How to Track Auto Parts and Tools with Inventory Software for Garages
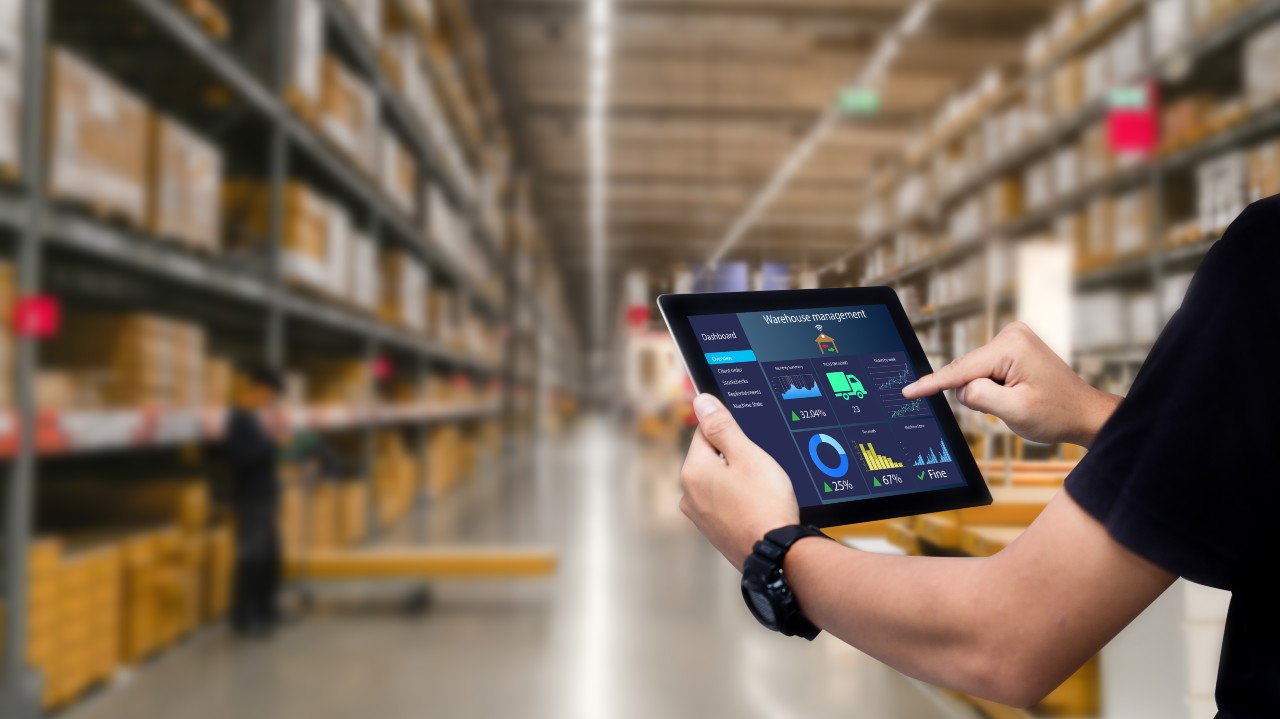
Inventory Software for Garage is more than just turning wrenches and diagnosing engine trouble. Behind the scenes, efficient inventory management plays a critical role in keeping operations smooth, minimizing downtime, and improving profitability.
Whether you're managing a small repair shop or a full-service auto center, tracking auto parts and tools accurately ensures you have what you need, when you need it. Fortunately, modern inventory software tailored for garages can simplify this task.
Why Inventory Software for Garage matters for auto repair shops, how inventory software works, and step-by-step strategies to effectively track parts and tools using these digital solutions.
Why Inventory Management Matters in Auto Garages
Imagine a mechanic trying to complete a repair job, only to find that the necessary part is out of stock—or worse, was mislabeled. This results in delays, frustrated customers, and lost revenue. Proper inventory tracking helps you:
Improve Service Efficiency: Quick access to required parts reduces vehicle turnaround time.
Reduce Overstock and Waste: Track usage trends and avoid over-ordering.
Minimize Theft or Loss: Know where your tools are and who used them last.
Forecast Demand Accurately: Data-driven insights can help with seasonal stock planning.
Increase Profit Margins: Manage supplier costs and reduce unnecessary expenses.
Traditional spreadsheets or manual systems often fail to keep pace with a busy workshop. This is where inventory management software steps in.
What is Garage Inventory Management Software?
Inventory Software for Garage is a digital tool that helps you monitor, organize, and control your stock of tools, parts, and supplies. Specialized versions for auto garages often come with additional features such as:
• Barcode scanning
• Vendor and purchase order tracking
• Maintenance scheduling for tools
• Integration with POS or work order systems
• Cloud-based access and mobile support
Some popular solutions include Shop-Ware, GaragePlug, Mitchell 1, and AutoFluent, though many garages also use customizable systems like QuickBooks or Zoho Inventory.
How to Track Auto Parts and Tools Effectively
Let’s break down the steps to successfully implement and use inventory software in your garage.
1. Audit Your Existing Inventory
Before using any software, start by auditing your current stock:
List all parts, tools, lubricants, and consumables.
Group items by category (e.g., engine parts, diagnostics tools, hand tools).
Count current quantities and record their location.
Check for expired, damaged, or obsolete items.
This baseline data is crucial for populating your software with accurate initial inventory levels.
2. Choose the Right Inventory Software
Not all software is created equal. Consider the following when selecting a system:
Ease of use: Staff should be able to learn it quickly.
Mobile access: Handy for mechanics on the shop floor.
Barcode/RFID support: Automates check-in/check-out of tools.
Parts lookup integration: Connects with suppliers for real-time pricing and ordering.
Alerts & notifications: Reorder reminders for low-stock items.
Multi-location tracking: For garages with multiple branches.
Demo a few platforms before committing. Look for user reviews specific to auto repair businesses.
3. Set Up Your Inventory Database
Once you've chosen your software, it’s time to populate your inventory list:
Enter Product Details: Include part numbers, supplier info, compatible vehicles, cost, and storage location.
Assign Categories: Helps with sorting and reporting (e.g., electrical, suspension, HVAC).
Add Barcodes or QR Codes: Print labels for each item to simplify tracking.
Establish Minimum and Maximum Levels: Trigger reorder alerts when stock falls below a certain level.
Some software can import data from Excel spreadsheets or CSV files, saving setup time.
4. Track Tools Using Check-In/Check-Out Features
Tools often go missing or get misplaced. To prevent this, track tools the same way you track parts:
Use tool tracking modules in your inventory software.
Assign tools to specific employees via check-in/check-out systems.
Add GPS tags or RFID chips for high-value tools or diagnostics equipment.
Monitor usage frequency and schedule preventive maintenance.
Some systems even allow digital signatures or photos when tools are issued and returned.
5. Automate Purchase Orders and Supplier Integration
Running out of stock is costly. Inventory Software for Garage platforms offer features to automate ordering:
• Set reorder points for frequently used parts.
• Automatically generate purchase orders (POs) based on real-time inventory.
• Integrate with suppliers for direct online ordering.
• Track incoming shipments and update inventory upon arrival.
• These automation features reduce the risk of stockouts and streamline supplier communications.
6. Monitor Inventory Reports and KPIs
Regular reporting is essential to optimize your inventory over time. Use the software to generate:
Stock movement reports – What’s being used and how fast?
Slow-moving items – Parts or tools collecting dust.
Profit margins by item – Are you pricing your parts effectively?
Supplier performance – Delivery times, cost accuracy, etc.
These insights can help you cut costs, improve efficiency, and boost your bottom line.
7. Train Your Team and Establish Workflows
Technology is only as effective as the people using it. Ensure your staff understands:
How to use the software on desktops or mobile devices.
The importance of scanning parts and tools in/out.
What to do when discrepancies arise.
Establish clear procedures for inventory receiving, restocking, and tool check-outs. Hold periodic training refreshers and audits to maintain discipline.
8. Integrate with Your Other Systems
To maximize efficiency, connect your inventory software with:
Point of Sale (POS) systems
Customer Relationship Management (CRM) software
Accounting platforms like QuickBooks or Xero
Repair order software or shop management tools
Integrated systems reduce data duplication, ensure consistency, and give a full-picture view of your operations.
Final Thoughts
Tracking auto parts and tools doesn’t have to be chaotic or time-consuming. With the right inventory software, garages can maintain accurate stock levels, improve repair speed, and eliminate unnecessary costs. From initial setup and database creation to automation and reporting, each step builds a stronger, more efficient workflow.
In the long run, investing time and resources into proper inventory management pays off with better customer satisfaction, lower expenses, and smoother daily operations. Whether you're running a two-bay shop or a large dealership service center, the right tools—both physical and digital—can make all the difference.
Note: IndiBlogHub features both user-submitted and editorial content. We do not verify third-party contributions. Read our Disclaimer and Privacy Policyfor details.