Foundry Chemicals Market Trends, Size, Growth, Challenges and Forecast 2030
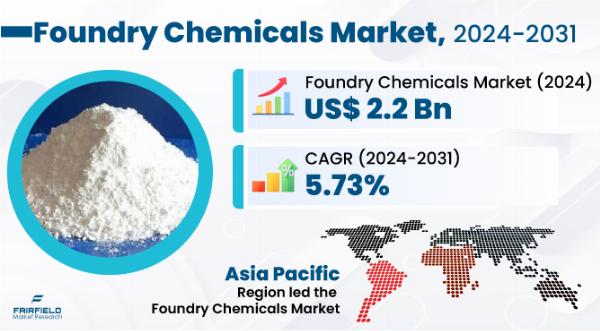
Global foundry chemicals market size is forecasted to reach a substantial US$3.25 billion by 2031, marking a significant increase from the anticipated US$2.2 billion by the end of 2024.
1. Remarkable Expansion: Market revenue is expected to exhibit a remarkable rate of expansion, with an estimated Compound Annual Growth Rate (CAGR) of 5.73% during the period from 2024 to 2031.
For more information: https://www.fairfieldmarketresearch.com/report/foundry-chemicals-market
Key Growth Drivers:
1. Increasing Demand from Automotive and Aerospace Industries: The automotive and aerospace sectors continue to drive demand for high-quality castings, necessitating superior foundry chemicals. With a focus on producing components capable of withstanding extreme conditions, advanced foundry chemicals play a crucial role in ensuring the durability and performance of materials used in these industries.
2. Technological Advancements and Sustainability: Ongoing innovations in foundry processes are resulting in the development of new chemicals that not only enhance casting quality but also align with environmental sustainability goals. As the industry increasingly emphasizes eco-friendly practices, there is a growing need for chemicals that minimize environmental impact while complying with regulatory standards and supporting corporate sustainability objectives.
3. Growth of Emerging Markets: Industrialization in regions such as Asia, Africa, and South America is fueling demand for machinery, vehicles, and infrastructure, consequently boosting the foundry industry and chemical market. The expansion into these new markets fosters global growth, driving up demand for foundry chemicals as manufacturing capabilities in these regions continue to evolve.
Major Growth Barriers:
1. Environmental Regulations and Compliance Costs: Stringent environmental regulations worldwide are presenting significant challenges for the foundry industry, resulting in additional costs for manufacturers as they adopt cleaner technologies and modify processes to comply with regulations.
2. Fluctuating Raw Material Prices: Volatility in raw material prices, particularly those derived from petroleum products and minerals, can lead to increased production costs and reduced profitability for foundry chemical manufacturers, impacting their bottom line.
3. Adoption of Alternative Technologies: Advancements in alternative casting technologies, such as 3D printing for metal parts, pose a potential threat to traditional foundry processes and chemicals. These alternative methods offer advantages in waste reduction, efficiency, and complex design production, thereby challenging the dominance of conventional foundry practices.
Key Trends and Opportunities:
1. Sustainability and Eco-friendly Products: The growing emphasis on sustainability is driving innovation in the development of biodegradable binders, water-based coatings, and chemicals that minimize emissions. This trend aligns with the demand from environmentally conscious industries and regulatory requirements for eco-friendly solutions.
2. Digitalization and Smart Foundries: The integration of digital technologies is optimizing production processes, reducing waste, and enhancing quality control in foundries. This shift towards smart manufacturing offers opportunities for the development of products compatible with automated processes, leading to increased efficiency and reduced downtime.
3. Expansion in Emerging Markets: Rapid industrial growth in emerging markets presents opportunities for tailored products and strategies to meet specific regional needs. Market players can capitalize on this growth by developing localized solutions and establishing strong footholds in these regions.
4. Development of High-performance and Specialty Chemicals: The increasing demand for high-quality components creates opportunities for the development of chemicals offering unique properties such as enhanced heat resistance or reduced shrinkage. Market players can differentiate themselves by offering specialized solutions that cater to specific industry requirements.
Regional Frontrunners:
1. Asia Pacific: With a dominant 40% market share, Asia Pacific, led by China's expanding industries, remains a powerhouse in the global market. The region's growth is further fueled by rising urbanization and manufacturing activities in countries like India.
2. Europe: Europe holds approximately 30% of the global market share, leveraging its established manufacturing base and growing focus on environmental sustainability. Major European players are at the forefront of eco-friendly solutions, driving innovation in the region.
3. North America: With a mature market and a strong presence in industries such as automotive and aerospace, North America offers steady growth opportunities. Continued focus on technological advancements can further propel the market forward in this region.
Leaders in the Foundry Chemicals Space: The foundry chemicals space is populated by several key players driving innovation and market growth. Some notable leaders include Vesuvius, SQ Group, Ask Chemicals, Asahi Yukizai Corporation, KAO Chemicals, IVP Limited, Hüttenes-Albertus International, Mancuso Chemicals Limited, Mazzon SpA, Fincast Foundry Flux Co., Ceraflux India Pvt. Ltd., and Hindusthan Adhesive & Chemicals, among others.
Note: IndiBlogHub features both user-submitted and editorial content. We do not verify third-party contributions. Read our Disclaimer and Privacy Policyfor details.