester
The ability of packaging materials to withstand damage from sharp objects is measured by the Puncture Resistance Tester. For businesses that handle pointed or sharp objects and need reliable packaging solutions, this paper and packaging testing instruments are important.
9. Secure Seal Tester
The quality of the seals in flexible packaging is checked by a Secure Seal Tester. It helps companies to measure how well packaging materials stop leaks which is particularly important for packaging used in food and medicinal products.
10. Gas Volume Tester
The amount of gas contained in sealed packaging is measured using a gas volume tester. In order to guarantee proper packaging conditions and avoid spoiling this test is particularly important in the food and beverage industry.
11. Vacuum Leak Tester
The Vacuum Leak Tester finds leaks in sealed containers and bottles to measure how airtight the packaging is. This guarantees the quality of the product and protects against damage, particularly in costly products like food and medications.
12. Top Load Tester
A bottle or container's top load limit before cracking is determined by a top load tester. In order to guarantee that plastic and glass bottles maintain their structure and form under pressure, this is important to industries that use them.
13. Coefficient of Friction Tester
The sliding resistance of materials and packaging films is measured by the Coefficient of Friction Tester. It helps businesses to determine how simple it is to handle and ship paper and packaging testing instruments.
14. Scuff Resistance Tester
The Scuff Resistance Tester analyzes the impact and resistance of printed or coated packaging materials. This provides packaging and branding prints remain clear and unharmed during handling and transport.
Factors to Consider When Choosing Testing Instruments
A variety of factors must be properly when choosing the best paper and packaging testing instruments including:
Material Type: Check the test equipment is suitable for the type of packaging material.
Testing Standards: Provide the device follows industry standards such as ASTM or ISO.
Ease of Use: Quality and productivity can be increased by devices with digital controls and simple automated features.
Durability and Maintenance: Select instruments that are made from high quality products and require low maintenance.
Testing Requirements: Based on the important test parameters that are relevant to your field, choose the right instruments.
Benefits of Using Paper and Packaging Testing Instruments
There are many advantages to using advanced paper and packaging testing instruments such as:
Enhanced Product Protection: Makes sure that the materials used for packaging offer the best safety against external forces.
Regulatory Compliance: Helps companies in following international packaging standards and laws.
Cost Savings: Reduce product damage and reduces down on material waste, which lowers costs.
Improved Customer Satisfaction: Better packaging improves customer trust and brand reputation.
Better Quality Control: Offers manufacturers to keep the quality of their packaging a fixed value.
Conclusion
Paper and packaging testing instruments make sure that industrial materials fulfill high quality requirements. These devices help to analyze the durability and strength of packaging and cardboard. Industries can increase productivity, reduce waste and avoid product damage with accurate testing. Better packaging solutions are supported by these tools, which range from compression and burst tests to seal quality checks. Packaging that is more strong, secure and environmentally friendly is the result of investing in trustworthy testing techniques. These devices stay important in maintaining product quality and customer satisfaction even as industries change. For durability selecting the right testing equipment is important.
Note: IndiBlogHub features both user-submitted and editorial content. We do not verify third-party contributions. Read our Disclaimer and Privacy Policyfor details.