How to Choose the Right Tugger Cart System for Your Warehouse Layout
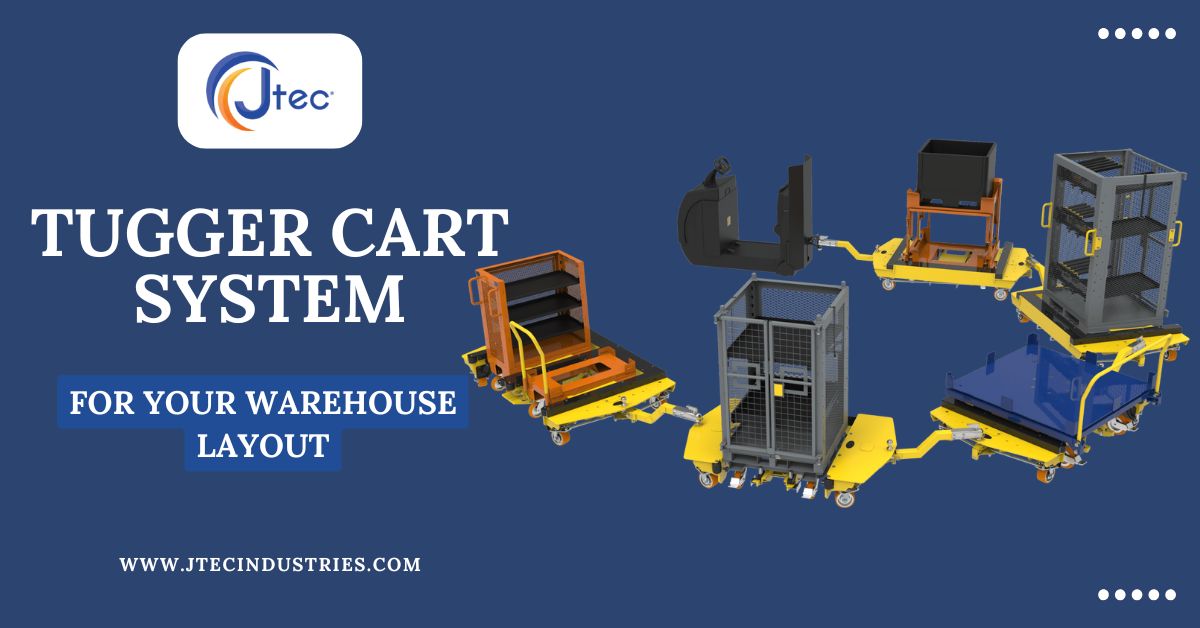
Effective material handling is key to keeping a warehouse organized and productive. One popular solution for moving items quickly and safely across a warehouse is a tugger cart system. Tugger carts are connected carts to a motorized vehicle (or tugger) that can transport materials in bulk, reducing the need for multiple trips and helping workers complete tasks more efficiently. Choosing the right tugger cart system, however, requires careful consideration of several factors, from warehouse layout to the types of materials being transported. Here’s a guide to help you make the best choice.
Analyze Your Warehouse Layout
Start by looking at the layout of your warehouse. Different layouts call for different tugger cart configurations, so it’s essential to match the system to your specific space:
Open Spaces: If your warehouse has wide, open areas, you may benefit from larger tugger carts or systems that can pull multiple carts in a train. This setup allows for high-volume transport and fewer trips.
Narrow Galleries: For warehouses with narrow galleries, compact tugger systems or carts with improved turning abilities are a better choice. Smaller, more flexible carts can navigate tight spaces more easily, making the transport process smoother.
Mixed Layouts: Warehouses with open spaces and narrow galleries may need a more adaptable system. Consider using a modular tugger cart system that can be adjusted for different warehouse sections, ensuring maximum efficiency in any layout.
Choosing a system that fits your layout will allow for safe and effective material movement.
Determine the Type and Volume of Materials
Think about the type and quantity of materials you’ll be moving. Tugger cart systems come in a variety of shapes and load capacities to meet different material handling needs:
Heavy Loads: For warehouses that handle heavy items, choose a tugger cart system with a strong build and a high weight limit. Ensure the carts are specifically rated to carry the weight of your usual loads.
Delicate Goods: If your warehouse frequently handles delicate items, look for carts with secure compartments, padding, or shock-absorbing features to reduce the risk of damage during transport.
Variety of Materials: If you have mixed loads—such as heavy, light, and delicate items—consider a modular system. Modular carts allow customization, so you can switch up the configuration based on your transport needs.
Matching the cart system to the materials ensures safe handling and reduces the risk of accidents or product damage.
Choose the Right Cart Size and Configuration
Cart size and layout are essential to consider as they directly impact efficiency. Think about how much space each cart will occupy and what cart design works best for your items:
Standard Carts: Standard-sized carts are often easier to manage and work well if your loads are generally consistent. They’re also a simpler, straightforward choice if you don’t need specialized setups.
Customizable Carts: Some systems allow you to customize the cart size or structure. This can be especially helpful if your inventory varies in size or shape, as it allows for flexible, adaptable transport options.
Flatbed vs. Shelved Carts: If you primarily transport bulky items, flatbed carts provide a stable platform. For smaller or more organized storage, consider shelved carts. These can keep items organized and separated, reducing the risk of mix-ups during transport.
Selecting the right cart type will help you optimize warehouse space and transport efficiency.
Think About Transport Frequency
How often you need to move materials within your warehouse also affects your choice. Some systems are better suited for high-frequency use, while others work well for occasional transport:
Frequent Use: For warehouses that require continuous material transport, invest in durable carts made from high-quality materials. Carts and tuggers that can resist regular use will prevent frequent breakdowns and delays.
Occasional Use: If your transport needs are less frequent, a lighter-duty system may be sufficient. Lighter systems are generally more cost-effective and easier to maintain, while still meeting occasional needs.
Selecting a system built for your transportation frequency helps ensure that trains last longer and operate efficiently.
Evaluate Maneuverability and Safety
Maneuverability is another important factor, especially in warehouses with complex layouts. Here’s what to consider:
Turning Radius: If your warehouse has tight spaces, opt for a tugger cart system with a small turning radius. This makes it easier to navigate sharp corners or narrow galleries, improving transport times and minimizing disruptions.
Braking System: A good braking system is necessary for safe operation. Reliable brakes allow tuggers to stop smoothly, reducing the risk of accidents in high-traffic areas.
Safety Features: Some tugger carts have additional safety features, such as warning lights, alarms, or emergency stop buttons. These can help prevent collisions, especially in busy environments.
Prioritizing maneuverability and safety features reduces the risk of accidents and ensures safe operation across your warehouse.
Decide Between Manual and Automated Systems
Tugger cart systems are available in both manual and automated options. The right choice depends on your warehouse’s needs and your budget:
Manual Systems: Manual tuggers are operated by workers and are often more affordable and flexible. They’re a good choice for warehouses with moderate transport needs, as they can be used on-demand without requiring additional setup.
Automated Guided Vehicles (AGVs): Automated systems, or AGVs, use programmed paths or sensors to navigate without a human driver. These systems can operate continuously making them ideal for high-volume or 24/7 warehouses. While AGVs require a higher initial investment, they can improve productivity in the long term.
Automated systems are useful in high-demand environments, whereas manual systems offer flexibility and cost savings for smaller companies.Â
Factor in Budget and Maintenance
Finally, consider your budget and maintenance needs. Tugger systems vary widely in price based on features and durability:
Prioritize Must-Have Features: Create a list of key features based on your warehouse-specific requirements and prioritize them within your budget.Â
Research Brands and Models: Compare models from different manufacturers to find the best value for money. Some brands may offer reliable systems at competitive prices.
Plan for Maintenance: Don’t forget to factor in maintenance costs. Choosing durable systems may reduce the need for frequent repairs, saving money in the long run.
Finding the right tugger cart system requires balancing your budget with the features and capabilities your warehouse needs.
Conclusion
Selecting the right tugger cart system for your warehouse layout can make a big difference in efficiency, safety, and productivity. By analyzing your layout, material type, cart size, frequency of transportation, mobility requirements, automation options, and budget, you can choose a system that perfectly suits your operations. A well-suited tugger cart system not only streamlines material handling but also contributes to a safer and more organized work environment.
Read More: The Role of Material Handling Carts in Streamlining Production Lines
Note: IndiBlogHub features both user-submitted and editorial content. We do not verify third-party contributions. Read our Disclaimer and Privacy Policyfor details.