How Work Rolls Improve Steel and Metal Rolling Efficiency
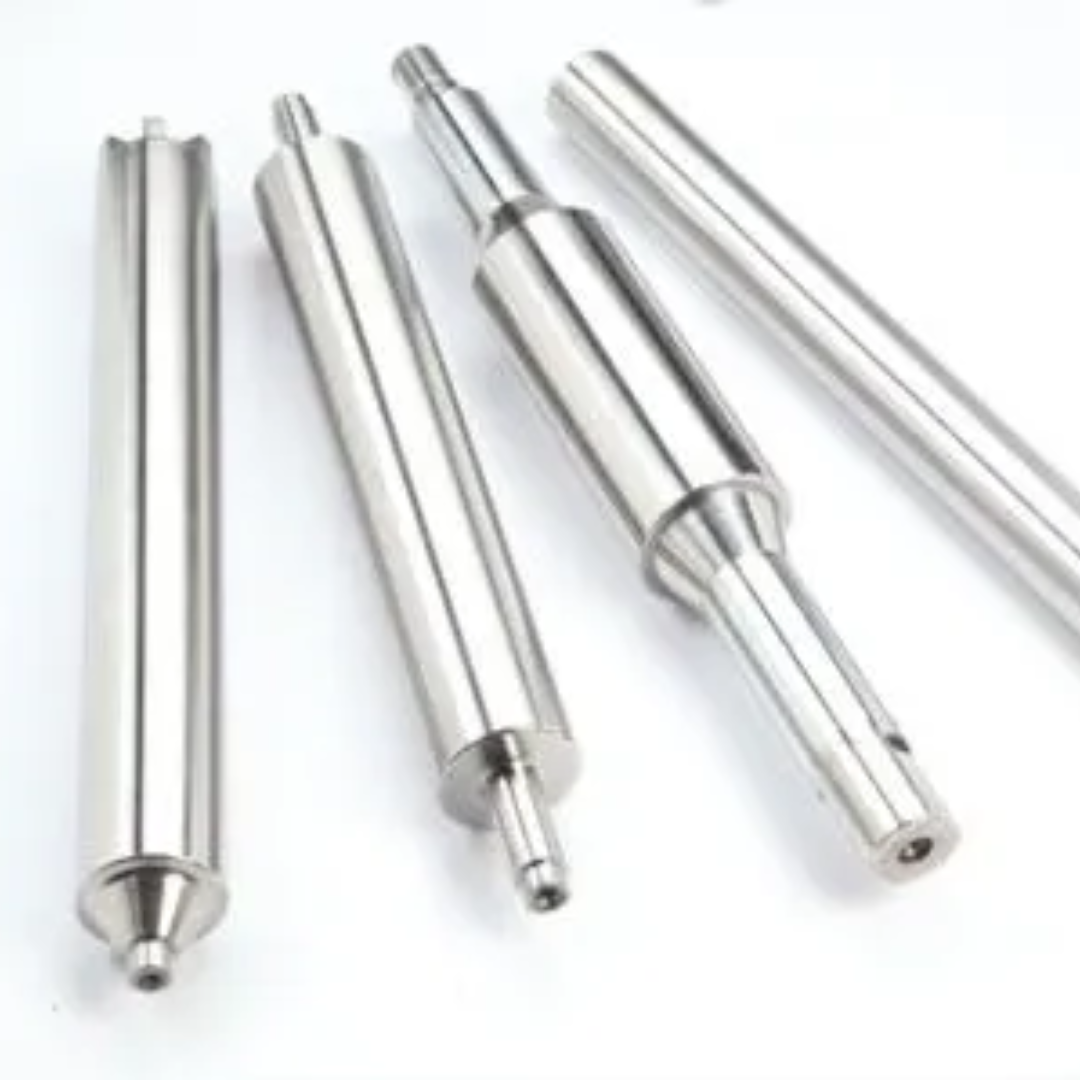
Few manufacturing processes are more crucial to industrial manufacturing than steel and metal rolling. Rolled metal products are the backbone of countless industries, from automobile components to building materials and household appliances. The center of it all is an element most commonly overlooked by the untrained eye: the work roll. This cylindrical equipment brings pressure and form to rolling, which is key to product quality, energy conservation, and total production output.
Since the world demand for premium rolled metal continues to escalate, knowing how work rolls impact efficiency can make producers competitive. In this blog, we look at how the role of work rolls improves the performance of steel and metal rolling processes.
What is a Work Roll?
A work roll is a mechanical piece of equipment used in rolling mills. It makes contact directly with the metal being rolled, exerting pressure to decrease thickness, enhance surface finish, and attain the desired shape. Work rolls are usually used in pairs, supporting backup rolls in multi-roll arrangements, particularly in high-capacity rolling.
Work rolls are fabricated from hardened steel or alloy material and must resist heavy mechanical stress, high temperature, and perpetual wear. To achieve maximum performance and long life, parameters vary depending on the rolling type (hot or cold), roll material, and surface treatment.
Improving Efficiency Through Better Rolling
Efficiency in a rolling mill means manufacturing quality goods at the highest rate with reduced waste or downtime. Work rolls help achieve this directly in the following ways:
1. Consistent Pressure Application
One of the most important functions of a work roll is to provide even pressure on the metal strip or sheet. Work rolls with precision grinding will give even pressure, ensuring consistent thickness and flatness. Inconsistent pressure can result in defects like edge waves, center buckles, or surface marks, resulting in scrap or rework.
Contemporary work rolls are made to be dimensionally accurate when loaded, reducing variability considerably and enabling higher quality levels.
2. Lower Energy Consumption
Work rolls designed and cared for properly enhance the contact surface between the roll and the metal, reducing energy loss through friction and slippage. Optimized rolls require less power to roll the material, resulting in lower energy expenditure per ton of rolled metal. At a time when industrial sustainability is becoming increasingly important, energy-efficient work rolls directly contribute to environmental and business objectives.
3. Enhanced Surface Finish and Product Quality
The work roll surface finish directly influences the ultimate finish of the metal product. Smooth, well-maintained rolls can give a clean, uniform surface in cold rolling, where appearance and texture are critical. Rolls are also intentionally textured (e.g., chrome plating or electro-discharge texturing) to affect product properties.
Investment in high-grade work rolls with superior finishes means fewer surface defects, less polishing, and less downstream processing.
4. Longer Roll Life and Less Downtime
High-grade work rolls are designed to withstand wear, spalling, and cracking even under severe operating conditions. By using advanced materials and surface coatings, manufacturers can prolong the roll's operating life and minimize the number of roll changes.
Every roll change normally causes production downtime, which can be expensive in high-volume situations. Enhancing roll life makes operations more consistent, and maintenance cycles are further apart, a significant benefit in continuous rolling lines.
5. Precision Rolling with Advanced Controls
Work rolls in modern rolling mills are frequently part of a sensor-controlled, semi-automatic, or automatic system with feed-forward loops. Such systems control roll gaps, pressures, and speeds in real time to optimize rolling conditions. Incorporating work rolls into such controls provides more accurate tolerances and improved repeatability.
High-performance work rolls are a requirement in aerospace, electronics, and automotive production, where micro-level accuracy is not negotiable.
Types of Work Rolls Depending on Application
Depending on the rolling process, various types of work rolls are employed:
- Hot Rolling Work Rolls: These rolls need higher thermal resistance and wear protection at elevated temperatures.
- Cold Rolling Work: Rolls Run at room temperature and need high hardness and a high-polish finish to satisfy surface quality requirements.
- Cluster or Multi-Roll Mill Work Rolls: They are combined with backup rolls to handle thinner gauges and minimize deflection.
The Significance of Proper Roll Maintenance
Even the finest work roll will eventually wear out if not maintained correctly. Periodic inspection, grinding, and rebalancing are essential to keeping rolls in top condition. Non-destructive testing techniques, such as ultrasonic or magnetic particle inspection, assist in identifying subsurface defects before failure.
Most facilities are moving towards predictive maintenance, where sensors monitor wear and performance patterns to plan service without disrupting production.
A Final Word: Selecting the Right Partner
The operation of your rolling mill is highly dependent on the quality and consistency of your work rolls. If you're making wide steel sheets or precision metal strips, the correct roll setup can make a quantifiable difference in speed, efficiency, and quality.
Collaborating with skilled suppliers focusing on high-performance work rolls helps keep your production line competitive in today's fast-paced manufacturing world.
Conclusion
In metal processing's fast-paced, competitive marketplace, every factor matters, and work roll is hardly insignificant. These pivotal components power rolling applications' efficiency, quality, and reliability globally. The correct workflow configuration can greatly enhance your operational capacity, from increased energy savings to better product finishes.
For businesses that need superior material handling and slitting technology, Maxwell Slitters is a name to trust. It combines innovation with functional performance and ensures that each roll and product meets the highest industrial standards.
Note: IndiBlogHub features both user-submitted and editorial content. We do not verify third-party contributions. Read our Disclaimer and Privacy Policyfor details.