Collaborative Robots in Automotive Manufacturing: A Game-Changer
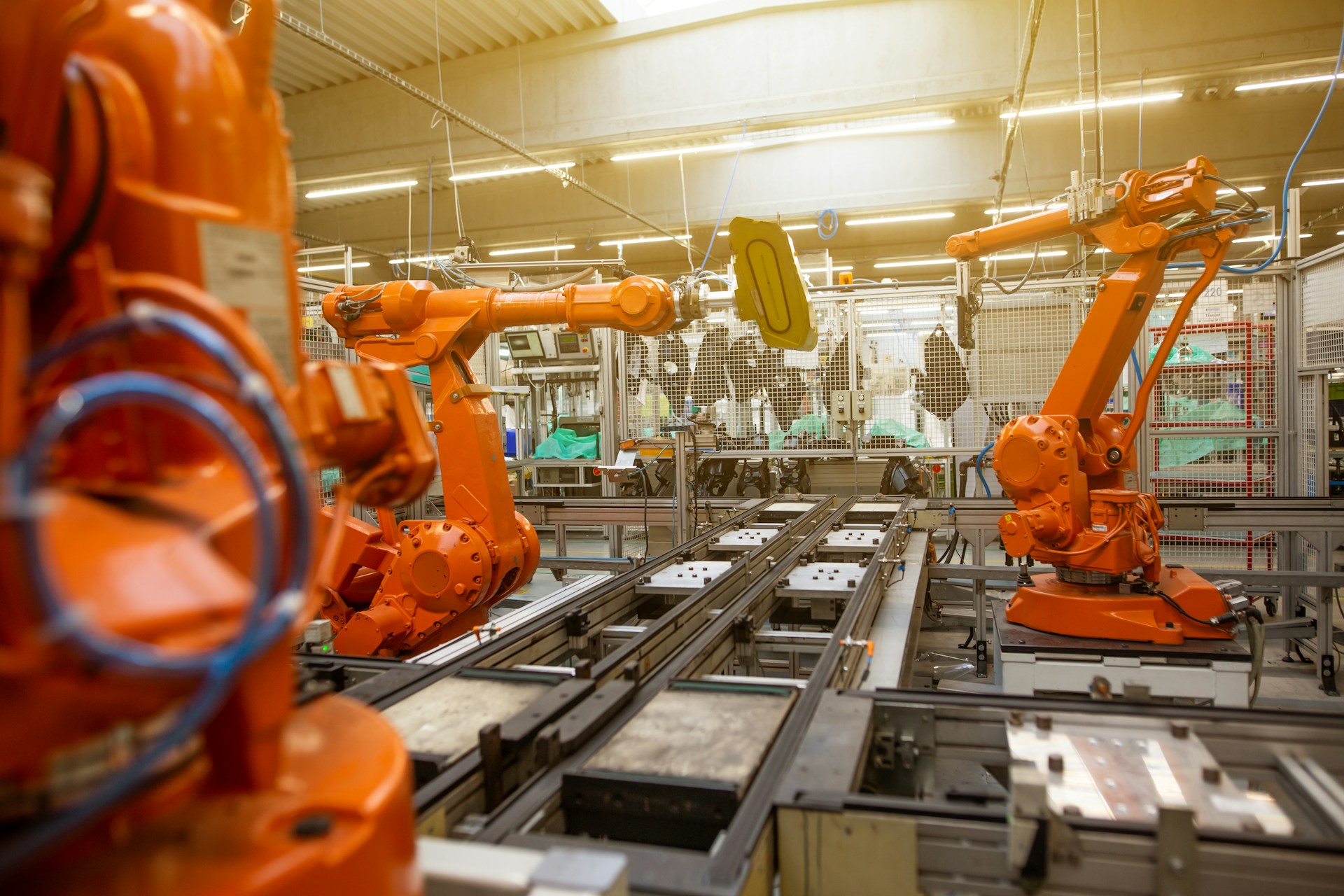
The automotive industry is undergoing a significant transformation as it embraces advanced technologies to enhance efficiency and productivity. Among these innovations, collaborative robots, or cobots, are proving to be game-changers in the manufacturing process. Designed to work alongside human operators, cobots are reshaping how vehicles are assembled, painted, and manufactured, leading to improved safety, flexibility, and overall production effectiveness.
The Rise of Automation in Automotive Manufacturing
Automation has been a cornerstone of the automotive industry for decades. From the introduction of the assembly line by Henry Ford to the use of traditional industrial robots in manufacturing plants, automation has continuously evolved. However, as consumer demands shift and the pace of production accelerates, manufacturers are increasingly turning to collaborative robots.
Cobots differ from traditional robots in that they are specifically designed to work alongside humans in a shared workspace. This shift reflects a growing recognition that combining human skills with robotic precision can lead to more efficient manufacturing processes. Today, automotive manufacturers are integrating cobots to meet the challenges of a dynamic market while maintaining high-quality standards. As the automotive industry continues to evolve, the integration of automotive robots has become essential for streamlining production processes, enhancing efficiency, and meeting the demands of a rapidly changing market.
Key Benefits of Collaborative Robots in Automotive Production
Collaborative robots bring a host of advantages to automotive production, enhancing efficiency and worker safety while offering the flexibility needed to meet modern manufacturing demands.
Enhanced Efficiency and Productivity
One of the primary advantages of collaborative robots is their ability to boost efficiency and productivity. Cobots can operate continuously without the need for breaks, allowing manufacturers to achieve higher output rates. Unlike traditional robots, which often require safety enclosures and complex programming, cobots are designed to be user-friendly, enabling faster deployment across various tasks.
For instance, cobots can assist in repetitive tasks such as part assembly, quality inspection, and material handling. By taking over these monotonous tasks, cobots free human workers to focus on more complex operations, ultimately leading to improved cycle times and overall production efficiency.
Improved Worker Safety and Ergonomics
Safety is a top priority in automotive manufacturing, where the risk of workplace injuries can be significant. Collaborative robots are engineered with safety features that allow them to work closely with human employees without the need for extensive safety barriers. This design promotes a safer work environment, reducing the likelihood of accidents.
Moreover, cobots are often used to assist with physically demanding tasks, such as lifting heavy components or repetitive motions that can lead to strain injuries. By sharing the workload, cobots help improve the overall ergonomics of the workplace.
Integrating Cobots into Existing Workflows
Successfully incorporating collaborative robots into existing manufacturing processes requires careful planning and a focus on creating synergies between human workers and robotic systems.
Seamless Integration with Human Workers
To maximize the benefits of collaborative robots, manufacturers must focus on integrating them seamlessly into existing workflows. This involves designing workspaces that promote collaboration between humans and cobots.
Additionally, training programs are essential to prepare employees for this technological shift. Providing workers with the skills needed to work alongside cobots ensures a smooth transition and enhances productivity. As workers become familiar with the capabilities of cobots, they can leverage these tools to enhance their own performance.
Overcoming Implementation Challenges
Despite the numerous advantages of collaborative robots, some challenges can arise during implementation. Common hurdles include resistance from workers who may fear job displacement and the initial investment required for new technologies. To overcome these challenges, manufacturers should communicate the benefits of cobots, emphasizing their role as tools that enhance human capabilities rather than replace them.
Technologies Driving Cobot Adoption
The rapid advancement of technology is a key factor in the increasing adoption of collaborative robots, enabling them to perform more complex tasks and integrate seamlessly into production environments.
The capabilities of collaborative robots are continually expanding, largely due to advancements in sensing and artificial intelligence (AI). Modern cobots are equipped with advanced sensors that enable them to perceive their environment and interact with human workers safely. These sensors allow cobots to detect obstacles, adjust their movements, and respond to changes in their surroundings in real time. This combination of sensing and AI makes cobots incredibly versatile, enabling them to handle complex assembly operations with precision.
The integration of real-time data analytics is another key driver behind the adoption of collaborative robots. By connecting cobots to a network of sensors and monitoring systems, manufacturers can collect valuable data on production processes. This data can be analyzed to identify bottlenecks, monitor equipment performance, and optimize workflows. By leveraging data analytics, automotive manufacturers can continuously improve their operations, ensuring they remain competitive in an evolving market.
Conclusion
In conclusion, the integration of collaborative robots in automotive manufacturing represents a pivotal advancement in the industry's evolution. By enhancing efficiency, improving worker safety, and offering unparalleled flexibility, cobots are redefining production processes and enabling manufacturers to respond swiftly to changing market demands.
As technological innovations continue to enhance the capabilities of cobots, their role in automotive production will only grow more significant. By fostering a collaborative environment that emphasizes human-robot interaction, manufacturers can not only optimize workflows but also empower their workforce to achieve greater heights of productivity and innovation.
Note: IndiBlogHub features both user-submitted and editorial content. We do not verify third-party contributions. Read our Disclaimer and Privacy Policyfor details.