How to Choose the Right Circular Slitting Blades for Your Slitting Machine
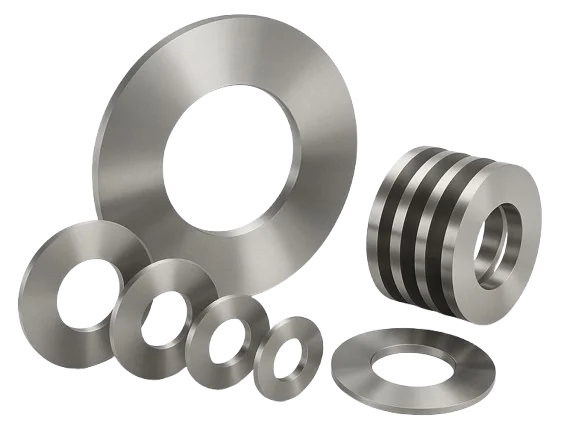
In the world of industrial cutting and slitting operations, Circular Slitting Blades play a critical role in determining the precision, efficiency, and cost-effectiveness of your production process. Whether you're slitting paper, plastic, metal, or textiles, selecting the right circular slitting blade is not just about fitting it into the machine; it's about optimizing performance and ensuring long-term reliability.
In this blog, we’ll help you understand the various factors that go into selecting the right circular slitting blades for your slitting machine and why making an informed decision can make or break your cutting operation.
Why the Right Circular Slitting Blade Matters
The efficiency of your slitting machine depends on the quality and compatibility of the blade. A poorly matched or worn-out blade can result in jagged cuts, product wastage, frequent downtime, and even damage to the machinery.
The Correct Circular Slitting Blade Ensures:
- Clean and precise cuts
- Reduced machine wear
- Fewer blade changes
- Improved productivity
- Better material yield
Selecting the ideal blade is a balance between the blade material, coating, geometry, and the nature of the material being processed.
1. Understand Your Material and Application
Before selecting a blade, it's crucial to analyze the type of material you intend to cut. Different materials have distinct physical properties, such as hardness, thickness, and tensile strength, which affect the choice of blade.
Examples:
- For thin plastic films, a sharper, finer blade is recommended.
- For metal foils, a blade made of hardened steel is necessary to resist wear.
- For corrugated boards, a toothed or serrated blade might be appropriate.
Tip: Always match the blade specification to the material to avoid tear-outs, delamination, or fuzzy edges.
2. Choose the Right Blade Material
The blade's composition determines its durability, sharpness, and resistance to wear.
Common Blade Materials:
- Tool Steel (D2, M2, etc.): Excellent edge retention, suitable for cutting paper, film, and soft metals.
- High-Speed Steel (HSS): Offers superior heat resistance, making it ideal for high-speed applications.
- Carbide Blades: Known for hardness and longevity, ideal for abrasive materials or high-precision cuts.
- Ceramic Blades: Extremely sharp and wear-resistant, though brittle. Useful for specialty applications.
Pro Tip: If you experience excessive wear or require precise cuts, consider upgrading from carbon steel to carbide or coated options for enhanced performance.
3. Pay Attention to Blade Geometry
Essential Features to Consider:
- Blade Diameter: Must match the machine's specifications.
- Thickness: Impacts cut precision and compatibility with the material.
- Edge Profile: Choose from standard, toothed, or beveled edges based on application.
- Bore Size: Ensure a snug fit to the spindle to prevent wobbling.
Types of Edges:
- Flat edges: Ideal for simple slit cuts.
- Beveled edges (single or double): Offer cleaner cuts and less burr formation.
- Toothed edges: Work well for cutting fibrous or layered materials.
A mismatch in blade geometry can lead to poor performance and unnecessary wear on both the blade and machine.
4. Consider Coatings and Surface Treatments
Advanced coatings can enhance the performance and lifespan of circular slitting blades, especially in challenging environments.
Popular Coatings:
- TiN (Titanium Nitride): Reduces friction and increases hardness.
- TiAlN (Titanium Aluminum Nitride): Provides excellent heat and oxidation resistance.
- CrN (Chromium Nitride): Ideal for corrosion-prone environments.
These coatings reduce adhesive wear and blade build-up, resulting in longer-lasting, cleaner cuts.
5. Know Your Slitting Method: Shear, Crush, or Razor Slitting?
The method of slitting also plays a crucial role in selecting the blade.
- Shear Slitting: Uses a male/female knife setup. Best with high-precision, clean cuts on film, paper, and foil. Requires extremely sharp and well-aligned blades.
- Crush Cutting: A duller blade presses against an anvil. Suitable for non-wovens and textiles. Needs a durable and thick blade.
- Razor Slitting: Uses razors for thin plastic films. Blades must be ultra-sharp but are generally disposable.
Each slitting method has its blade requirement in terms of sharpness, thickness, and material hardness.
6. Evaluate Blade Tolerance and Balancing
Precision-manufactured circular slitting blades with tight tolerances ensure:
- Better cut consistency
- Reduced vibration
- Longer equipment life
Look for dynamically balanced blades, especially for high-speed applications. Poorly balanced blades can cause vibration, resulting in uneven cuts and premature wear.
7. Don’t Ignore Manufacturer Reputation and Customization Options
Choosing a reliable supplier for your circular slitting blades is just as important as the blade itself. A reputable manufacturer, like Maxwell Slitter, provides:
- Blades made from premium materials
- Custom dimensions and tolerances
- Expert consultation on application-based needs
- After-sales support and quality assurance
Customization is particularly valuable if you’re working with specialized or uncommon materials, or if your slitting operation is unique in design or purpose.
8. Maintenance and Replacement Tips
Even the best blade needs maintenance. Monitor your slitting performance and inspect blades regularly.
Signs it’s time to replace your blade:
- Increased burrs or frayed edges
- Material jamming or sticking
- Blade vibration or noise
- Decreased throughput or speed
Sharpening is possible for many steel and carbide blades, but always consult your manufacturer for best practices. Regular replacement avoids costly downtime and ensures consistent cut quality.
Conclusion: Invest Smart in Your Circular Slitting Blades
Choosing the right Circular Slitting Blades for your slitting machine isn't just a technical decision; it’s a strategic one. By considering your material type, cutting method, blade material, geometry, and surface coating, you can significantly enhance both the performance and longevity of your cutting operation.
With the right blade, you reduce waste, increase production speed, and ensure consistently high-quality cuts. And with expert support from leading suppliers like Maxwell Slitter, you gain access to tailored solutions that perfectly align with your operational needs.
Visit Maxwell Slitters to explore our full range of industrial-grade circular slitting blades built for precision and performance.
Note: IndiBlogHub features both user-submitted and editorial content. We do not verify third-party contributions. Read our Disclaimer and Privacy Policyfor details.