Inductive Sensors: Enhancing Efficiency in Industrial Automation
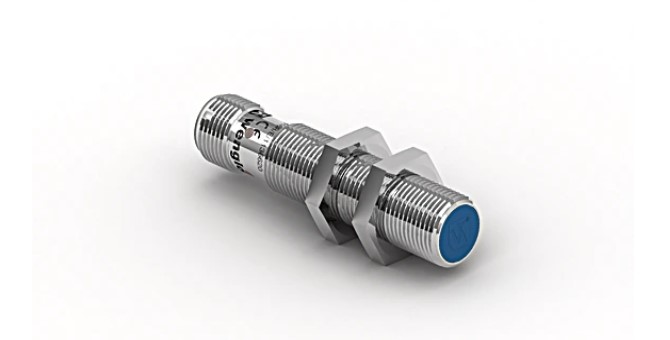
What is an Inductive Sensor
An inductive sensor can be defined as a non-contact sensor that utilizes an electromagnetic field to sense the presence of metallic substances. The internal circuitry of the sensor contains a marked coil that will generate an oscillating electromagnetic field. If a metallic object were to enter this field, eddy currents would be induced in the object and the output from the sensor would change as a result. This would indicate contact was detected.
In addition, these sensors are not affected by dust, contaminants, or even the presence of moisture in the air. For these reasons and others, a wide variety of industrial manufacturers use inductive sensors for numerous processes such as automation, manufacturing, and even systems for quality assurance.
Key Features and Advantages
These sensors make it possible to automatically monitor various processes in an industry and business area. They possess numerous benefits that enhance their use in the industry including:
- Touch free capability enables the sensor to last longer and avoids sensor degradation.
- Greater resistance when it comes to dust, moisture, vibrations alongside extreme temperatures for prolonged periods.
- Reduces the amount of time needed to respond to a problem. This also enables faster decisions to be made with regards to automation.
- Works well in the identification of ferrous and non-ferrous metals.
- Contributes to a decline in the need for a maintenance routine because of the absence of moving parts.
- Functions effectively in adverse economic conditions that are characterized by being unclean, greasy, or having a high temperature.
- For a single sensor, it can be used collectively within different systems making it more appealing.
- Always using a cost-effective solution with low maintenance needs allows for higher operational productivity.
- Withstanding high levels of electromagnetic interference (EMI) makes it possible to efficiently work around heavy machinery and electrical systems.
- Useful in dirty environments where eyes or other mechanical sensors cannot be used, and are often exposed to grease or chemicals.
The aforementioned characteristics justify the preference for the use of inductive sensors for applications that require accuracy, reliability, and prolonged service.
Common Industrial Applications
Many industrial sectors rely on inductive sensors for dependable and efficient detection solutions. Some of the more common applications include:
- Detecting the position and movement of certain metal elements on an automated production line.
- Speed monitoring of rotating machinery and conveyor systems to avoid malfunctions.
- Automatic sorting of ferrous and non-ferrous metals in sorting lines.
- Detection of metallic objects in dangerous zones for industrial machines to ensure their safety.
- Quality assurance checks for the manufacturing of machines, especially confirming assembly processes.
- During vehicle manufacturing, while assembling and welding metal components onto the vehicle.
- Detection of metal particles on packaging and production lines to ensure the quality and safety of products in the Food and beverage industry.
- Advanced Metals, Robotics Using Induction Automation, and Robotics Automation, Inc. produce sensors for the mining industry to assist in detecting heavy machinery operations in extreme conditions.
- Sensing components in induction automation and robotics make sure of the precise placement of metal parts in high-speed production lines.
Inductive sensors are integral in clear processes where industry relations are automated. They have to increase efficiency and output while minimizing downtimes.
Choosing the Right Inductive Sensor
In order to pick the appropriate inductive sensor, one has to keep in mind the application, workplace condition, and detection specifics. These particularly are important:
- It varies depending on the shape of the sensor and the material of the metal object.
- Non-ferrous metals like Aluminum and Copper have lower range while Ferrous metals like Iron and Steel target have range level.
- Working Temperature, Humidity, Dust, and Chemical Factors.
- Mounting Type, either flush or non- flush type.
- System NO and NC requirements output.
- Type of connection, including smart automation's analog, digital, and IO link.
- Electronics for better performance and reliability over heightened electromagnetic interference regions.
- Automation system responsiveness. Fast response sensors allow for efficiency to be maintained.
- Durability under mechanical stress makes them ideal for environments with frequent vibrations and shocks.
Industries in need of dependable proximity sensors can find what they are looking for as OMCH has prepared a full package of industrial sensing solutions for automation. For more information visit https://www.omchsmps.com/de/path/proximity-switch/.
Future Trends in Inductive Sensor Technology
With the growing complexity of automation, inductive sensor technology as well is evolving to fulfill new requirements. Some important factors that will dictate the evolution of the inductive sensors comprise:
- Increasing the scope of monitoring and maintenance with IoT integration of Industry 4.0.
- Increased ranges of detection through superior coil and circuit design with advanced measurement accuracy.
- Inductive sensor miniaturization for placement in small spaces in automated systems.
- Superior energy management that minimizes terms of trade and increases the equity in the industrial setting.
- Broader environmental restrictions using new materials and coatings which makes the equipment more durable under extreme conditions.
- Flexible installation and easier set up without complicated wiring through wireless sensors.
- Performance and failure prediction monitoring the status of the system boosts reliability.
- Integrating the ability of systems to adapt to errors and optimize processes using AI.
- Combining sensors with other systems like temperature sensors, inductive vibration sensors to achieve multi-systems for industrial monitoring.
- Enhanced processing techniques to minimize incorrect identifications and achieve a higher sensor precision within difficulty settings.
Subsequent to the improvement of the multi-capability feature of inductive sensors, they are made as temporary sensors along with other measuring tools including the thermometer or the vibrometer. These sensors are more comprehensive and suitable for prediction of maintenance in smart industries. They are expected to improve the capabilities and performance of inductive sensors meant for the enhanced solutions in industrial applications and smart manufacturing. Inductive sensors will remain relevant in industries involving production rates; developments in the processing of occurrences and determination of definitive processes; and reliable automation. Finally, both the direct and indirect productivity in many industries will be affected in a seamless manner through the use of those sensors.
Note: IndiBlogHub features both user-submitted and editorial content. We do not verify third-party contributions. Read our Disclaimer and Privacy Policyfor details.