How to Design for Injection Molding: A Comprehensive Guide
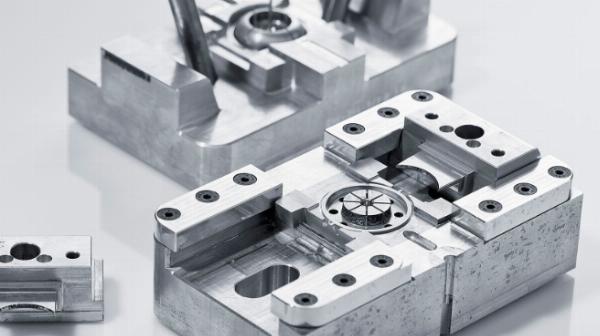
Injection molding is a widely used manufacturing process for creating complex parts with high precision and efficiency. This process involves injecting molten material into a mold cavity, allowing it to cool and solidify, and then ejecting the finished part. To ensure successful outcomes in injection molding, it’s crucial to follow specific design principles and considerations. This guide will walk you through the essential aspects of designing for injection molding, helping you optimize your designs for quality, functionality, and manufacturability.
Understanding the Basics of Injection Molding
Injection molding is suitable for producing a variety of parts, from small intricate components to large structural pieces. The key components of an injection molding system include the injection machine, the mold, and the material. The injection machine melts the material, which is then injected into the mold cavity. The mold, typically made from steel or aluminum, determines the shape of the final part. After the material cools and solidifies, the mold opens, and the part is ejected.
Key Design Principles for Injection Molding
Material Selection
The choice of material significantly impacts the performance and cost of the molded part. Common materials include thermoplastics like ABS, polycarbonate, and polypropylene, and thermosetting plastics like epoxy and phenolic. Consider the material’s mechanical properties, thermal resistance, and chemical compatibility when designing your part.
Design for Manufacturability
Draft Angles: Incorporate draft angles in your design to facilitate easy removal of the part from the mold. Typically, a draft angle of 1 to 3 degrees is recommended to prevent sticking and ensure smooth ejection.
Wall Thickness: Maintain uniform wall thickness to avoid issues like warping and sink marks. Variations in wall thickness can lead to uneven cooling, causing defects.
Radii and Fillets: Use radii and fillets instead of sharp corners to reduce stress concentrations and improve material flow during molding. This also helps in reducing mold wear and extending mold life.
Designing for Cooling Efficiency
Efficient cooling is crucial for reducing cycle times and ensuring dimensional accuracy. Design the mold with cooling channels that evenly distribute cooling fluid around the cavity. This helps in achieving uniform cooling and minimizing thermal gradients. Use simulation tools to analyze cooling patterns and optimize channel placement.
Draft Angles and Ejection Mechanisms
Draft Angles: Implement appropriate draft angles (typically 1-2 degrees) to ensure easy ejection of the part from the mold. Insufficient draft angles can lead to difficulty in part removal and increased wear on the mold.
Ejection Mechanisms: Consider incorporating ejector pins, air ejectors, or hydraulic ejectors in your mold design to assist with the removal of parts. Ensure that the ejection mechanism does not damage the part or affect its appearance.
Minimize Undercuts
Undercuts are features that prevent the part from being easily ejected from the mold. To avoid this, design your part with features that can be produced without requiring complex mold mechanisms. If undercuts are necessary, consider using side cores or lifters in the mold design.
Design for Assembly and Functionality
Interlocking Features: Design parts with interlocking features or snap fits to reduce the need for additional assembly steps. This can streamline the manufacturing process and reduce costs.
Functional Features: Incorporate features like ribs, bosses, and holes into your design to enhance the part’s functionality and performance. Ensure that these features are designed to be easily produced with injection molding.
Simulation and Prototyping
Mold Flow Analysis: Use mold flow analysis software to simulate the injection molding process and identify potential issues such as filling problems, air traps, and weld lines. This helps in optimizing the design before manufacturing the actual mold.
Rapid Prototyping: Create prototypes using rapid prototyping techniques such as 3D printing to test the form, fit, and function of your design. This allows for early detection of design issues and iterative improvements.
Cost Considerations
Designing for injection molding also involves considering the cost implications. Here are some factors that can impact the cost:
Tooling Costs: The complexity of the mold affects tooling costs. Simple molds with fewer cavities and features are less expensive than complex molds with multiple cavities and intricate features.
Material Costs: The choice of material can influence the cost. High-performance materials may be more expensive but offer better mechanical properties and durability.
Cycle Time: Design features that optimize cooling and reduce cycle time can lower production costs and increase overall efficiency.
Quality Control and Testing
Ensuring the quality of molded parts is essential for meeting performance standards and customer expectations. Implement quality control measures such as:
Inspection: Regularly inspect parts for defects such as warping, sink marks, and surface blemishes.
Dimensional Analysis: Use precision measuring instruments to verify that parts meet dimensional specifications.
Functional Testing: Test the parts to ensure they perform as intended and meet functional requirements.
Conclusion
Designing for injection molding requires a comprehensive understanding of the process and careful consideration of various design principles. By selecting the right materials, optimizing mold design, and utilizing simulation and prototyping tools, you can achieve high-quality, cost-effective results. Incorporating these practices into your design process will enhance manufacturability, reduce production costs, and ensure the successful production of molded parts.
Note: IndiBlogHub features both user-submitted and editorial content. We do not verify third-party contributions. Read our Disclaimer and Privacy Policyfor details.