Integrating 3D Printing with CAD: A Seamless Workflow
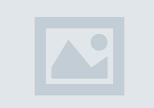
In recent years, the convergence of 3D printing and Computer-Aided Design (CAD) has fundamentally transformed the way products are developed, prototyped, and manufactured. From rapid prototyping in product design to personalized healthcare solutions and aerospace-grade components, the integration of 3D printing with CAD software has enabled engineers, designers, and manufacturers to streamline workflows, reduce time-to-market, and innovate faster than ever before.
As noted in TechPapersWorld’s article on essential CAD technologies, integrating 3D printing directly into the CAD environment is one of the key trends shaping the future of design and production. This blog explores how the synergy between CAD and 3D printing creates a seamless workflow—from design to fabrication—and what it means for industries across the board.
The Evolution of CAD and 3D Printing
CAD has long served as the digital backbone for product development, enabling the creation of precise 2D drawings and 3D models. Meanwhile, 3D printing, also known as additive manufacturing, has evolved from a prototyping novelty to a powerful production technology capable of fabricating complex parts directly from digital models.
The traditional workflow often involved exporting a CAD model into a separate slicer software to prepare it for 3D printing. However, this disjointed process introduced compatibility issues, file conversion errors (e.g., STL limitations), and reduced efficiency. Today, the integration of CAD and 3D printing within unified platforms or through plug-ins and cloud-based tools allows for:
Direct slicing and printing from CAD software
Real-time printability checks
Seamless material and printer selection
Enhanced iteration and prototyping cycles
This connected ecosystem is unlocking a new era of rapid, accurate, and flexible design-to-print workflows.
Benefits of Integrating CAD with 3D Printing
1. Faster Design Iteration Cycles
One of the standout advantages of combining CAD and 3D printing is the acceleration of design iteration. Changes made in the CAD model can be printed and tested almost immediately, enabling engineers to identify and correct design flaws within hours rather than days or weeks.
This is particularly valuable in industries like consumer electronics and automotive, where speed and agility are critical to competitive advantage.
2. Reduced Risk of Errors
When CAD and 3D printing are disconnected, exporting files (e.g., to STL or OBJ formats) can introduce rounding errors, tessellation issues, or loss of metadata. These issues can lead to misprints or inaccurate representations of the original design.
By keeping the workflow unified, integrated systems retain important data such as units, tolerances, material properties, and metadata, ensuring that what gets printed is exactly what was intended in the digital design.
3. Enhanced Collaboration and Workflow Integration
Many cloud-based CAD platforms like Autodesk Fusion 360, PTC Creo, and Onshape now include integrated 3D printing toolsets. These allow teams to collaborate in real-time, share models across departments, and prepare them for printing without needing to switch software or deal with compatibility issues.
This centralization of tools enhances communication between designers, engineers, and production teams—enabling a smoother transition from concept to physical part.
4. Design for Additive Manufacturing (DfAM)
With integrated 3D printing, CAD systems can now include tools that assist in designing specifically for additive manufacturing. These include:
Topology optimization to reduce material use
Lattice structures for lightweight components
Automated support generation
Orientation and slicing optimization
This enables engineers to fully leverage the design freedoms of 3D printing, producing geometries that would be impossible or too expensive with traditional manufacturing methods.
5. Cost and Time Efficiency
By eliminating the need for third-party tools and minimizing file conversions, companies can reduce both software costs and the time engineers spend managing multiple tools. It also cuts down on physical prototyping costs by enabling more effective virtual validation and simulation before printing.
Real-World Applications
Aerospace
Aerospace companies are using CAD-integrated 3D printing to produce lightweight components with optimized internal structures. For example, Airbus and GE have employed this approach to create parts that are not only lighter and stronger but also easier to certify due to accurate digital traceability from CAD to final product.
Healthcare
In medical device development, integrating 3D printing with CAD has enabled the production of patient-specific implants and surgical guides. Designers can import scan data directly into CAD software, model around it, and print personalized solutions with minimal turnaround.
Consumer Products
Companies like Nike and Adidas are using this integration to iterate rapidly on wearable product designs. The ability to test fit, function, and aesthetics through printed prototypes directly from CAD speeds up the innovation process significantly.
Tools and Platforms Making Integration Seamless
Autodesk Fusion 360: Offers a fully integrated CAD/CAM/CAE environment with built-in additive manufacturing workflows, simulation, and slicing tools.
PTC Creo: Provides robust support for additive manufacturing with lattice generation, tray management, and support structure creation directly within the CAD tool.
SolidWorks with 3DEXPERIENCE: Integrates with additive manufacturing modules and cloud-based collaboration tools for enterprise-level design-to-print workflows.
Onshape: A cloud-native CAD system that integrates easily with various 3D printing services and provides real-time collaboration features.
Challenges and Considerations
Despite its advantages, integrating 3D printing with CAD isn't without challenges:
Hardware Compatibility: Not all CAD-integrated 3D printing platforms support every printer or material, requiring customization or third-party drivers.
Learning Curve: Engineers and designers accustomed to traditional CAD workflows may need training in DfAM and slicing strategies to fully benefit.
Simulation and Validation: While integration helps speed up iteration, simulating real-world stresses and material behaviors still requires robust analysis tools.
Security: Moving CAD and print workflows to the cloud introduces potential security risks. Companies must ensure proper access controls and data protection strategies are in place.
(Explore more on secure CAD workflows in TechPapersWorld’s article on 5 key CAD technologies.)
Note: IndiBlogHub features both user-submitted and editorial content. We do not verify third-party contributions. Read our Disclaimer and Privacy Policyfor details.