CMM Systems Backbone of Precision Engineering in Aerospace
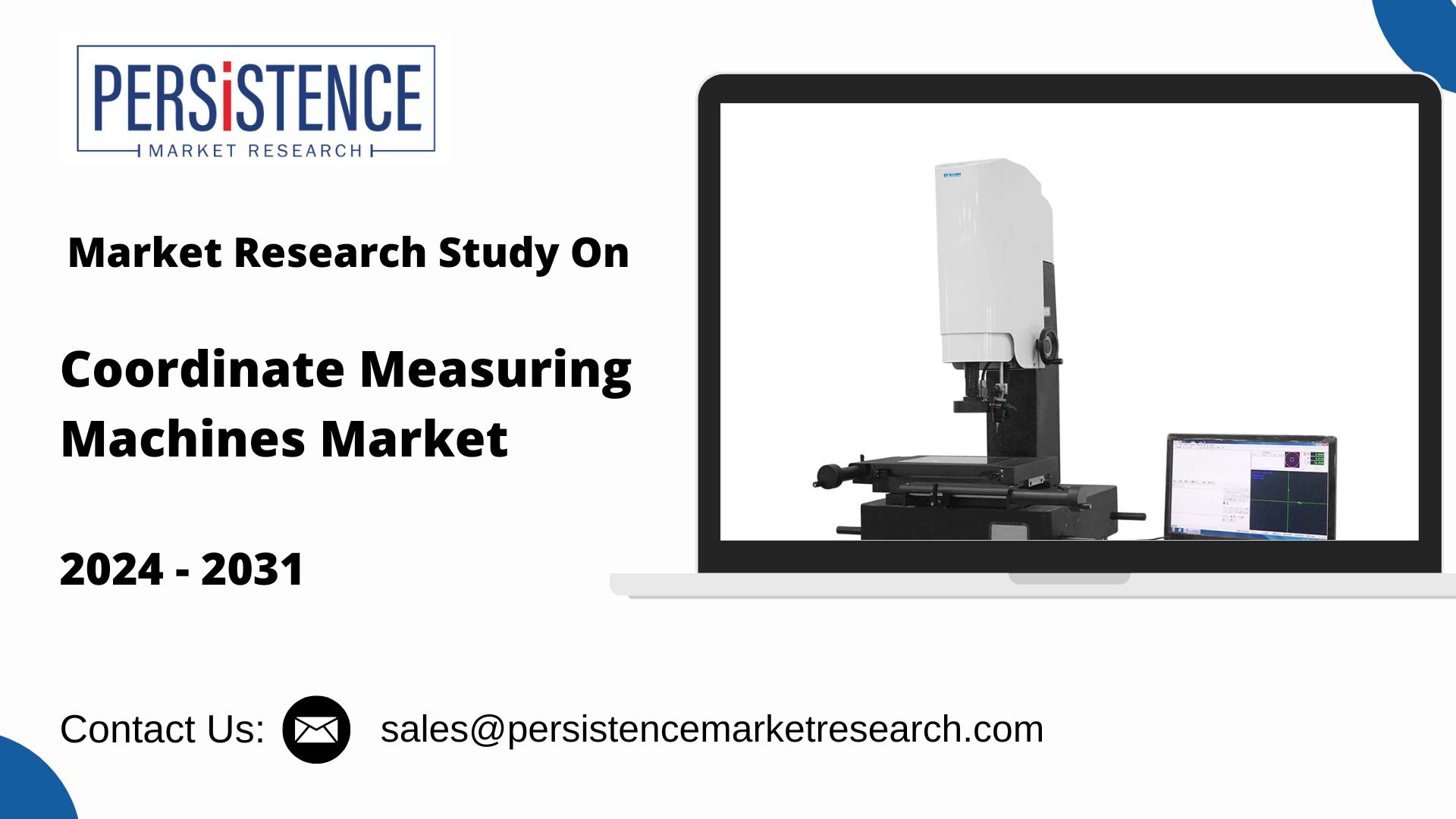
In the aerospace industry, precision engineering is paramount. The safety and efficiency of aircraft rely heavily on the accuracy of every component, from the smallest fasteners to the largest structural parts. At the heart of this precision engineering are Coordinate Measuring Machines (CMMs), which serve as critical tools for quality control and assurance in aerospace manufacturing. This article explores how CMM market systems are indispensable in the aerospace sector, highlighting their applications, benefits, and future trends.
Understanding CMM Systems
CMMs are advanced measurement devices used to measure the physical geometrical characteristics of an object. They can be operated manually or controlled via computer software, and they utilize various probing systems, including mechanical, optical, laser, and white light probes. CMMs provide highly accurate measurements of dimensions, shapes, and tolerances, making them essential in industries where precision is non-negotiable, such as aerospace.
The Role of CMMs in Aerospace Engineering
1. Quality Control and Assurance
Quality control is crucial in aerospace manufacturing due to the stringent safety regulations and standards imposed by governing bodies such as the Federal Aviation Administration (FAA) and the European Union Aviation Safety Agency (EASA). CMMs play a vital role in ensuring that all components meet these regulatory requirements. By providing precise measurements, CMMs help manufacturers:
Identify defects and deviations early in the production process.
Validate the integrity of components through rigorous testing.
Ensure that all parts fit together correctly, reducing the risk of assembly errors.
2. Reverse Engineering
In the aerospace industry, reverse engineering is often necessary to analyze existing components, improve designs, or reproduce obsolete parts. CMMs facilitate this process by:
Accurately scanning and measuring the dimensions of existing components.
Creating detailed 3D models that can be used for further design and analysis.
Allowing engineers to compare the scanned models with original CAD data to assess compliance with design specifications.
3. Prototyping and Tooling
CMMs are instrumental in the prototyping phase of aerospace projects. They assist engineers in verifying the accuracy of prototypes and tooling against their design specifications. This capability enables:
Rapid identification of design flaws before full-scale production.
Adjustments to tooling and fixtures to enhance manufacturability.
Improved collaboration between design and manufacturing teams through precise measurements.
4. Data Collection and Analysis
Modern CMMs are equipped with sophisticated software that allows for data collection and analysis in real-time. This feature is essential for:
Monitoring production processes to ensure consistent quality.
Collecting statistical data for Six Sigma and other quality improvement initiatives.
Analyzing measurement trends over time to identify potential issues and implement corrective actions proactively.
Benefits of CMM Systems in Aerospace
1. Enhanced Accuracy and Precision
CMMs provide exceptional accuracy, often achieving tolerances within microns. This level of precision is essential in aerospace, where even the slightest deviation can lead to catastrophic failures.
2. Increased Efficiency
Automated CMM systems significantly reduce measurement time compared to traditional methods. This increased efficiency allows manufacturers to accelerate production timelines without compromising quality.
3. Cost Savings
By identifying defects early in the manufacturing process, CMMs help reduce waste and rework costs. Additionally, the ability to produce high-quality components consistently leads to lower warranty claims and improved customer satisfaction.
4. Flexibility and Adaptability
CMMs can be adapted to measure a wide variety of aerospace components, from simple shapes to complex geometries. This flexibility makes them invaluable in a diverse industry where designs are continually evolving.
Future Trends in CMM Technology
1. Integration with Industry 4.0
The advent of Industry 4.0 is set to revolutionize manufacturing processes, including the use of CMMs. Integration with the Internet of Things (IoT) will enable real-time data sharing and analysis, improving decision-making and operational efficiency.
2. Artificial Intelligence and Machine Learning
The incorporation of AI and machine learning algorithms into CMM systems will enhance data analysis capabilities, allowing for predictive maintenance and intelligent quality control. These advancements will further improve the reliability and efficiency of measurement processes.
3. Portability and On-Site Measurements
The demand for portable CMM solutions is growing, enabling on-site measurements in the field or production floor. This trend will enhance flexibility and reduce the need for component transport, ultimately saving time and resources.
4. Advanced Sensor Technologies
As sensor technology continues to advance, CMMs will incorporate new measurement techniques, including laser scanning and optical measurement, providing even higher accuracy and faster measurement capabilities.
Conclusion
Coordinate Measuring Machines are undeniably the backbone of precision engineering in the aerospace industry. Their ability to ensure quality, facilitate reverse engineering, support prototyping, and provide valuable data analysis makes them indispensable tools in modern manufacturing. As CMM technology continues to evolve with advancements in AI, IoT, and sensor technologies, their role in ensuring the safety and reliability of aerospace components will only become more critical.
Embracing these innovations will empower aerospace manufacturers to maintain high standards of quality, enhance operational efficiency, and ultimately ensure the safety of the millions who rely on air travel every day. The future of aerospace manufacturing is undoubtedly intertwined with the ongoing development and integration of CMM systems, solidifying their status as essential components in the quest for excellence in precision engineering.
Note: IndiBlogHub features both user-submitted and editorial content. We do not verify third-party contributions. Read our Disclaimer and Privacy Policyfor details.