Innovations in Electron Beam Melting for Complex Geometries
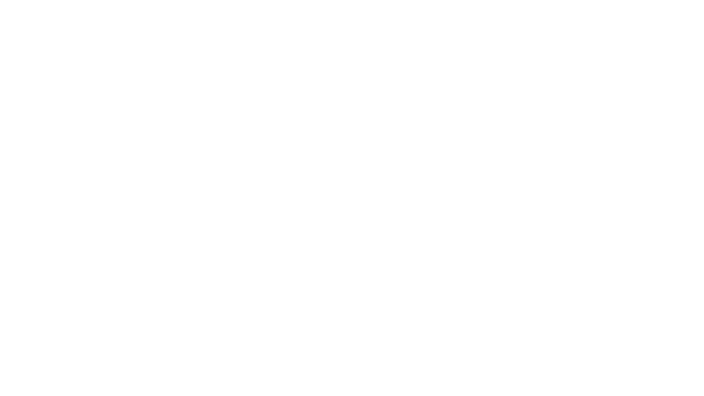
https://ebeammachine.com/what-is-electron-beam-melting-advantages-and-applications-in-3d-printing/
In the world of advanced manufacturing, 3D printing has revolutionized the way we create and design products. Among the many methods, Electron Beam Melting (EBM) has emerged as a powerful tool, especially for industries requiring intricate designs and complex geometries. Originally developed for aerospace and medical applications, EBM has expanded into a broader range of sectors, including automotive, defense, and even energy production. This innovation continues to evolve, pushing the boundaries of what’s possible in additive manufacturing.
In this blog, we will explore the latest innovations in Electron Beam Melting and how they are transforming the production of complex geometries.
What is Electron Beam Melting?
Electron Beam Melting is an additive manufacturing technology that uses a high-energy electron beam to melt metal powder, layer by layer, to form a solid part. Unlike traditional methods of subtractive manufacturing, such as milling or casting, EBM creates objects directly from 3D CAD models. It is particularly effective for working with high-performance materials like titanium, cobalt chrome, and various alloys, which are often used in industries such as aerospace and healthcare.
EBM operates in a vacuum environment to prevent oxidation and contamination of the metal powder. The electron beam precisely melts the material, allowing for the creation of parts with high precision and minimal material waste. The ability to produce intricate structures with fine details has made EBM a go-to solution for complex geometries that are difficult or impossible to achieve with conventional manufacturing methods.
Advances in Electron Beam Melting for Complex Geometries
1. Improved Precision and Resolution
One of the most significant innovations in Electron Beam Melting is the continued improvement in precision and resolution. EBM machines are now capable of achieving finer layer resolutions, allowing for the production of more intricate geometries. With higher resolution, manufacturers can produce parts with better surface finishes and more intricate internal structures, which is particularly valuable for sectors such as medical implants, where precision is critical for the part's functionality and safety.
Recent advancements in EBM technology have led to more accurate control over the energy input from the electron beam. This fine control allows for precise melting of the metal powder, reducing issues like distortion and warping that can arise with complex geometries.
2. Multi-Beam EBM Systems
Traditionally, EBM machines utilize a single electron beam to melt metal powder. However, a new development in the field is the creation of multi-beam EBM systems. These systems use multiple electron beams working in parallel, effectively speeding up the printing process without sacrificing quality.
By using multiple beams, it becomes possible to fabricate larger parts or produce complex geometries at a faster rate. This innovation not only improves throughput but also enhances the ability to create parts with a higher degree of customization, a crucial feature for industries where every design detail matters, such as aerospace, where every millimeter counts in reducing weight and improving performance.
3. Advanced Material Development
EBM's success has been heavily tied to the development of specialized materials that can withstand the intense heat and precision required for additive manufacturing. New alloys and powder blends are being designed specifically for use with EBM technology, offering improved strength, fatigue resistance, and corrosion resistance—traits that are highly valued in demanding industries like aerospace and medical implant manufacturing.
These materials are engineered to perform under extreme conditions, such as high-temperature environments or exposure to harsh chemicals, making them ideal for creating complex geometries that must maintain structural integrity over time. The customization of materials also allows for the creation of parts with tailored mechanical properties, improving the overall performance of the finished product.
4. In-Situ Monitoring and Adaptive Control
One of the emerging trends in Electron Beam Melting is the integration of real-time monitoring and adaptive control systems. These systems enable manufacturers to closely monitor the melting process during production, ensuring that any issues, such as material inconsistencies or temperature fluctuations, are detected and addressed instantly.
In-situ monitoring allows for dynamic adjustments to the process parameters, optimizing the quality of the printed part without requiring manual intervention. This not only improves the consistency of the finished product but also reduces the likelihood of defects, making it easier to produce highly complex geometries with fewer risks of failure.
5. Integration with Hybrid Manufacturing Systems
Another key innovation is the integration of EBM with hybrid manufacturing systems. Hybrid systems combine the strengths of additive and subtractive manufacturing, allowing for the production of complex geometries with exceptional surface finishes and structural integrity.
With hybrid systems, an EBM machine can build the bulk of the part, and then a subtractive process, such as milling, can be used to refine the surface, add additional details, or correct any imperfections. This combination is especially useful for industries that require both the freedom to design complex geometries and the need for high-quality, precise finishes, such as the aerospace and automotive industries.
6. Reduced Post-Processing Needs
Post-processing has traditionally been one of the more time-consuming aspects of additive manufacturing. However, advancements in EBM technology have led to a significant reduction in the need for post-processing, particularly for complex geometries.
With better control over the layer bonding and surface quality, parts produced using EBM can require less finishing work, such as sanding, polishing, or heat treatment. This innovation leads to faster production times and a more streamlined manufacturing process, which is essential in industries where time-to-market is critical.
Conclusion
As industries continue to demand more complex, high-performance parts, innovations in Electron Beam Melting are making it possible to meet these challenges. With improved precision, faster production speeds, and enhanced material options, EBM is paving the way for a new era of manufacturing. The ability to create complex geometries—ranging from intricate internal structures to parts with customized mechanical properties—gives manufacturers unparalleled design freedom.
As technology continues to evolve, it is clear that electron beam melting will remain at the forefront of additive manufacturing, providing solutions for industries where innovation is not just a competitive advantage but a necessity for survival. The future of manufacturing looks bright, and EBM will undoubtedly play a central role in shaping it
Note: IndiBlogHub features both user-submitted and editorial content. We do not verify third-party contributions. Read our Disclaimer and Privacy Policyfor details.