Best Practices for ISO 9001 Implementation
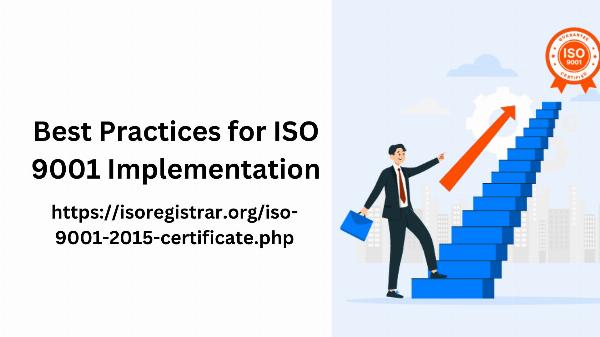
ISO 9001 certification is a globally recognized standard for quality management systems (QMS) that can help organizations improve their processes, enhance customer satisfaction, and foster a culture of continuous improvement. Implementing ISO 9001 can be a transformative process, but it requires careful planning and execution. Here are some best practices to ensure a successful ISO 9001 implementation.
1. Top Management Commitment
The success of ISO 9001 implementation starts with a strong commitment from top management. Leaders must not only endorse the process but also actively participate in it. Their involvement demonstrates the importance of quality management to the entire organization.
Set Clear Objectives: Management should define clear quality objectives aligned with the organization’s strategic goals. This creates a roadmap for implementation and sets expectations for all employees.
Allocate Resources: Ensure that adequate resources—financial, human, and technological—are allocated to support the QMS implementation.
2. Engage Employees at All Levels
Employee engagement is crucial for the successful implementation of ISO 9001. All staff members should understand the importance of the QMS and their role within it.
Training and Education: Provide training programs that cover ISO 9001 principles, QMS processes, and individual responsibilities. Empowering employees with knowledge increases their commitment to quality.
Foster a Quality Culture: Encourage open communication about quality issues and ideas for improvement. Create an environment where employees feel comfortable sharing their insights and feedback.
3. Conduct a Gap Analysis
Before implementation, conduct a thorough gap analysis to assess current processes against ISO 9001 requirements. This analysis helps identify areas for improvement and informs the development of a tailored implementation plan.
Document Existing Processes: Map out existing processes to understand workflows and pinpoint inefficiencies. This baseline will guide improvements and ensure compliance with ISO 9001.
Identify Strengths and Weaknesses: Use the gap analysis to identify strengths that can be leveraged and weaknesses that need addressing.
4. Develop a Quality Management System
A well-structured QMS is essential for ISO 9001 compliance. This system should be documented, accessible, and user-friendly.
Create a Quality Manual: Develop a quality manual that outlines the scope of the QMS, quality policies, and objectives. This document serves as a reference for employees.
Standard Operating Procedures (SOPs): Develop SOPs for key processes, ensuring that everyone understands their roles and responsibilities. SOPs help standardize practices and reduce variability.
5. Set Measurable Objectives and KPIs
Establishing measurable quality objectives and key performance indicators (KPIs) is essential for monitoring progress and driving improvement.
Align Objectives with Business Goals: Ensure that quality objectives support broader organizational goals, creating synergy between quality management and overall business strategy.
Regularly Review KPIs: Use data and metrics to evaluate performance against objectives. Regularly review these KPIs to identify trends, successes, and areas needing improvement.
6. Conduct Internal Audits
Internal audits are vital for assessing the effectiveness of the QMS and ensuring compliance with ISO 9001.
Plan and Schedule Audits: Develop a comprehensive audit plan that outlines the frequency and scope of audits. Ensure that audits are conducted consistently and thoroughly.
Use Audits for Continuous Improvement: Treat audits as opportunities for learning and improvement rather than merely compliance checks. Encourage auditors to provide constructive feedback and recommendations.
7. Implement a Document Control System
Effective document control is crucial for maintaining the integrity of the QMS. A well-structured document control system ensures that all documents are current and easily accessible.
Establish a Document Control Procedure: Define how documents are created, reviewed, approved, and distributed. Ensure that everyone understands their roles in the document control process.
Use Technology to Streamline Control: Consider using document management software to organize and track documents, making it easier to maintain compliance.
8. Focus on Continuous Improvement
Continuous improvement is a core principle of ISO 9001. Organizations should adopt a proactive approach to identifying and implementing improvements.
Use PDCA Cycle: Implement the Plan-Do-Check-Act (PDCA) cycle to facilitate continuous improvement. This iterative process allows organizations to test changes, measure outcomes, and make necessary adjustments.
Encourage Employee Involvement: Foster a culture where employees are empowered to suggest improvements. Regularly solicit feedback and ideas from all levels of the organization.
9. Management Review Meetings
Regular management review meetings are essential for assessing the performance of the QMS and making strategic decisions.
Schedule Regular Reviews: Hold management review meetings at predetermined intervals to evaluate the effectiveness of the QMS, discuss performance against objectives, and identify areas for improvement.
Document Outcomes: Record decisions made during these meetings and follow up on action items to ensure accountability and progress.
10. Effective Communication
Clear and effective communication is key to successful ISO 9001 implementation.
Communicate Policies and Objectives: Ensure that all employees are aware of the quality policies, objectives, and their roles in achieving them. Use various communication channels to reach different audiences.
Foster Open Dialogue: Create channels for employees to discuss quality-related issues, share ideas, and provide feedback. Encourage a culture of transparency and collaboration.
11. Engage External Stakeholders
Involving external stakeholders, such as suppliers and customers, can enhance the effectiveness of the QMS.
Set Expectations for Suppliers: Communicate quality expectations to suppliers and assess their performance regularly. Strong supplier relationships can improve overall product quality.
Gather Customer Feedback: Use customer feedback to inform quality improvements and ensure that the QMS aligns with customer expectations.
12. Leverage Technology
Utilizing technology can streamline ISO 9001 implementation and enhance the effectiveness of the QMS.
Use Quality Management Software: Consider adopting software solutions that can automate processes, track performance metrics, and simplify document control.
Data Analytics: Leverage data analytics tools to analyze performance data, identify trends, and inform decision-making.
Note: Apply for iso 14001 certification through the iso portal
Conclusion
Implementing ISO 9001 is a strategic endeavor that can lead to significant improvements in quality management, operational efficiency, and customer satisfaction. By following these best practices, organizations can create a robust QMS that not only meets ISO 9001 requirements but also supports long-term business objectives.
The journey toward ISO 9001 certification requires commitment, collaboration, and a focus on continuous improvement. As organizations embrace this journey, they position themselves for greater success and resilience in an ever-evolving marketplace. By fostering a culture of quality and empowering employees at all levels, businesses can unlock the full potential of their quality management system and drive sustained growth.
Note: IndiBlogHub features both user-submitted and editorial content. We do not verify third-party contributions. Read our Disclaimer and Privacy Policyfor details.