HDPE Injection Molding: Processes, Properties, and Applications
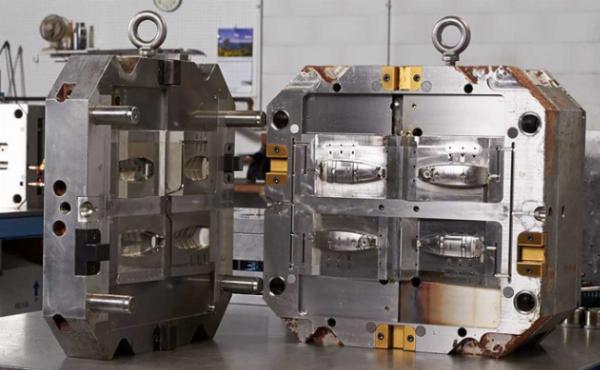
High-density polyethylene (HDPE) is one of the most versatile and widely used thermoplastic materials in the injection molding industry. Known for its excellent balance of strength, flexibility, and chemical resistance, HDPE is a material of choice for a wide range of products. This article provides a comprehensive overview of HDPE injection molding, including the properties of HDPE, the injection molding process, and its applications across various industries.
1. Understanding HDPE
What is HDPE?
High-density polyethylene (HDPE) is a thermoplastic polymer made from the monomer ethylene. It is characterized by a linear structure with minimal branching, which contributes to its high density (typically between 0.93 and 0.97 g/cm³). This structure gives HDPE a high strength-to-density ratio, making it one of the most durable and widely used types of polyethylene.
Key Properties of HDPE:
Strength and Rigidity: HDPE has excellent tensile strength and stiffness, making it suitable for products that require durability and the ability to withstand mechanical stress.
Chemical Resistance: HDPE is highly resistant to a wide range of chemicals, including acids, alcohols, and bases. This makes it ideal for applications involving chemical exposure.
Low Moisture Absorption: HDPE’s low moisture absorption rate ensures that it maintains its mechanical properties even in wet environments, making it suitable for both indoor and outdoor applications.
Impact Resistance: HDPE has good impact resistance, even at low temperatures, which is crucial for products exposed to harsh environmental conditions.
Ease of Processing: HDPE is relatively easy to process using standard injection molding equipment, which contributes to its widespread use in manufacturing.
2. The HDPE Injection Molding Process
Material Preparation:
Before the injection molding process begins, HDPE resin in the form of pellets is prepared. These pellets are often dried to remove any moisture that could affect the molding process and the final product quality.
Injection Molding Machine Setup:
Hopper: The HDPE pellets are fed into the machine through a hopper, which funnels them into the barrel.
Barrel and Screw: Inside the barrel, the pellets are heated to the appropriate melting temperature (typically between 180°C and 230°C, depending on the grade of HDPE). The screw rotates within the barrel, mixing and pushing the molten HDPE forward.
Mold Clamping: The mold, which defines the shape of the final product, is held tightly closed by a clamping unit. The clamping force must be sufficient to keep the mold closed during the injection of the molten HDPE.
Injection Phase:
The molten HDPE is injected into the mold cavity under high pressure. The pressure ensures that the material fills the entire cavity, capturing all the details of the mold design.
Cooling and Solidification:
Once the mold is filled, the material begins to cool and solidify. HDPE has a relatively low shrinkage rate, but the cooling process must be carefully controlled to prevent warping or dimensional inaccuracies in the final product.
Ejection and Post-Processing:
After cooling, the mold is opened, and the solidified part is ejected. The part may then undergo post-processing steps, such as trimming excess material (known as flash), surface finishing, or assembly with other components.
3. Advantages of HDPE Injection Molding
Cost-Effectiveness:
HDPE is a cost-effective material, particularly when used in high-volume production. The material's low cost, combined with the efficiency of the injection molding process, makes it ideal for producing large quantities of parts at a relatively low cost per unit.
Versatility:
HDPE's balance of properties makes it suitable for a wide range of applications. It can be easily molded into complex shapes with fine details, which is essential for producing both functional and aesthetic components.
Durability:
Products made from HDPE exhibit excellent durability, making them suitable for long-term use in demanding environments. HDPE's resistance to impact, chemicals, and moisture ensures that it maintains its integrity over time, even under harsh conditions.
Recyclability:
HDPE is fully recyclable, which contributes to its sustainability. Used HDPE products can be melted down and reprocessed into new items, reducing the environmental impact of plastic production.
4. Challenges in HDPE Injection Molding
Shrinkage and Warping:
While HDPE has a relatively low shrinkage rate compared to other plastics, it is still susceptible to shrinkage and warping if not cooled properly. Uneven cooling can lead to internal stresses in the part, causing it to warp as it solidifies. This challenge can be mitigated through careful control of cooling rates and mold design.
Mold Wear:
The high pressures and temperatures involved in HDPE injection molding can cause wear on the mold over time, especially if the mold is used for high-volume production. Regular maintenance and the use of durable mold materials can help extend the life of the mold.
Part Design Considerations:
Designing parts for HDPE injection molding requires careful consideration of factors such as wall thickness, flow paths, and draft angles. Inconsistent wall thickness can lead to uneven cooling and potential defects, while inadequate draft angles can make it difficult to eject the part from the mold.
5. Applications of HDPE Injection Molding
Packaging Industry:
HDPE is widely used in the packaging industry to produce containers, bottles, and caps for a variety of products, including food, beverages, chemicals, and household goods. Its chemical resistance and moisture barrier properties make it ideal for preserving the contents.
Consumer Goods:
HDPE is used to manufacture a wide range of consumer goods, such as toys, household items, and outdoor furniture. Its durability and impact resistance ensure that these products can withstand regular use and exposure to the elements.
Construction Materials:
In the construction industry, HDPE is used for products such as piping, fittings, and geomembranes. HDPE pipes are particularly valued for their resistance to corrosion and chemical degradation, making them suitable for transporting water, gas, and other fluids.
Automotive Industry:
HDPE injection molding is used to produce a variety of automotive components, including fuel tanks, interior panels, and protective covers. The material's lightweight nature contributes to improved fuel efficiency, while its impact resistance enhances safety.
Agriculture:
In agriculture, HDPE is used for irrigation piping, containers, and other equipment that requires resistance to environmental conditions. HDPE’s durability and chemical resistance ensure that these products can withstand exposure to sunlight, water, and fertilizers.
Medical Devices:
HDPE is also used in the medical field to produce items such as drug delivery systems, surgical trays, and laboratory equipment. Its chemical resistance and ability to be sterilized make it suitable for use in environments where hygiene and durability are critical.
6. Future Trends in HDPE Injection Molding
Material Innovations:
Ongoing research into HDPE formulations is leading to the development of new grades with enhanced properties, such as improved impact resistance, higher stiffness, and better environmental stress crack resistance (ESCR). These innovations are expanding the range of applications for HDPE.
Sustainability Initiatives:
As sustainability becomes increasingly important, there is a growing focus on using recycled HDPE (rHDPE) in injection molding processes. Advances in recycling technologies are improving the quality of rHDPE, making it a viable alternative to virgin HDPE in many applications.
Process Automation:
The integration of automation and Industry 4.0 technologies into HDPE injection molding processes is enhancing efficiency and quality control. Automated systems can optimize material usage, monitor production parameters in real-time, and reduce waste, making the process more cost-effective and environmentally friendly.
Conclusion
HDPE injection molding is a highly versatile and efficient manufacturing process that produces durable, high-quality parts for a wide range of industries. The material’s excellent balance of strength, chemical resistance, and ease of processing, combined with the efficiency of injection molding, makes it a popular choice for many applications. While there are challenges, such as controlling shrinkage and maintaining mold integrity, the benefits of HDPE injection molding ensure its continued relevance in the manufacturing sector. As material innovations and sustainability practices evolve, HDPE injection molding will continue to be a cornerstone of modern production techniques.
Note: IndiBlogHub features both user-submitted and editorial content. We do not verify third-party contributions. Read our Disclaimer and Privacy Policyfor details.