How Closed-Cell Foam Enhances Building Envelope Integrity
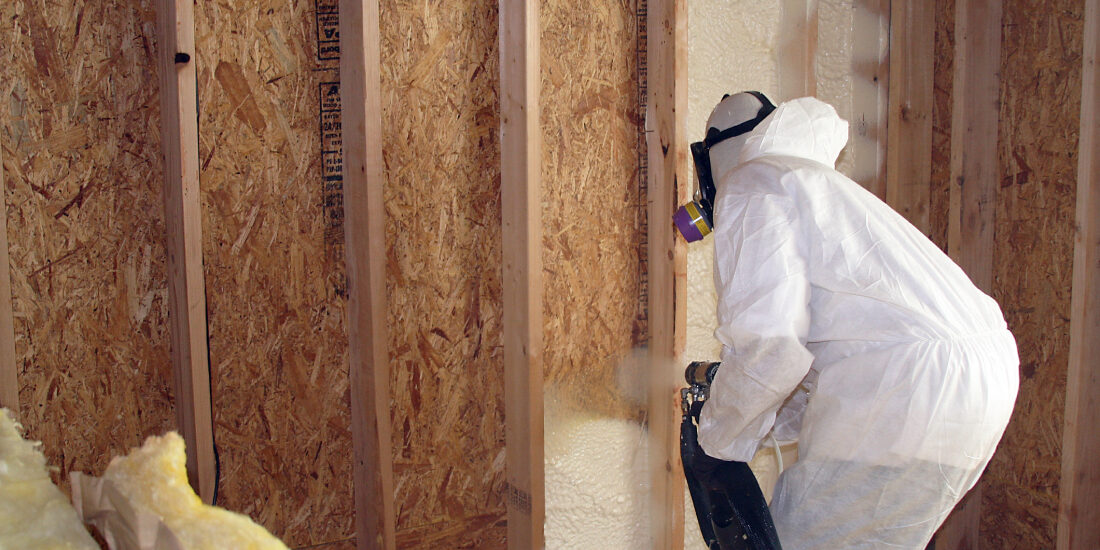
Closed-cell foam improves building envelope integrity by creating an airtight, moisture-resistant barrier that simultaneously insulates and strengthens the structure. This rigid foam material expands to fill gaps and cracks, forming a continuous air and thermal barrier with R-values of 6-7 per inch, effectively preventing energy loss while adding structural rigidity. When properly installed, closed-cell foam can reduce energy costs by 25-50% while extending building durability by preventing moisture infiltration that leads to rot, mold, and structural damage.
This high-performance closed-cell spray foam insulation solution addresses multiple building envelope challenges simultaneously, making it particularly valuable in extreme climates and high-moisture environments where maintaining structural integrity alongside energy efficiency is crucial.
Properties of Closed-Cell Foam Insulation
Closed-cell foam insulation contains millions of tiny closed cells filled with gas that gives the material its distinctive properties. Unlike open-cell foam where cells connect, closed-cell foam's individual sealed cells create its rigid structure and impressive performance characteristics.
This combination of properties creates a multifunctional building material that simultaneously insulates, air-seals, controls moisture, and reinforces structural elements. According to the Department of Energy, air leakage can account for 30-40% of heating and cooling costs in typical buildings, making closed-cell foam's air-sealing properties particularly valuable.
Building Envelope Components Enhanced by Closed-Cell Foam
Closed-cell foam significantly improves several critical components of the building envelope, working as a system to increase overall performance:
Wall Assemblies: When applied between studs, closed-cell foam creates a continuous thermal and air barrier that virtually eliminates thermal bridging through framing members. This comprehensive coverage prevents the energy loss that occurs with traditional insulation methods that leave gaps around electrical boxes, plumbing penetrations, and irregular framing.
Roof Systems: Applied to the underside of roof decking, closed-cell foam prevents both air and moisture movement while adding structural strength. This capability is particularly valuable in high-wind regions, where testing has shown properly installed closed-cell foam can increase roof uplift resistance by 50% or more.
Foundation and Below-Grade Applications: Closed-cell foam's moisture resistance makes it ideal for basements, crawlspaces, and other below-grade applications where water intrusion is a concern. It creates a continuous barrier that blocks soil gases like radon while providing thermal insulation.
Building Transitions: Areas where different building components meet—like rim joists where walls connect to foundations—are particularly vulnerable to air infiltration and thermal bridging. Closed-cell foam excels at sealing these complex junctions that are difficult to insulate effectively with traditional materials.
Bonus Tip: When planning closed-cell foam insulation, consider using a "flash and batt" hybrid approach in non-critical areas to reduce costs while maintaining performance. This method uses a thinner layer of closed-cell foam (1-2 inches) for air sealing and moisture control, followed by less expensive fiberglass or mineral wool to achieve the desired total R-value.
Moisture Management Benefits
One of closed-cell foam's most significant contributions to building envelope integrity is its comprehensive moisture management capabilities:
Bulk Water Resistance: Unlike many insulation materials that absorb moisture, closed-cell foam repels liquid water. This property makes it suitable for flood-prone areas, where it can help wall assemblies recover more quickly after short-term flooding events.
Vapor Control: With sufficient thickness (typically 2 inches or more in most climate zones), closed-cell foam functions as a Class II vapor retarder. This characteristic helps control vapor diffusion through building assemblies, reducing condensation risk within walls and roofs.
Air-Transported Moisture: By sealing air leakage pathways, closed-cell foam eliminates a primary mechanism for moisture movement in buildings. This air sealing prevents warm, humid air from contacting cold surfaces within assemblies where condensation could occur.
Capillary Breaks: The closed-cell structure resists capillary water movement, creating effective separation between moisture-susceptible building materials.
A study by the Building Science Corporation found that wall assemblies with closed-cell foam maintained 70% lower moisture content during extreme weather testing compared to traditional fiberglass insulation assemblies, significantly reducing the risk of mold and wood rot.
Structural Enhancement Capabilities
Beyond its insulation and air-sealing properties, closed-cell foam provides notable structural benefits:
Wall Racking Strength: Testing by the National Association of Home Builders Research Center demonstrates that walls insulated with closed-cell spray foam have up to 300% greater racking strength than walls with traditional insulation. This increased rigidity helps buildings withstand high winds and seismic events.
Roof Deck Attachment: When sprayed to the underside of roof decking, closed-cell foam adheres the decking to rafters and trusses, creating a more unified structure that resists uplift forces during high winds.
Framing Protection: By controlling moisture movement and condensation, closed-cell foam helps preserve wood framing members from moisture damage that can degrade structural integrity over time.
Bonus Tip: For maximum structural benefit in high-wind or seismic zones, work with an engineer to calculate the appropriate closed-cell foam thickness and density needed to achieve specific structural reinforcement goals beyond basic insulation requirements.
Things to Consider Before Making a Decision
Before selecting closed-cell foam for your building envelope strategy, consider these important factors:
Climate Zone Requirements: The optimal insulation strategy varies by location. In cold climates, closed-cell foam's high R-value and vapor control properties offer significant advantages, while in mild climates, the cost premium may exceed the performance benefit.
Budget Considerations: With installation costs ranging from $1.50-$3.00 per board foot (significantly higher than traditional insulation), closed-cell foam represents a substantial investment. Calculate long-term energy savings against upfront costs to determine ROI for your specific project.
Installation Implications: Quality installation requires specialized equipment and trained technicians. Poor installation can result in inadequate coverage, improper curing, and potential off-gassing issues. Research contractor qualifications thoroughly.
Environmental Factors: Traditional closed-cell foams use hydrofluorocarbon (HFC) blowing agents with high global warming potential. Newer water-blown and hydrofluoroolefin (HFO) formulations offer significantly reduced environmental impact but may have slightly different performance characteristics.
Code Compliance: Building codes often require thermal barriers (typically 1/2" gypsum board) over foam insulation for fire safety. Some applications may require ignition barriers as well. These requirements add cost and complexity to installation.
Space Constraints: In retrofit applications, the thickness of closed-cell foam needed to achieve desired R-values may reduce interior space more than desired.
Common Questions About Closed-Cell Foam
How does closed-cell foam compare to other insulation types for building envelope performance?
Closed-cell foam outperforms traditional insulation in creating a comprehensive building envelope system because it addresses thermal resistance, air infiltration, and moisture control simultaneously. While materials like fiberglass or cellulose may offer good R-value per dollar, they don't provide closed-cell foam's air sealing, moisture control, or structural benefits without additional components and labor.
Is closed-cell foam worth the additional cost over other insulation options?
The value proposition depends on your specific requirements. Buildings in extreme climates, moisture-prone environments, or high-wind zones gain significant performance benefits that often justify the premium cost through energy savings, damage prevention, and extended building life. For mild climate zones with simple building designs, the cost premium may exceed the performance benefit.
Can closed-cell foam cause moisture problems in walls or roofs?
Properly installed closed-cell foam rarely causes moisture problems—it typically prevents them. However, in retrofit applications or certain wall assemblies, its vapor-impermeable nature could potentially trap moisture if installed on the wrong side of an assembly relative to climate zone. Working with a knowledgeable designer familiar with building science principles ensures proper application.
How much closed-cell foam do I need for effective building envelope improvement?
The required thickness varies by climate zone and application. For thermal performance alone, thickness should be calculated based on target R-value (remembering closed-cell foam provides R-6 to R-7 per inch). For vapor control properties, a minimum of 2 inches is typically required in most climates. For structural benefits, engineering calculations should determine appropriate thickness.
How long will closed-cell foam last in my building?
Properly installed closed-cell foam maintains its performance characteristics for the life of the building, typically 50+ years. Unlike some traditional insulation materials, it doesn't settle, compress, or degrade under normal conditions. The air sealing and moisture control benefits help extend the service life of the building itself by protecting structural components.
Make the Right Decision
Expert Spray Foam insulation contractor offers unmatched building envelope performance by simultaneously addressing thermal efficiency, air infiltration, moisture management, and structural integrity. This comprehensive approach eliminates the need for multiple building products and reduces the risk of performance gaps that occur when separate systems don't integrate perfectly.
Evaluate your specific climate challenges, building design complexity, performance goals, and budget constraints to determine if closed-cell foam's premium performance justifies its higher cost for your project. For buildings in challenging environments or where long-term durability is paramount, closed-cell foam often provides the most complete building envelope solution available, despite its premium cost.
Reviewer
Reviewer: Lily Johnson offered her feedback after reviewing this post. With 8 years in the spray foam insulation field, her suggestions centered around improving outreach to homeowners looking for quality insulation solutions.
Note: IndiBlogHub features both user-submitted and editorial content. We do not verify third-party contributions. Read our Disclaimer and Privacy Policyfor details.