Cement Grinding Mills Revolutionizing the Construction Industry
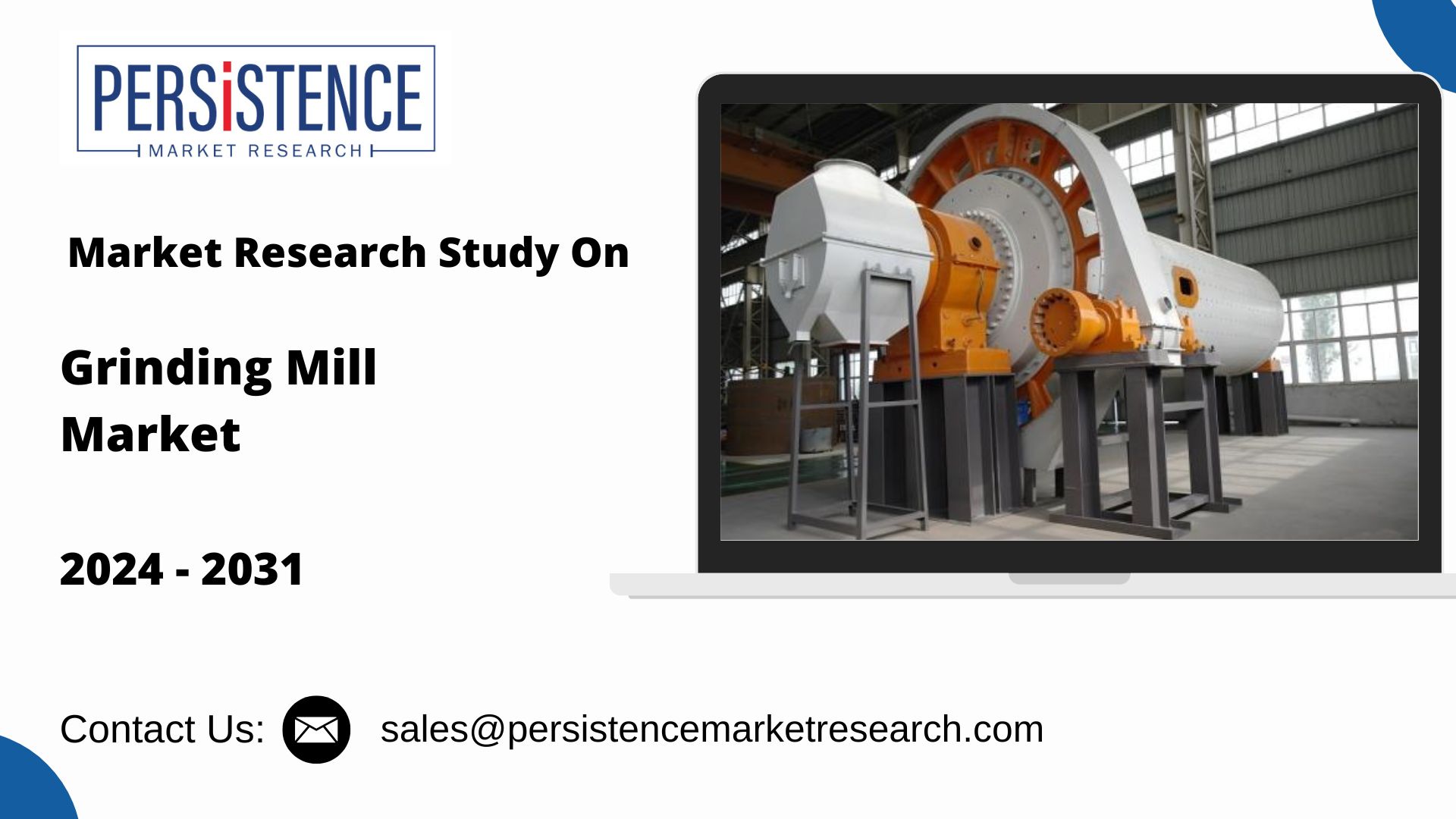
Cement, often referred to as the "backbone of the construction industry," plays an indispensable role in building infrastructure, from residential homes to large-scale commercial projects. A critical component in cement production is the grinding process, where raw materials like limestone, clay, and gypsum are finely ground to produce the desired consistency and quality.
In this context, cement grinding mills market, particularly vertical and ball mills, are vital in ensuring that cement production is efficient, cost-effective, and sustainable.
The cement industry, one of the largest industrial sectors worldwide, is undergoing a transformation with the introduction of advanced grinding technologies. These innovations in cement grinding mills are not only improving the quality of the final product but also enhancing the energy efficiency and environmental performance of cement plants. In this article, we explore how cement grinding mills are revolutionizing the construction industry and driving growth and sustainability.
What are Cement Grinding Mills?
Cement grinding mills are machines used to finely grind raw materials to produce cement. The milling process is essential for transforming raw materials into finely powdered substances that can then be mixed with water and other ingredients to form the final cement product. These mills typically come in two primary types:
Ball Mills: Traditional ball mills consist of a rotating cylinder filled with steel balls, which grind the raw material through a combination of impact and abrasion. Ball mills are commonly used in cement plants and are effective at producing the fine powders required for cement production.
Vertical Mills (Vertical Roller Mills): Vertical mills are a newer innovation in the cement grinding industry. These mills use rollers to crush and grind raw materials, with the grinding process occurring in a vertical orientation. Vertical mills are considered more energy-efficient and cost-effective than ball mills, offering advantages like higher throughput and reduced power consumption.
Key Trends Shaping the Cement Grinding Mills Market
1. Energy Efficiency and Cost Reduction
Energy efficiency is one of the most critical concerns in cement production, as the grinding process consumes a significant amount of energy. Cement plants, therefore, are increasingly investing in more energy-efficient grinding mills to reduce operational costs and minimize their carbon footprint. Vertical grinding mills, for example, have become popular due to their superior energy efficiency. These mills use less energy than traditional ball mills, which directly translates to cost savings for cement producers.
As cement producers are under growing pressure to reduce energy consumption and lower their operational costs, energy-efficient grinding mills play a pivotal role in enabling them to meet these challenges. The development of grinding mills with optimized grinding efficiency has thus become a central focus of innovation in the cement industry.
2. Automation and Digitalization
The integration of automation and digital technologies into cement grinding mills has significantly improved the operational efficiency of cement plants. Modern mills are now equipped with advanced control systems that optimize parameters such as speed, pressure, and temperature to ensure consistent product quality and improve overall performance.
Automation allows for better control over the grinding process, resulting in reduced energy consumption, lower emissions, and higher throughput. The use of artificial intelligence (AI) and machine learning (ML) in mill operations has also made it possible to predict and prevent equipment failure, thus reducing downtime and maintenance costs.
Furthermore, digitalization in cement plants enables real-time monitoring and data-driven decision-making, which enhances the efficiency of cement grinding mills. These innovations are not only enhancing the sustainability of cement production but are also setting new standards in the construction industry.
3. Sustainability and Reduced Carbon Emissions
Sustainability has become a key driver in the evolution of cement grinding mills. Cement production is one of the largest industrial sources of carbon dioxide (CO2) emissions globally. In response, there is increasing pressure on cement manufacturers to adopt more sustainable production practices, which include reducing emissions during the grinding process.
Advanced cement grinding mills are designed to minimize energy consumption and reduce CO2 emissions. For example, the introduction of alternative fuels and the use of waste-derived materials in the grinding process has gained traction. Additionally, the use of grinding aids โ substances that enhance the grinding process by reducing the energy required to break down materials โ is helping to further decrease energy consumption.
Furthermore, some modern grinding mills are designed to integrate with carbon capture and storage (CCS) technologies, helping to capture CO2 emissions before they are released into the atmosphere. As cement plants adopt these sustainable practices, the role of cement grinding mills in reducing the environmental impact of construction projects becomes increasingly important.
4. Higher Production Capacity and Improved Product Quality
The demand for cement is steadily increasing as global construction projects grow in scale. As a result, cement plants are looking for ways to enhance their production capacity without compromising on the quality of the final product. Cement grinding mills have evolved to accommodate these needs, with modern mills providing higher throughput and better control over product quality.
Vertical roller mills, in particular, have become essential in meeting the demand for higher production capacities. These mills are capable of grinding larger quantities of material more efficiently, producing a finer and more consistent product. Moreover, the ability to control product fineness more precisely allows manufacturers to produce high-quality cement that meets stringent industry standards.
The shift toward advanced grinding technologies is facilitating the scaling of cement production without sacrificing quality, thus supporting the global construction industry's growth.
5. Customization and Flexibility in Grinding Mills
Another key trend in the cement grinding mills market is the increasing demand for customized solutions. As construction projects become more specialized and complex, cement manufacturers are required to produce different types of cement with specific properties to meet the unique needs of the market.
Modern cement grinding mills offer greater flexibility in adjusting the grinding process to produce cement with various specifications, such as varying fineness levels or different chemical compositions. This customization capability allows manufacturers to meet the diverse demands of the construction industry, including the production of high-performance and specialized cement types for particular applications.
Regional Insights
1. Asia-Pacific: The Leading Market for Cement Grinding Mills
Asia-Pacific is the largest market for cement grinding mills, driven by the rapidly expanding construction and infrastructure sectors in countries like China, India, and Southeast Asia. As these countries continue to experience urbanization and industrialization, the demand for cement is expected to remain strong, thereby driving the need for efficient cement grinding technologies.
China, in particular, is one of the world's largest producers and consumers of cement, making it a key player in the global cement grinding mills market. As the country invests in new infrastructure projects, including transportation, housing, and commercial developments, the demand for high-quality cement and efficient grinding mills continues to rise.
2. Europe and North America: Focus on Sustainability and Efficiency
Europe and North America are also key markets for cement grinding mills, with an increasing emphasis on sustainability and energy efficiency. In these regions, stricter environmental regulations and the growing focus on reducing carbon emissions are pushing cement manufacturers to adopt more energy-efficient and environmentally friendly grinding technologies.
The integration of digital technologies and automation in cement plants is also more prominent in these regions, where advanced technologies are helping manufacturers optimize the performance of their grinding mills and reduce overall production costs.
Conclusion
Cement grinding mills are playing a crucial role in revolutionizing the construction industry by improving the efficiency, sustainability, and quality of cement production. As global demand for cement continues to rise, advanced grinding technologies, such as vertical roller mills, are enabling manufacturers to meet production targets while minimizing energy consumption and reducing environmental impact.
With the increasing demand for customized cement products and the integration of digital technologies and automation, the future of cement grinding mills looks promising. As the construction industry continues to expand, cement manufacturers who adopt these innovations will be well-positioned to meet the challenges of tomorrow's building projects and contribute to a more sustainable future for the industry.
Note: IndiBlogHub features both user-submitted and editorial content. We do not verify third-party contributions. Read our Disclaimer and Privacy Policyfor details.