IoT in Manufacturing: Use Cases, Benefits, and Challenges
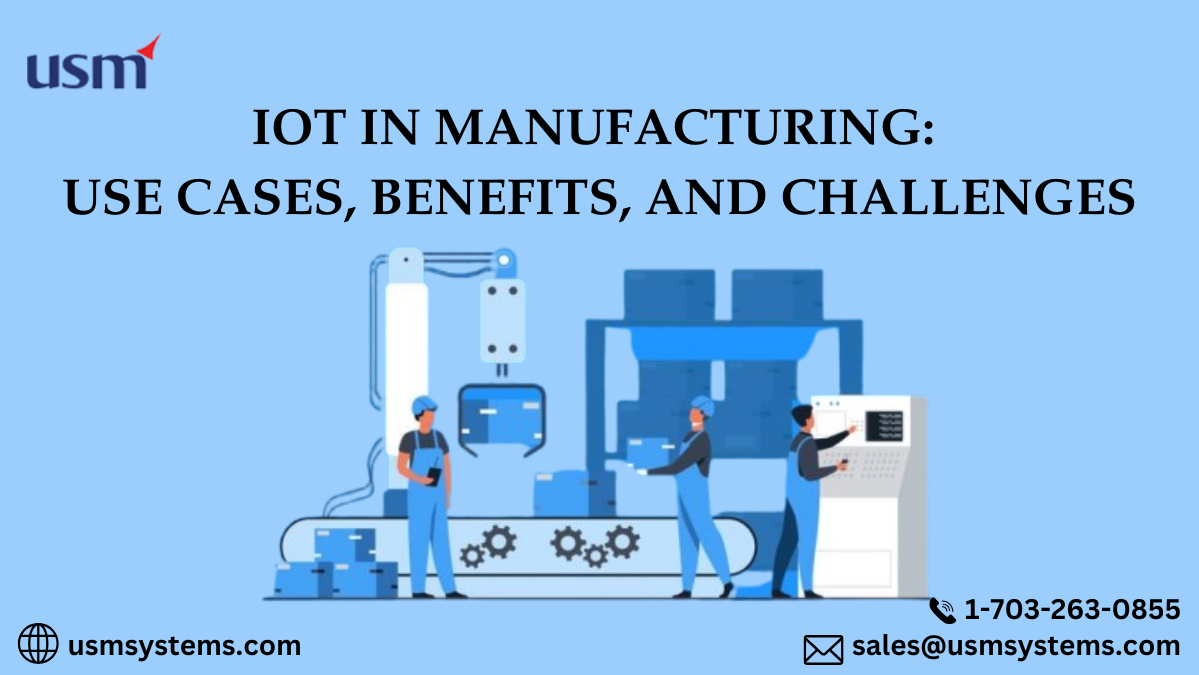
The Internet of Things (IoT) is revolutionizing the manufacturing industry by connecting machines, processes, and people in ways that enhance efficiency, productivity, and decision-making. IoT in manufacturing enables real-time data collection, predictive maintenance, and automated processes, leading to smarter factories and a competitive edge in the global market. This blog explores the various use cases, benefits, and challenges of IoT in manufacturing.
IoT Use Cases in Manufacturing
1. Predictive Maintenance
Predictive maintenance is one of the most valuable applications of IoT in manufacturing. IoT sensors collect real-time data from machinery, monitoring parameters such as temperature, vibration, and pressure. Using artificial intelligence (AI) and machine learning (ML), manufacturers can predict equipment failures before they occur, minimizing downtime and reducing maintenance costs.
2. Smart Asset Tracking and Management
IoT-powered asset tracking solutions use RFID tags and GPS sensors to monitor the location and condition of raw materials, tools, and finished products. Manufacturers can use this data to improve inventory management, reduce losses, and ensure timely deliveries.
3. Supply Chain Optimization
IoT devices help streamline supply chains by providing end-to-end visibility. Connected sensors track shipments in real time, providing accurate delivery estimates and detecting potential disruptions. Manufacturers can adjust production schedules dynamically based on supply chain conditions.
4. Remote Monitoring and Control
IoT allows manufacturers to monitor and control production processes remotely. Supervisors can access real-time data via dashboards and mobile applications, enabling them to make quick decisions even when off-site. This capability is particularly useful for global manufacturing operations.
5. Energy Management and Efficiency
IoT devices can track energy consumption across different manufacturing units and identify areas of wastage. Smart meters and connected devices optimize energy use, leading to cost savings and sustainable operations.
6. Quality Control and Assurance
IoT sensors detect defects in products during manufacturing, ensuring high-quality standards. Vision-based inspection systems combined with AI can analyze real-time data to identify deviations from quality benchmarks, reducing waste and rework costs.
7. Worker Safety and Compliance
Wearable IoT devices such as smart helmets, vests, and wristbands monitor worker health and safety conditions. These devices can detect hazardous gases, extreme temperatures, or fatigue levels and alert workers and supervisors to potential dangers.
Benefits of IoT in Manufacturing
1. Increased Operational Efficiency
IoT-driven automation reduces manual interventions, enhancing production speed and accuracy. Real-time monitoring and predictive analytics ensure that machines operate at peak efficiency.
2. Cost Reduction
By predicting maintenance needs and reducing unexpected downtime, IoT significantly cuts operational costs. Optimized resource utilization and energy efficiency further contribute to cost savings.
3. Enhanced Decision-Making
With real-time data analytics, manufacturers gain deeper insights into production processes, allowing for informed decision-making. AI-powered analytics help detect inefficiencies and suggest improvements.
4. Improved Product Quality
IoT-powered quality control mechanisms identify defects early in the production cycle, reducing scrap rates and ensuring consistent product quality. This enhances customer satisfaction and brand reputation.
5. Greater Supply Chain Visibility
Real-time tracking of materials and finished goods ensures smoother logistics operations. IoT helps manufacturers respond swiftly to supply chain disruptions and maintain steady production flows.
6. Sustainability and Environmental Impact Reduction
Smart energy management and waste reduction contribute to eco-friendly manufacturing practices. IoT-driven sustainability initiatives help businesses comply with environmental regulations and reduce their carbon footprint.
7. Better Worker Safety
Wearable IoT devices and smart monitoring systems create safer work environments by identifying potential hazards and preventing accidents.
Recommended to Read: IOT mobile application development cost.
Challenges of IoT in Manufacturing
1. High Implementation Costs
The initial investment in IoT infrastructure, including sensors, cloud platforms, and integration with existing systems, can be high. Small and medium-sized enterprises (SMEs) may find it challenging to justify the costs.
2. Data Security and Privacy Risks
IoT devices generate vast amounts of data, making them attractive targets for cyberattacks. Ensuring robust cybersecurity measures, including encryption and access controls, is crucial to protect sensitive manufacturing data.
3. Integration with Legacy Systems
Many manufacturing facilities still use legacy equipment that lacks IoT compatibility. Upgrading or integrating IoT solutions with these systems can be complex and costly.
4. Data Overload and Management
With multiple IoT devices generating massive data streams, manufacturers face challenges in storing, processing, and extracting meaningful insights from this data. Investing in advanced analytics and cloud computing solutions is necessary.
5. Skilled Workforce Requirement
Implementing and maintaining IoT solutions requires specialized expertise in data analytics, cybersecurity, and system integration. Manufacturers may need to invest in workforce training or hire skilled professionals.
6. Reliability and Downtime Risks
IoT solutions depend on stable internet connectivity and power supply. Any disruption in connectivity can lead to data loss or production downtime, affecting operational efficiency.
Conclusion
IoT in manufacturing is transforming the industry by enabling smarter, data-driven decision-making and optimizing production processes. While the benefits of IoT, such as increased efficiency, cost reduction, and enhanced safety, are substantial, challenges like high implementation costs and cybersecurity risks must be addressed. Manufacturers that successfully integrate IoT into their operations will gain a competitive edge, improve productivity, and drive innovation in the era of Industry 4.0.
As technology evolves, IoT adoption in manufacturing will become more widespread, paving the way for a more connected, intelligent, and efficient industrial landscape.
Hire the best IoT app developers and get stunning inventory tracking apps @ affordable budget!
Note: IndiBlogHub features both user-submitted and editorial content. We do not verify third-party contributions. Read our Disclaimer and Privacy Policyfor details.