How to Avoid Weld Lines in Injection Molding: A Comprehensive Guide
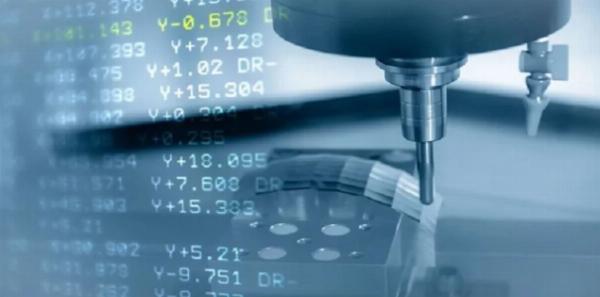
Weld lines, also known as knit lines, are a common defect in injection molding that can affect the appearance, strength, and functionality of molded parts. These lines occur when two or more flow fronts of molten plastic meet and solidify unevenly. Understanding how to prevent weld lines is crucial for achieving high-quality parts with optimal performance. This article explores the causes of weld lines, strategies for avoiding them, and best practices for achieving defect-free injection molding.
Understanding Weld Lines
Weld lines are visible lines or marks on the surface of a molded part where two or more streams of molten plastic have fused together. They are typically characterized by:
Visual Defects: Weld lines can appear as faint lines or seams on the surface of the part, often with discoloration or surface imperfections.
Mechanical Weakness: Parts with weld lines may exhibit reduced mechanical strength and impact resistance due to the incomplete fusion of plastic streams.
Functional Issues: In critical applications, weld lines can affect the part's functionality and performance, leading to potential failure in use.
Causes of Weld Lines
Several factors contribute to the formation of weld lines in injection molding:
Flow Fronts Meeting: Weld lines occur when two or more streams of molten plastic meet in the mold cavity but do not fuse together completely. This can happen when the flow fronts are too far apart or when the plastic cools too quickly before they merge.
Mold Design: Poorly designed molds can contribute to weld lines. Factors such as inadequate gate locations, flow channel design, and mold temperature can impact how the plastic flows and solidifies.
Material Properties: The choice of material affects how it flows and solidifies in the mold. Materials with high viscosity or low melt flow index may be more prone to weld lines.
Injection Speed and Pressure: Insufficient injection speed or pressure can lead to incomplete filling of the mold and weak fusion of flow fronts.
Cooling Conditions: Uneven cooling or excessively high cooling rates can cause differential cooling rates at weld line locations, leading to defects.
Strategies to Avoid Weld Lines
To minimize or prevent weld lines, consider the following strategies:
Optimize Mold Design
Gate Placement: Position gates strategically to ensure that molten plastic flows towards the weld line area and minimizes the distance between flow fronts. This helps in achieving better fusion at the meeting point.
Flow Path Design: Design the mold with balanced flow paths to ensure that molten plastic fills the cavity uniformly and reduces the likelihood of weld lines.
Rib and Boss Placement: Place ribs and bosses in locations that do not obstruct the flow of molten plastic. This helps in reducing flow interruptions and minimizes the formation of weld lines.
Adjust Injection Parameters
Increase Injection Speed: Increasing the injection speed helps in achieving a more uniform flow front and reduces the chances of incomplete fusion. However, ensure that the speed is adjusted within the capabilities of the molding machine and material.
Optimize Injection Pressure: Adequate injection pressure ensures that the mold cavity is filled completely and helps in achieving better fusion at potential weld line locations. Adjust the pressure based on the material and mold requirements.
Control Injection Time: Adjusting the injection time helps in ensuring that the plastic fills the mold cavity before it starts to cool. Properly timed injection minimizes the risk of weld lines.
Manage Mold Temperature
Uniform Temperature: Maintain a consistent and uniform mold temperature to ensure even cooling of the part. Uneven cooling can contribute to weld line formation. Use mold temperature controllers to regulate the temperature effectively.
Optimize Cooling Channels: Design and place cooling channels to promote uniform cooling throughout the mold cavity. Proper cooling channel design helps in reducing thermal gradients and minimizing weld lines.
Select the Right Material
Material Properties: Choose materials with appropriate melt flow characteristics for the specific application. Materials with better flow properties are less prone to weld lines.
Additives: Consider using additives or impact modifiers that enhance the flow and fusion of molten plastic. These additives can improve the overall quality and reduce the occurrence of weld lines.
Conduct Mold Flow Analysis
Simulation Software: Utilize mold flow analysis software to simulate the injection molding process and predict potential weld line locations. This allows you to make design adjustments before manufacturing the mold.
Analyze Flow Patterns: Study the flow patterns in the simulation to identify areas where weld lines are likely to form. Optimize the mold design and injection parameters based on the analysis results.
Perform Regular Maintenance
Mold Maintenance: Regularly inspect and maintain molds to ensure they are free of wear, damage, or debris that can affect the flow of molten plastic. Proper maintenance helps in achieving consistent part quality and minimizing weld lines.
Machine Calibration: Ensure that the injection molding machine is properly calibrated and maintained to achieve accurate control of injection parameters.
Best Practices for Weld Line Prevention
Prototype Testing: Use prototype molds to test designs and parameters before committing to full-scale production. This helps in identifying and addressing potential weld line issues early in the development process.
Quality Control: Implement a robust quality control process to monitor the appearance and performance of molded parts. Regular inspections and testing help in detecting weld lines and other defects.
Training and Expertise: Invest in training for mold designers and operators to ensure they understand the factors contributing to weld lines and how to prevent them. Expertise in mold design and process optimization is crucial for achieving high-quality parts.
Continuous Improvement: Continuously review and improve the injection molding process based on feedback, performance data, and technological advancements. Adopting best practices and staying updated with industry trends helps in achieving consistent part quality.
Conclusion
Weld lines in injection molding can pose challenges to part quality and performance. By understanding the causes of weld lines and implementing effective strategies to avoid them, manufacturers can achieve high-quality, defect-free parts. Optimizing mold design, adjusting injection parameters, managing mold temperature, selecting the right material, and utilizing simulation tools are essential practices for preventing weld lines.
Note: IndiBlogHub features both user-submitted and editorial content. We do not verify third-party contributions. Read our Disclaimer and Privacy Policyfor details.