Latest Trends and Technological Advancements in Automated Guided Vehicles
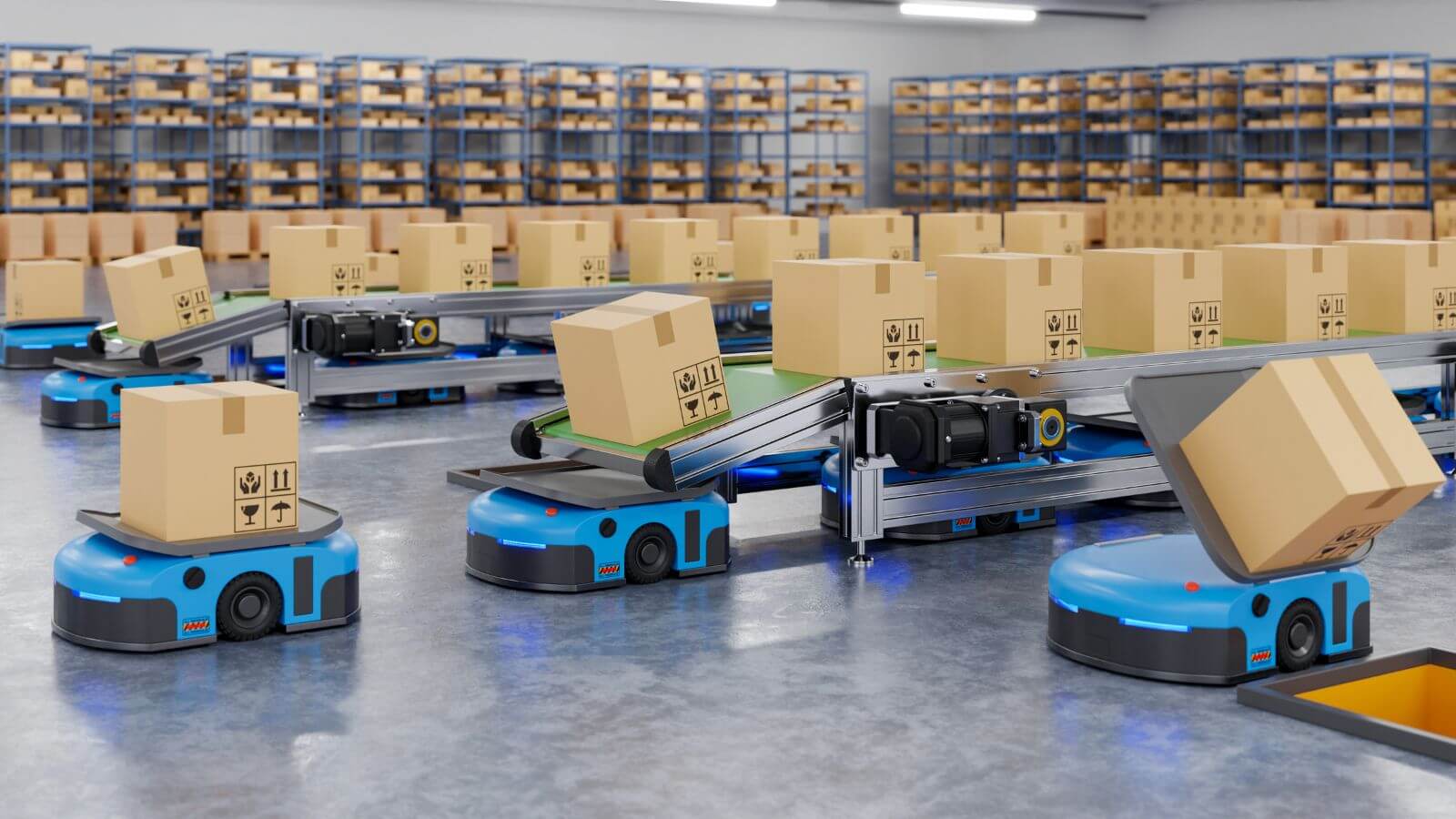
Introduction:
Automated Guided Vehicles (AGVs) are transforming industries by providing efficient, cost-effective, and scalable solutions for material handling and transportation. From manufacturing plants to warehouses and logistics centers, AGVs are streamlining operations and reshaping the future of automation. These autonomous vehicles, equipped with advanced technology, are capable of moving goods with precision, safety, and minimal human intervention. As the industry evolves, so too do the technologies that drive AGVs. In this article, we’ll explore the latest trends and technological advancements in AGVs, focusing on their impact on industries and the role of advanced sensors and LiDAR in enhancing AGV safety and precision.
The Rise of Automated Guided Vehicles
Automated Guided Vehicles have gained significant traction across multiple sectors due to their ability to improve productivity, reduce labor costs, and optimize workflows. Originally developed for material handling in industrial environments, AGVs now serve a broad range of applications, including automated material transport, order picking, inventory management, and even delivery services.
As AGVs continue to grow in popularity, their integration with other cutting-edge technologies such as Artificial Intelligence (AI), the Internet of Things (IoT), and advanced sensors is allowing them to become more intelligent, versatile, and adaptive. These advancements are contributing to a rapid transformation in industries ranging from logistics and e-commerce to manufacturing and healthcare.
Download FREE Sample of Artificial Intelligence Market
Key Trends in AGV Technology
The adoption of AGVs is driven by several key trends that are enhancing their capabilities and making them more accessible to businesses of all sizes. Below, we’ll look at some of the most prominent trends shaping the AGV market.
1. Integration with AI and Machine Learning
AI and Machine Learning (ML) are increasingly being integrated into AGVs to make them smarter and more autonomous. By leveraging AI, AGVs can adapt to changing environments, optimize their routes in real time, and make decisions based on data inputs. Machine learning algorithms enable AGVs to learn from previous tasks, improve their performance, and avoid obstacles more effectively.
These AI-driven advancements allow AGVs to navigate complex environments with minimal human oversight. For instance, AGVs can analyze and adjust their path in response to traffic, obstacles, or changes in the environment, ensuring efficient and safe operations. Additionally, AI algorithms help AGVs predict maintenance needs, reducing downtime and increasing reliability.
2. Increased Use of Cloud Computing and IoT
The Internet of Things (IoT) and cloud computing are becoming essential components of AGV systems. Through IoT connectivity, AGVs can communicate with other devices, sensors, and systems to gather and share information. This connectivity allows for better fleet management, improved coordination between AGVs, and real-time monitoring of vehicle performance.
Download FREE Sample of Internet of Things Market
Cloud computing further enhances the capabilities of AGVs by enabling centralized data storage, analysis, and control. Businesses can access detailed analytics and insights about AGV performance, allowing for better decision-making, predictive maintenance, and fleet optimization. With cloud-connected AGVs, companies can ensure that their fleets are operating at peak efficiency, reducing costs and maximizing throughput.
3. Collaborative AGVs (CAGVs)
Collaborative AGVs, or CAGVs, represent a significant shift in AGV technology. These vehicles are designed to work alongside human workers in shared environments, rather than working in isolation. This trend is particularly prominent in warehouses, where CAGVs assist in tasks such as material transport and inventory management while interacting with workers in a safe and efficient manner.
Collaborative AGVs are equipped with advanced sensors and safety features that allow them to navigate environments with high foot traffic and potential obstacles. The ability to collaborate with humans makes these AGVs ideal for environments where flexible and adaptive workflows are essential.
The Role of Advanced Sensors and LiDAR in AGV Safety and Precision
One of the most crucial aspects of AGV technology is ensuring that these vehicles operate safely and efficiently in complex and dynamic environments. The use of advanced sensors and Light Detection and Ranging (LiDAR) technology has become integral to enhancing AGV safety, precision, and overall performance.
Advanced Sensors in AGVs
AGVs rely on a wide array of sensors to detect their surroundings and make real-time decisions based on the data they collect. These sensors include ultrasonic sensors, cameras, infrared sensors, and proximity sensors, all of which provide valuable data about the environment, obstacles, and other moving objects.
Ultrasonic Sensors: These sensors use sound waves to detect obstacles in the vehicle’s path. They are commonly used for short-range detection, allowing AGVs to avoid collisions with nearby objects or walls.
Cameras and Vision Systems: AGVs equipped with cameras can capture high-resolution images of their surroundings. This data is then processed using computer vision algorithms to identify and track objects, enabling AGVs to recognize obstacles, lanes, and other critical features within their environment.
Infrared Sensors: These sensors detect heat signatures, allowing AGVs to detect human presence or other vehicles, even in low-light conditions. Infrared sensors are vital for ensuring safe operation in environments with varying lighting.
Proximity Sensors: Proximity sensors detect the presence of nearby objects by measuring changes in the electromagnetic field. These sensors are essential for AGVs to navigate tight spaces and avoid collisions with stationary or moving objects.
LiDAR Technology in AGVs
LiDAR technology, which uses laser beams to map and measure the distance to objects, is playing an increasingly important role in AGV safety and navigation. LiDAR provides AGVs with high-precision, 360-degree scanning capabilities, allowing them to build detailed maps of their environment.
LiDAR systems create a 3D representation of the surroundings by emitting laser beams and measuring the time it takes for the beams to reflect back to the sensor. This data is then processed to create accurate maps of the vehicle's environment, including the location of obstacles, walls, and other important features.
The use of LiDAR in AGVs offers several advantages:
Enhanced Navigation: LiDAR allows AGVs to navigate complex and dynamic environments with precision, making it particularly useful in warehouses or production facilities with tight spaces and moving objects.
Improved Obstacle Detection: LiDAR provides AGVs with the ability to detect obstacles with greater accuracy, even at greater distances. This is crucial for preventing collisions and ensuring safe operation, particularly in high-traffic areas.
Autonomous Operation: LiDAR enables AGVs to operate autonomously, without the need for external infrastructure such as magnetic strips or cameras. This allows for greater flexibility and adaptability in different environments.
Real-Time Mapping: LiDAR systems allow AGVs to continuously scan and update their maps in real time. This dynamic mapping capability ensures that the AGV can adjust its route and avoid obstacles as they arise.
The Synergy of Sensors and LiDAR
While both sensors and LiDAR are powerful on their own, their combined use results in even greater levels of safety and precision for AGVs. Advanced sensor systems provide AGVs with real-time data on their immediate surroundings, while LiDAR offers long-range, detailed scanning of the entire environment.
Together, these technologies ensure that AGVs can navigate safely, avoid obstacles, and operate efficiently in dynamic environments. The synergy between sensors and LiDAR also supports the development of more intelligent and adaptable AGVs, capable of performing a wide variety of tasks with minimal human oversight.
The Future of AGV Technology
As AGV technology continues to advance, we can expect even more innovative developments that will enhance their capabilities and make them an even more integral part of industrial operations. Some of the most exciting prospects for the future of AGVs include:
Increased Autonomous Capabilities: With further advancements in AI, machine learning, and sensor technology, AGVs will become even more autonomous, reducing the need for human intervention and allowing for fully automated workflows.
Smarter Fleet Management: The integration of IoT and cloud computing will allow for smarter fleet management systems that can optimize routes, monitor performance, and predict maintenance needs in real time.
Greater Energy Efficiency: The development of more energy-efficient AGVs, powered by advanced battery technologies or even solar energy, will help reduce operational costs and make AGVs more sustainable.
Enhanced Human-Robot Collaboration: As collaborative AGVs become more widespread, we can expect to see even greater levels of interaction between AGVs and human workers, enhancing safety and productivity in shared workspaces.
Conclusion
Automated Guided Vehicles are revolutionizing the way industries approach material handling, logistics, and production. With advancements in AI, IoT, and sensor technologies, AGVs are becoming smarter, safer, and more versatile. The use of advanced sensors and LiDAR is particularly crucial in enhancing AGV safety and precision, ensuring that these vehicles can navigate complex environments with minimal risk of collision or failure.
As AGV technology continues to evolve, businesses can expect to see even more sophisticated solutions that increase productivity, reduce costs, and contribute to the growth of fully automated environments. With their growing presence across industries, AGVs are poised to play a critical role in the future of automation and material handling.
Read the complete blog
Note: IndiBlogHub features both user-submitted and editorial content. We do not verify third-party contributions. Read our Disclaimer and Privacy Policyfor details.