Bottle Filling Machine: Comprehensive Guide to Boost Productivity and Precision
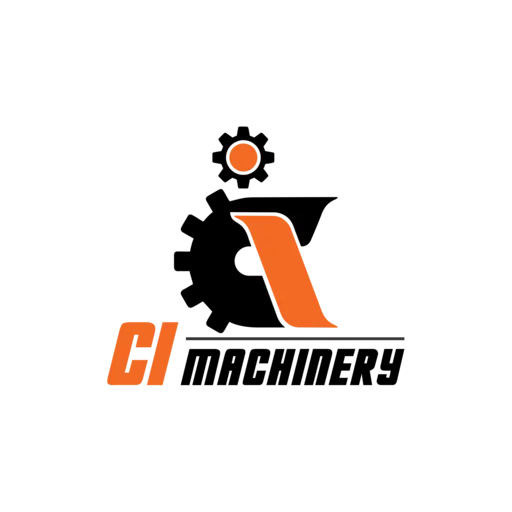
In the rapidly evolving world of manufacturing and packaging, a bottle filling machine is not just a convenience—it's a necessity. Whether you're in the beverage, cosmetics, chemical, or pharmaceutical industry, having the right filling solution can transform your operations, reduce waste, and dramatically improve your output. This article explores everything you need to know about bottle filling machines—from types and applications to advanced features and buying advice.
What is a Bottle Filling Machine?
A bottle filling machine is specialized equipment designed to fill bottles of various sizes and shapes with liquids, semi-liquids, or even powders. These machines streamline the bottling process, ensuring uniformity, speed, and accuracy across the production line. They can be manual, semi-automatic, or fully automatic depending on production needs and budgets.
Types of Bottle Filling Machines
1. Gravity Bottle Filling Machines
Ideal for low-viscosity, free-flowing liquids such as water, juices, and spirits, these machines allow liquid to flow into bottles using gravitational force. Cost-effective and low-maintenance, they're perfect for startups and small batch producers.
2. Overflow Bottle Filling Machines
These machines ensure precise fill levels, making them ideal for transparent containers where aesthetics matter. Overflow fillers are commonly used in cosmetic, personal care, and beverage industries.
3. Piston Bottle Filling Machines
Designed for high-viscosity or chunky liquids like sauces, honey, creams, and gels, these machines use a piston to draw and dispense the product. They offer unmatched volumetric accuracy.
4. Pressure Bottle Filling Machines
These are used when product flow needs assistance, especially with thick or dense liquids. Pressure fillers are found in industrial chemical and oil production lines.
5. Vacuum Bottle Filling Machines
Best suited for small volume and precision applications, especially in the perfume or essential oil sectors, vacuum fillers prevent product spillage and ensure exact filling.
Applications of Bottle Filling Machines
Food and Beverage Industry
From carbonated drinks to ketchup and cooking oils, bottle filling machines ensure hygiene, safety, and regulatory compliance in high-speed food processing environments.
Pharmaceuticals and Healthcare
Accuracy and contamination prevention are crucial. Bottle filling machines here come with HEPA filters, sterile filling zones, and anti-bacterial contact parts.
Cosmetics and Toiletries
For products like lotion, shampoo, face creams, and perfumes, filling machines must maintain product integrity. Features such as foam control and gentle handling are vital.
Chemicals and Lubricants
These machines handle flammable, corrosive, and heavy-duty fluids. With explosion-proof enclosures and corrosion-resistant parts, they're built for extreme conditions.
Key Features of Modern Bottle Filling Machines
1. Multi-Container Compatibility
Modern machines can adjust for various bottle sizes, shapes, and materials, from glass to PET and HDPE plastic.
2. Nozzle Customization
Options include anti-drip, shut-off, or bottom-up nozzles for foamy or corrosive products. Multi-head systems speed up production significantly.
3. Speed and Throughput
Machines can handle anything from 10 bottles per minute (for small setups) to 500+ bottles per minute in industrial operations.
4. Integrated Capping and Labeling
Some systems offer integrated solutions for filling, capping, sealing, and labeling—eliminating the need for multiple machines and ensuring seamless automation.
5. Programmable Logic Control (PLC)
Machines come with touchscreen HMI panels, allowing operators to store multiple recipes, monitor performance, and automate diagnostics.
Advantages of Using a Bottle Filling Machine
Enhanced Productivity: Automates repetitive tasks and fills multiple bottles simultaneously.
Reduced Wastage: Precision filling means minimal product loss.
Hygiene and Safety: Closed systems reduce contamination risks.
Scalability: Easily upgradeable to accommodate future business growth.
Regulatory Compliance: Helps meet FDA, GMP, or ISO standards with traceability and documentation features.
Selecting the Right Bottle Filling Machine
Step 1: Know Your Product
The viscosity, temperature, and chemical composition of your product determine the appropriate filling mechanism.
Step 2: Identify Bottle Type
Consider dimensions, cap styles, and materials. Machines should be adaptable to your container specs.
Step 3: Determine Output Requirements
What’s your daily or hourly bottle output? Choose between manual, semi-automatic, or fully automatic systems.
Step 4: Budgeting
Balance your initial investment against long-term benefits like speed, accuracy, and maintenance costs.
Maintenance Tips for Longevity and Efficiency
Daily Cleaning: Avoid product build-up and contamination.
Monthly Calibration: Maintain accuracy for compliance and quality.
Lubricate Moving Parts: Prevent mechanical wear and tear.
Replace Worn Components: Keep spare parts like gaskets, seals, and nozzles handy.
Train Operators: A knowledgeable team can identify issues early and avoid production delays.
Top Indian Manufacturers and Exporters
Pack Tech Solutions – Affordable and reliable packaging systems
Multipack Machinery – Export-grade filling solutions
Siddhivinayak Automation – Customizable bottle filling lines
N.K. Industries – GMP and CE certified filling machinery
Choose manufacturers who offer machine installation, operator training, and 24x7 technical support.
Future of Bottle Filling Technology
1. IoT Integration
Machines now feature real-time remote monitoring, allowing plant managers to track productivity from anywhere.
2. AI for Predictive Maintenance
Artificial intelligence is used to forecast mechanical failures before they occur—minimizing downtime.
3. Eco-Friendly Design
Sustainability is shaping the future. Energy-efficient motors, low-waste dispensing, and recyclable packaging compatibility are becoming standard.
The Importance of Precision in Bottle Filling
In sectors where product consistency is non-negotiable, even a milliliter error can result in customer dissatisfaction, revenue loss, or regulatory non-compliance. Modern bottle filling machines incorporate advanced technology like servo-driven filling, vision systems, and sensor-controlled dosing to eliminate such inconsistencies. These machines reduce human error, minimize spillage, and offer unmatched fill accuracy—often within ±0.5%.
Bottle Filling Machines by Industry Type
1. Beverage Industry
In beverage manufacturing, speed is critical. Machines used here must support high throughput, carbonated and non-carbonated liquids, and handle PET, glass, or aluminum bottles. Features like clean-in-place (CIP) systems and anti-foaming filling nozzles are essential.
Common applications:
Water bottling
Soft drink filling
Juice bottling with pulp
Alcoholic beverages
2. Dairy Sector
Milk, flavored milk, curd, and buttermilk require filling machines that maintain product freshness and comply with FSSAI and dairy hygiene standards. These machines often include pasteurization links and automatic sealing systems.
3. Cosmetics and Toiletries
In cosmetic production, products like face wash, oils, lotions, serums, and creams have varying viscosities. Machines for this sector require flexible filling heads and nozzles designed to avoid air bubbles and foam formation.
4. Pharmaceutical Industry
Here, the focus is on sterile filling, precise volume, and contamination control. Machines should comply with cGMP, FDA, and USP Class VI standards. Most use laminar airflow, HEPA filters, and automatic reject systems for defect handling.
5. Agrochemical and Industrial Oils
Highly viscous and often corrosive liquids require machines built with chemical-resistant SS316L, anti-corrosive gaskets, and flameproof enclosures.
Innovative Features in Modern Bottle Filling Machines
1. Servo-Controlled Volumetric Filling
This allows for precise control over fill volume and speed, significantly improving fill accuracy and repeatability.
2. Multi-Head Filling Systems
Multiple synchronized nozzles fill several bottles at once, dramatically increasing productivity. Machines may offer 4, 6, 8, 12, or 24-head configurations depending on production scale.
3. Touchscreen HMI and PLC Integration
Operators can easily adjust parameters, store recipes, and troubleshoot problems using user-friendly interfaces.
4. Automatic Bottle Detection Sensors
These ensure that filling occurs only when a bottle is properly placed under the nozzle, preventing product loss.
5. No-Bottle, No-Fill Technology
A smart feature that helps avoid wastage when a bottle is missing from the conveyor.
6. Drip-Free Nozzles
These are designed with shut-off valves or pneumatic actuators to avoid any droplet formation after the fill cycle ends.
Bottle Orientation and Filling Line Integration
Many filling machines are integrated with other systems such as:
Automatic bottle unscramblers
Rinsing and sterilization tunnels
Capping machines
Induction sealing units
Shrink sleeve applicators
Automatic labeling systems
Case packing and palletizing robots
The integration of these systems enables a complete, end-to-end bottling solution that reduces labor costs and increases line efficiency.
Performance Optimization Tips
To ensure your machine operates at peak efficiency:
Routine Maintenance: Follow scheduled preventive maintenance, including oiling, checking sensor calibration, and inspecting wear parts.
Spare Parts Readiness: Keep a stock of consumables such as O-rings, gaskets, and nozzles.
Operator Training: Well-trained operators reduce downtime and ensure optimal machine performance.
Data Logging and Analysis: Use PLC and SCADA systems to monitor key performance indicators like bottle per minute rate, fill error rate, and rejection statistics.
Continuous Upgrades: Add modules or upgrade software for increased efficiency and future-proofing.
Sustainability and Green Bottling Solutions
With rising global emphasis on sustainability, manufacturers are adopting:
Energy-efficient motors to reduce power usage
Lightweight PET packaging compatibility
Minimal product residue systems
Eco-friendly construction materials
Automated cleaning systems that use less water and chemicals
Compliance and International Standards
Look for machines that conform to:
CE (European Conformity)
GMP (Good Manufacturing Practices)
FDA (Food and Drug Administration – for U.S. markets)
BIS (Bureau of Indian Standards)
ISO 9001 and ISO 22000
Meeting these ensures smooth export processes and increases consumer trust.
Conclusion
A bottle filling machine is more than just equipment—it's the foundation of a productive and scalable manufacturing process. Whether you're a small business or a global brand, choosing the right machine ensures consistent quality, minimal downtime, and long-term cost efficiency.
Note: IndiBlogHub features both user-submitted and editorial content. We do not verify third-party contributions. Read our Disclaimer and Privacy Policyfor details.