Injection Molding Process: A Comprehensive Guide
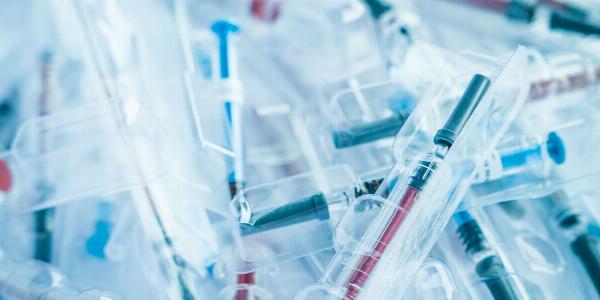
Introduction
The injection molding process stands at the forefront of modern manufacturing, revolutionizing how products are created with precision and efficiency. From everyday household items to complex automotive components, injection molding plays a crucial role in producing high-quality parts with remarkable consistency. This guide delves into the intricacies of the injection molding process, exploring its stages, applications, and benefits, providing a thorough understanding of why it's a preferred method in various industries.
Understanding Injection Molding
What is Injection Molding?
Injection molding is a manufacturing process used to produce parts by injecting molten material into a mold. It is widely employed for fabricating items from thermoplastic and thermosetting polymers. The process is efficient, capable of producing large quantities of identical items with precise specifications.
History of Injection Molding
The injection molding process dates back to the late 19th century when the first patent was issued to John Wesley Hyatt and his brother for the injection molding machine. Over the decades, advancements in technology and materials have refined the process, making it a cornerstone of modern manufacturing.
The Injection Molding Process
Step 1: Material Selection
The process begins with selecting the appropriate material. Thermoplastics, thermosets, and elastomers are common choices, each offering unique properties suitable for different applications.
Step 2: Mold Design
Designing the mold is a critical step, requiring precision and expertise. The mold consists of two halves โ the cavity (female part) and the core (male part). The design must account for shrinkage, cooling rates, and material flow to ensure the final product meets specifications.
Step 3: Melting the Material
The chosen material is fed into the injection molding machine, where it is heated until it reaches a molten state. This is typically achieved using a combination of electric heaters and friction generated by the screw rotation.
Step 4: Injection of Molten Material
The molten material is then injected into the mold cavity under high pressure. This stage requires precise control to ensure the material fills the mold completely without any voids or imperfections.
Step 5: Cooling and Solidification
Once the mold is filled, the material begins to cool and solidify. Cooling time varies depending on the material and part design, but it is crucial for the integrity and dimensional accuracy of the final product.
Step 6: Ejection of the Part
After cooling, the mold opens, and the newly formed part is ejected. Ejector pins or plates are typically used to push the part out of the mold cavity.
Step 7: Post-Processing
Post-processing may involve trimming excess material, assembling components, or applying surface finishes. This step ensures the part meets the desired aesthetic and functional standards.
Materials Used in Injection Molding
Thermoplastics
Thermoplastics are the most commonly used materials in injection molding due to their versatility and recyclability. Examples include polyethylene, polypropylene, polystyrene, and ABS (Acrylonitrile Butadiene Styrene).
Thermosets
Thermosets undergo a curing process during molding, making them hard and durable. Common thermosets include epoxy, phenolic, and melamine.
Elastomers
Elastomers, like rubber, offer flexibility and resilience, making them ideal for applications requiring elasticity and impact resistance.
Applications of Injection Molding
Automotive Industry
Injection molding is extensively used in the automotive industry to manufacture parts such as dashboards, bumpers, and interior components.
Consumer Goods
From kitchen utensils to toys, injection molding produces a wide range of consumer goods with high precision and durability.
Medical Devices
The medical field relies on injection molding for creating sterile, high-precision components like syringes, implants, and diagnostic equipment.
Electronics
Injection molding is crucial in producing housings, connectors, and other components used in electronic devices.
Advantages of Injection Molding
High Efficiency
Injection molding offers high production rates, making it ideal for mass production. Once the mold is created, parts can be produced quickly and consistently.
Precision and Consistency
The process ensures tight tolerances and consistent quality across large volumes, essential for industries requiring precision parts.
Material Versatility
Injection molding accommodates a wide range of materials, allowing manufacturers to choose the best material for their specific application.
Reduced Waste
The process generates minimal waste as excess material can often be recycled and reused in subsequent runs.
Complex Designs
Injection molding can produce complex shapes and intricate details that would be challenging or impossible with other manufacturing methods.
Challenges in Injection Molding
Initial Cost
The upfront cost for designing and creating molds can be high, especially for complex parts. However, this is offset by the long-term benefits in high-volume production.
Design Limitations
Certain designs may be challenging to mold, requiring careful consideration of part geometry and material flow to avoid defects.
Material Constraints
Not all materials are suitable for injection molding. Some materials may have processing limitations or may not achieve the desired properties.
Innovations in Injection Molding
Advanced Materials
Ongoing research into new materials enhances the capabilities of injection molding, allowing for parts with improved performance and sustainability.
Automation
Automation in injection molding improves efficiency, reduces labor costs, and enhances quality control.
3D Printing Integration
Integrating 3D printing with injection molding opens new possibilities for rapid prototyping and custom manufacturing.
Quality Control in Injection Molding
Process Monitoring
Continuous monitoring of the injection molding process ensures consistency and identifies potential issues early.
Inspection Techniques
Various inspection techniques, such as X-ray and ultrasonic testing, are used to verify the quality and integrity of molded parts.
Defect Prevention
Implementing strategies like mold flow analysis and design optimization helps prevent common defects like warping, sink marks, and voids.
Environmental Considerations
Recycling and Sustainability
Injection molding supports recycling efforts, with many thermoplastics being recyclable. Efforts are also made to use eco-friendly materials and reduce waste.
Energy Efficiency
Advancements in injection molding machinery focus on energy efficiency, reducing the environmental impact of the manufacturing process.
Future of Injection Molding
Smart Manufacturing
The integration of IoT and smart technologies in injection molding leads to more efficient, adaptive, and intelligent manufacturing processes.
Sustainable Practices
The industry continues to explore sustainable practices, including the use of biodegradable materials and improved recycling methods.
Global Trends
Global trends in injection molding indicate a growing demand for high-precision, lightweight, and durable components across various sectors.
FAQs
How does injection molding differ from other molding processes?
Injection molding involves injecting molten material into a mold, whereas processes like blow molding and compression molding use different techniques to form parts.
What are the typical lead times for injection molding projects?
Lead times can vary based on the complexity of the part and the mold design, but typically range from a few weeks to several months.
Can injection molding be used for low-volume production?
While injection molding is ideal for high-volume production, it can be used for low-volume production with the appropriate cost considerations.
What factors influence the cost of injection molding?
Factors include material selection, mold design complexity, production volume, and post-processing requirements.
How do I choose the right material for injection molding?
Material selection depends on the application requirements, including mechanical properties, temperature resistance, and cost.
What is the lifespan of an injection mold?
The lifespan of an injection mold depends on factors like material, design, and maintenance but typically ranges from hundreds of thousands to millions of cycles.
Conclusion
The injection molding process is a cornerstone of modern manufacturing, offering unparalleled efficiency, precision, and versatility. By understanding its intricacies and advancements, businesses can leverage this technology to produce high-quality parts that meet the demands of various industries. As innovation continues to drive the field forward, the future of injection molding promises even greater capabilities and sustainable practices.
Note: IndiBlogHub features both user-submitted and editorial content. We do not verify third-party contributions. Read our Disclaimer and Privacy Policyfor details.