Fluid Couplings in Mining Equipment Enhancing Performance and Safety
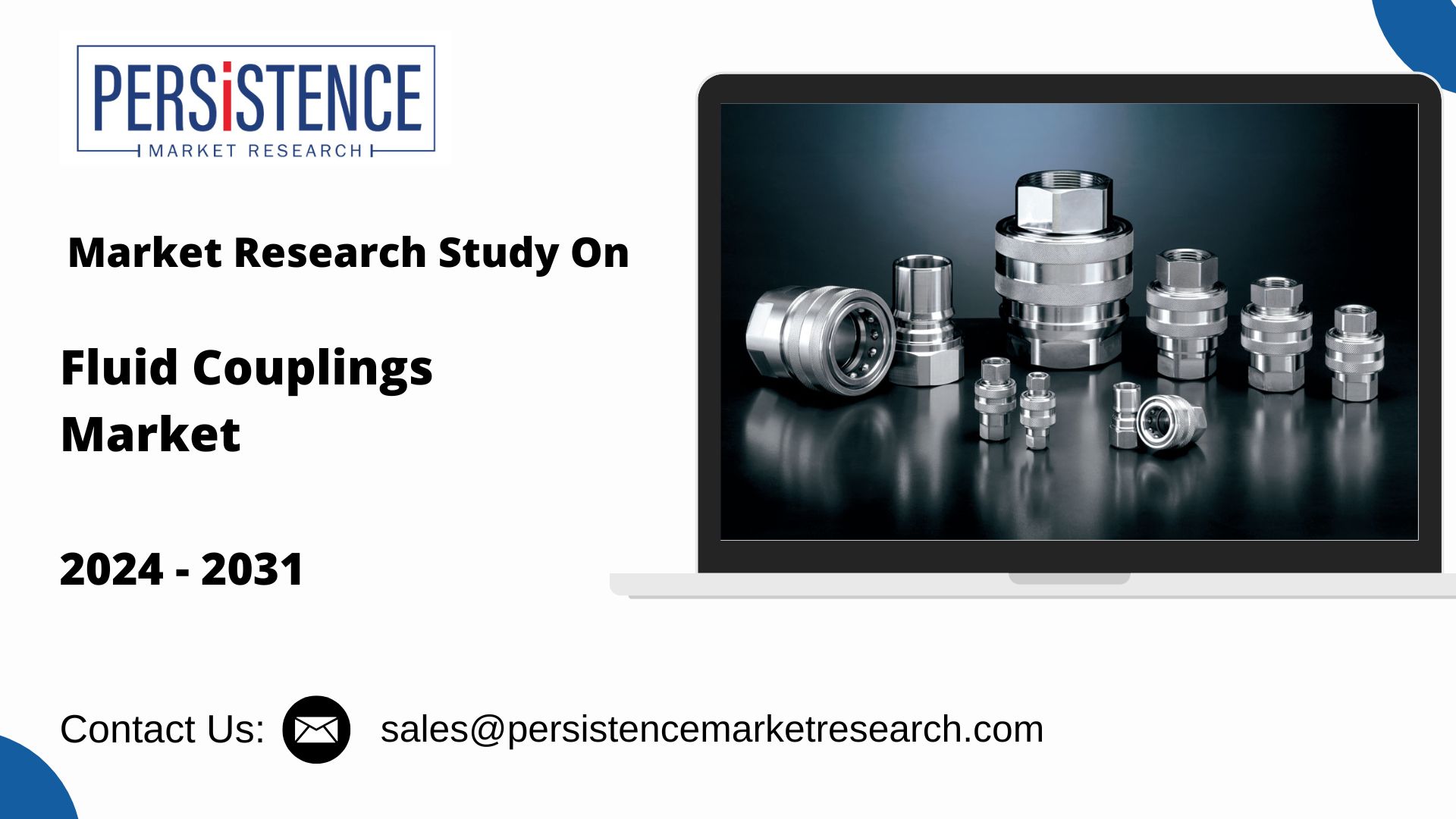
Mining is one of the most demanding industries, where heavy machinery operates under extreme conditions, handling massive loads, and enduring high levels of stress. As mining operations scale to meet growing global demand for minerals, optimizing machinery performance and ensuring the safety of operations have become top priorities. Fluid couplings have emerged as a vital component in mining equipment, playing a crucial role in enhancing performance, improving energy efficiency, and ensuring the safety of both machinery and personnel.
In this article, we will explore how fluid couplings market are transforming the mining industry, offering solutions that address key challenges and drive operational efficiency.
What Are Fluid Couplings?
Fluid couplings are mechanical devices used to transmit rotational power between two rotating shafts via hydraulic fluid. Unlike traditional mechanical couplings, which transfer power through direct physical contact, fluid couplings use the energy of a fluid medium to transmit torque. This allows for smoother operation and protects both machinery and personnel from the harsh stresses that typically occur in heavy-duty applications.
The two main components of a fluid coupling are the impeller (connected to the driving shaft) and the turbine (connected to the driven shaft), which are separated by hydraulic fluid. The impeller creates a flow of fluid that drives the turbine, transmitting torque while minimizing the risk of mechanical shock, vibration, and sudden load changes. Fluid couplings are widely used in industries requiring heavy-duty machinery, and mining is one of the most prominent sectors benefitting from this technology.
Enhancing Performance in Mining Equipment
Smooth Power Transmission
Mining equipment, such as crushers, conveyor belts, and grinding mills, often operates in environments where rapid acceleration and deceleration occur, leading to shocks that can damage machinery and affect productivity. Fluid couplings ensure smooth and gradual power transmission, preventing jerks or sudden torque surges that can be damaging to sensitive equipment.
By using hydraulic fluid to cushion the connection between the driving and driven parts, fluid couplings help maintain a steady, controlled transfer of power. This smooth operation not only protects the equipment from wear and tear but also contributes to better overall performance, increasing the operational uptime of mining machinery.
Energy Efficiency
Mining operations are energy-intensive, with energy costs often making up a significant portion of the operational budget. Fluid couplings improve energy efficiency by minimizing energy losses during power transmission. In traditional mechanical couplings, sudden torque spikes and load fluctuations can lead to excessive energy consumption. However, fluid couplings adjust automatically to load changes, allowing for more efficient energy use and reducing power losses.
In high-demand applications, such as crushers and mills, fluid couplings optimize the distribution of energy, ensuring that machinery uses only the power it needs for specific tasks. This adaptability leads to lower energy consumption, reduced operational costs, and a smaller carbon footprint, making fluid couplings an environmentally friendly choice for mining operations.
Protection Against Overload and Mechanical Stress
Mining equipment often faces extreme operational conditions, with sudden changes in load or torque potentially leading to mechanical failures. Fluid couplings provide a built-in safeguard by slipping or disengaging when the load exceeds a safe threshold. This overload protection prevents the machinery from experiencing dangerous torque spikes that could result in system failures, breakdowns, or costly repairs.
For example, if a conveyor belt is clogged or a crusher becomes jammed, the fluid coupling can reduce the transmission of excess torque to the driven parts, preventing damage to critical components such as motors, gearboxes, and shafts. This protection is especially important in mining, where the downtime caused by machinery failure can result in significant delays and financial losses.
Reduced Wear and Tear on Equipment
The mining industry deals with large volumes of abrasive materials, which subject equipment to constant wear and tear. Fluid couplings help reduce mechanical stresses on machinery by eliminating sudden shocks and vibrations that typically occur in traditional power transmission systems. By providing a smooth, cushioned transfer of energy, fluid couplings minimize the impact on sensitive components, extending the lifespan of mining equipment.
This reduction in mechanical stress means fewer breakdowns, less frequent repairs, and overall lower maintenance costs. As a result, mining companies benefit from reduced downtime and lower long-term operating costs, which contribute to improved profitability.
Improving Safety in Mining Operations
Minimizing Shock Loads and Vibration
Shock loads and vibrations are common causes of equipment failure and can present serious safety risks in mining environments. The rugged conditions and unpredictable nature of mining tasks, such as drilling, blasting, and material handling, often result in excessive mechanical stress. Fluid couplings help to minimize these risks by absorbing and damping shock loads, creating a smoother operating environment.
By preventing sudden torque surges, fluid couplings reduce the chances of equipment malfunction, improving the safety of workers and preventing accidents caused by equipment failure. Moreover, the reduced vibration ensures a more stable and secure working environment, reducing the risk of injury to personnel operating or maintaining machinery.
Preventing Overheating and System Failures
Mining equipment is exposed to high temperatures, heavy loads, and constant use, which can lead to overheating and system malfunctions. Fluid couplings provide an additional layer of protection by distributing heat evenly throughout the system and reducing the strain on components like motors and bearings. This not only helps maintain optimal operating conditions but also reduces the risk of overheating, which can cause equipment failures or fire hazards in certain environments.
Ensuring Operator Safety
Operators working with heavy mining machinery face significant risks due to the large-scale nature of the equipment and the extreme conditions under which it operates. The smooth, controlled power transfer provided by fluid couplings ensures that machines start and stop without sudden jerks or unanticipated movements, making it easier for operators to manage the machinery safely. The reduced vibrations and shocks also make the operating environment less physically taxing, reducing fatigue and improving worker safety.
Applications of Fluid Couplings in Mining Equipment
Fluid couplings are used in various mining equipment, from crushers and mills to conveyors and draglines. Here are some specific applications where fluid couplings enhance performance and safety:
Crushers: Crushers experience high torque loads, which can cause significant wear on components. Fluid couplings provide smooth torque transmission, preventing overloads and reducing wear on gears, motors, and shafts.
Conveyor Systems: Conveyors are essential in transporting materials throughout the mining process. Fluid couplings protect against shock loads that can occur when the conveyor belt is overloaded, ensuring smooth operation and reducing the risk of belt slippage.
Ball Mills and Grinding Mills: Mills operate under heavy loads and need efficient power transmission systems to prevent equipment failure. Fluid couplings help protect the motors and gears in these high-demand environments by offering a gradual transmission of power.
Draglines and Shovels: In large-scale mining operations, draglines and shovels require precise control and load management. Fluid couplings offer the necessary protection and efficiency, improving the longevity of these machines and ensuring smooth operation in difficult conditions.
Conclusion
Fluid couplings are an indispensable technology in the mining industry, offering substantial benefits in terms of performance, safety, and efficiency. By providing smooth power transmission, protecting against overloads, and reducing mechanical stress, fluid couplings enhance the reliability and longevity of mining equipment. Additionally, their ability to minimize shock loads, vibrations, and energy consumption makes them a valuable tool for improving operational efficiency and reducing costs.
As the mining industry continues to evolve and face increasing demands, fluid couplings will play an essential role in helping companies optimize their operations while ensuring the safety of their workforce and the longevity of their equipment. With advancements in fluid coupling technology, the future of mining operations is set to be even more efficient, sustainable, and safe.
Note: IndiBlogHub features both user-submitted and editorial content. We do not verify third-party contributions. Read our Disclaimer and Privacy Policyfor details.