Choose Carefully: The Potential of Continuous Flow Chemistry in API Synthesis
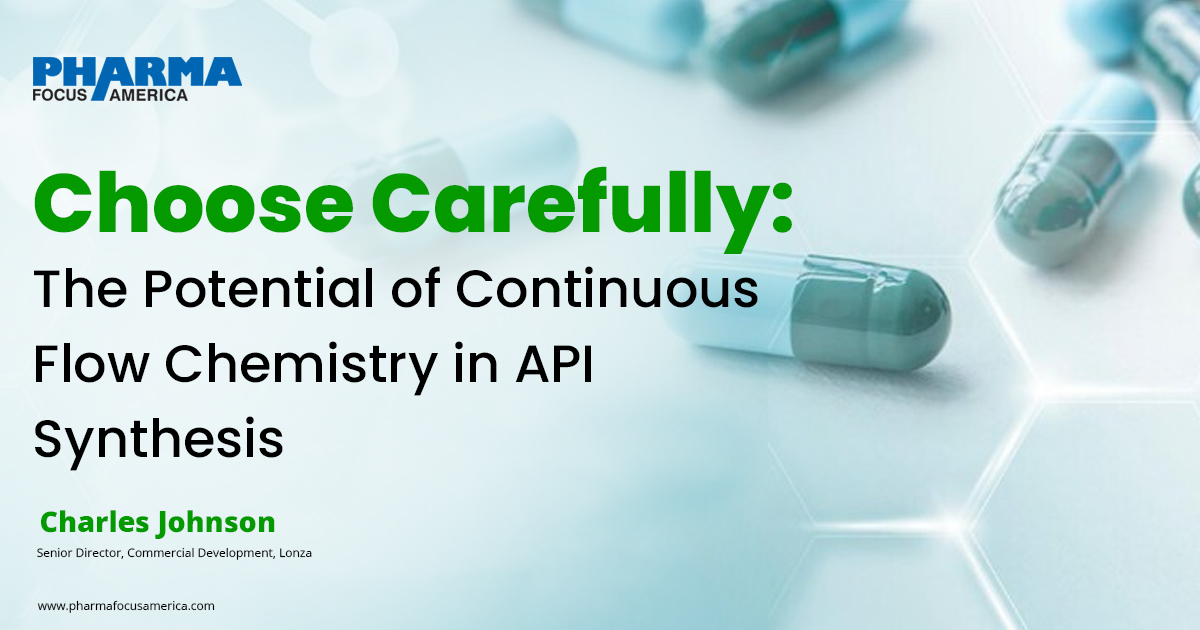
Author: Charles Johnson, Senior Director, Commercial Development, Lonza
Flow chemistry has huge potential in API manufacture, particularly for reactions that would be overly hazardous when run at scale as batch processes. This article will look at the mechanics behind flow chemistry and give examples of where it has been successfully employed to make APIs on a large scale.
The batch reactor has long been the mainstay of API manufacture for good reason. They are well understood, and many processes work very successfully in batch mode. Yet there are some reactions where running a batch process at a very large scale is less than ideal. High up the ‘best avoided’ list are reactions that are extremely exothermic, where running them on a large scale risks explosion in the event of a thermal runaway. But, equally, one of the reaction intermediates might be explosive, demonstrate auto-catalytic behaviour, or perhaps extremely toxic or otherwise hazardous, and handling large volumes might be considered unwise.
In such cases, the answer might lie in flow chemistry. The concept is not new and has been touted as the potential future for the manufacture of APIs for at least a couple of decades now without making widespread inroads in replacing batch vessels. But, given the right choice of project, flow chemistry has huge potential and has already been used at commercial scale in the manufacture of APIs and intermediates.
The key difference between a continuous flow reactor and a batch reactor is, of course, the volume of reagents that reside within the vessel at any one time. Batch reactors with a 10,000-liter capacity are not uncommon in a commercial environment, whereas the volume within a flow reactor might be as small as a few millilitres. In a batch process, the reaction mixture will usually remain within the reactor for several hours, whereas in a flow reactor, it will pass through quickly—the residence time is commonly a handful of seconds or a few minutes—and heat exchange is drastically increased. This short residence time also means the product is far less likely to decompose or to over-react and form side products.
Workup can also be carried out in flow if another device is connected in series, with the reaction mixture flowing from the reactor device directly into a workup device to quench the reaction. Multiple reaction steps can even be done in sequence by connecting another reactor (or reactors) after the first one.
Scaling up can be achieved simply by leaving a continuous flow reactor running for longer and, if necessary, running multiple reactors in parallel. This represents a further advantage: when scaling up a batch process, it is normal to sequentially scale up through multiple, increasingly large, vessels, with tweaks to the reaction conditions commonly being necessary. It is, of course, also possible to create a production-scale reactor that is a little larger than the one used in development to reduce the need for parallelisation.
With a flow process, the reaction conditions for an experimental scale will likely be identical to those for pilot scale and full-scale commercial production. This will speed up the overall development process, as much of the time required for optimisation is eliminated.
Reaction types
As a rule-of-thumb, when trying to decide what type of reactor to use for a particular process when switching from batch to continuous, the nature of the reaction should be considered carefully. Reaction characteristics can be split into three types, depending on their reaction rates and behaviour under standard operating conditions. Type A reactions proceed extremely quickly; they will have a half-life shorter than one second, and the rate will be controlled by mixing or mass transfer.
A type C reaction is much slower, typically taking 10 minutes or more to go to completion. The timescale can even be an hour or more. These slow, kinetically controlled reactions might benefit from being carried out in flow if there were safety considerations in play or if they are amenable to process intensification at higher temperature, pressure, reagent concentration, or a combination of these factors.
Learn more: https://www.pharmafocusamerica.com/manufacturing/choose-carefully-potential-continuous
Note: IndiBlogHub features both user-submitted and editorial content. We do not verify third-party contributions. Read our Disclaimer and Privacy Policyfor details.