Melt Flow Index Tester Manual
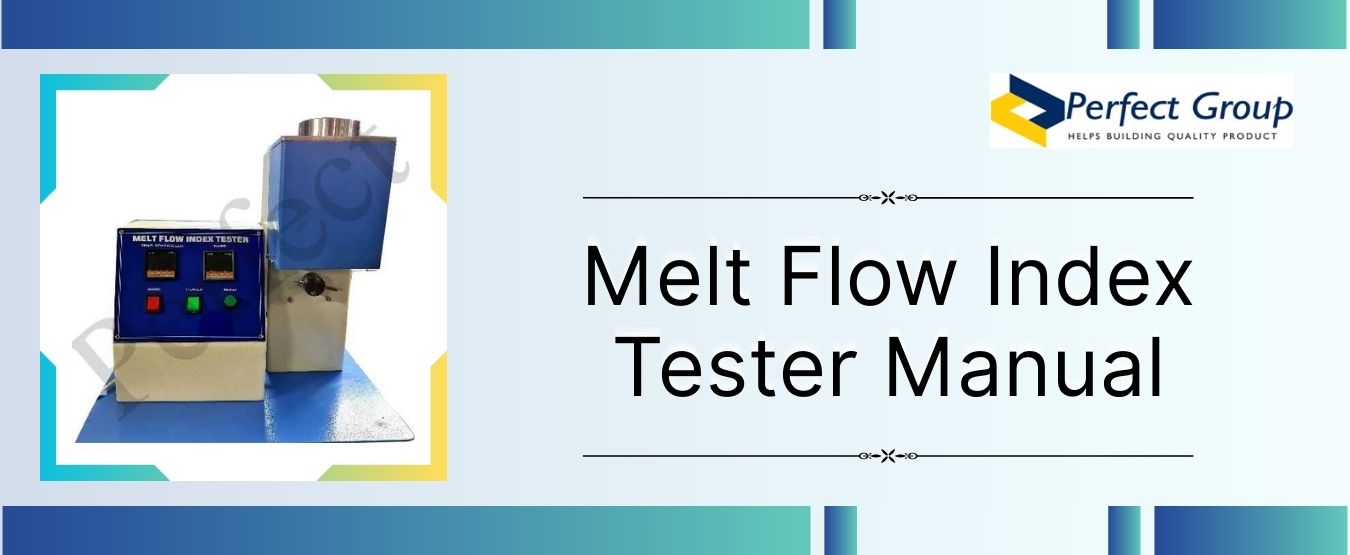
Introduction
An important instrument for finding out the flow properties of thermoplastic polymers is the Melt Flow Index Tester. It is a popular tool to analyze the consistency, thickness and overall performance of materials in industries like material research, quality control and plastics manufacture. Accurate and trustworthy results require an excellent knowledge of how it works and has to be maintained. This detailed guide helps users improve performance while maintaining quality and security by describing the instrument's functioning, performance and solving issues.
Understanding the Melt Flow Index Tester
Molten plastic flows through a specified capillary die under controlled conditions to find the melt flow rate (MFR) of polymer materials using the Melt Flow Index Tester. The test conforms to set standards that define the requirements for obtaining accurate readings, such as ASTM D1238 and ISO 1133. Because of these standards, testing results are dependable for quality control because they are repeatable and similar between multiple industries.
Components of the Tester
Each of the important elements of a Melt Flow Index Tester plays an important role in the testing procedure:
Heated Barrel โ Keeps the polymer sample melted at a controlled temperature.
Piston and Dead Weights โ The molten polymer flows through the capillary die by applying an adjustable load.
Capillary Die โ A tool with a fixed size that controls the flow rate of material.
Timer โ Controls the test time to guarantee stability.
Collection Tray โ Collects extrusion material for more research.
Digital Display/Control Panel โ Users can set situations including temperature, load and time.
Preparation for Testing
A Melt Flow Index Tester requires proper setup to produce accurate test results. Follow these instructions:
Calibrate the Machine โ Check adjustment to confirm that all of the parts are working properly.
Preheat the Barrel โ Set the correct temperature for the material type and let the barrel reach the desired level.
Prepare the Sample โ Cut a certain number of polymer grains or flakes for testing.
Load the Material โ Insert the polymer sample into the barrel and compress it with the plunger.
Apply the Weight โ Choose the suitable load based on the material's qualities and testing needs.
Conducting the Melt Flow Index Test
Start the Heating Process โ Ensure that the polymer achieves the required temperature.
Initiate the Extrusion โ Release the piston to put pressure on the molten polymer.
Measure the Flow Rate โ Use a timer to record how long it takes to melt a given amount of material.
Collect and Weigh the Sample โ The MFR is calculated by cutting the injected polymer at specified times and measuring it.
Record the Results โ Calculate the MFR using the formula:
MFR (g/10 min) = (Mass of extrudate in grams) / (Time in minutes)
Factors Affecting Test Accuracy
Many factors affect the accuracy of a Melt Flow Index Tester, including:
Temperature Stability โ Changes in barrel temperature can have an impact on test findings.
Consistent Load Application โ Adjustments in applied weight have an impact on flow rate measurements.
Material Moisture Content โ Polymers with a high moisture content can generate unequal outcomes.
Die and Barrel Cleanliness โ Previous test leftovers can cause values to change.
Maintenance and Cleaning
The Melt Flow Index Tester should be maintained and cleaned on a regular basis to guarantee its best performance.
Routine Cleaning โ After each test make sure to clean the barrel and die of any remaining polymer waste.
Component Inspection โ Check the capillary die and piston on a regular basis for signs of damage.
Temperature Calibration โ Frequently check the heating system's accuracy.
Lubrication โ Apply lubricant to moving parts if required.
Firmware Updates โ Check to see if the digital control system needs to be updated.
Common Troubleshooting Issues
Users can face a variety of challenges when using a Melt Flow Index Tester, including:
Material Not Flowing Properly โ Check the temperature settings and check that the polymer is completely melted.
Inconsistent Measurements โ Check the amount released and check the die for blockages or jams.
Erratic Digital Readings โ To restore accuracy, reset the equipment and adjust its sensors.
Polymer Degradation โ Avoid overheating materials over their melting point limitations, as this can result in poor performance.
Advanced Testing Considerations
For laboratories and research institutes performing advanced material analysis, the Melt Flow Index Tester can be added with extra testing processes. Different versions include:
Multi-Load Testing โ Using different weights to find out how the material reacts under different stress levels.
Shear Rate Analysis โ Measuring how the density of the polymer changes with flow rate.
Extended Dwell Time Tests โ Measuring changes in polymer characteristics after long exposure to heat.
Safety Guidelines
Using a Melt Flow Index Tester requires attention to important safety protocols:
Wear Protective Gear โ Protect yourself from burns by using thermal gloves and safety eyewear.
Avoid Direct Contact โ Avoid contacting the heated barrel or molten polymer.
Ensure Proper Ventilation โ To avoid exposure to vapors, perform experiments in fully ventilated places.
Handle Weights Carefully โ To avoid injury when handling heavy loads, use safe lifting procedures.
Applications of Melt Flow Index Testing
The Melt Flow Index Tester is widely used across multiple industries, including:
Plastic Manufacturing โ Ensures quality control in both raw materials and finished goods.
Automotive Industry โ Verifies that polymers meet the durability and performance requirements for car components.
Medical Devices โ Analyzes polymer quality for usage in healthcare industries.
Packaging Industry โ Finds out the flow characteristics of plastic films, containers and other packing materials.
Research & Development โ Assists in testing new polymer formulations for improved performance and sustainability.
Comparison with Other Polymer Testing Methods
While the Melt Flow Index Tester is commonly used, other forms of polymer testing include rheometry and capillary viscometry. A quick comparison:
Melt Flow Index Testing โ Provides quick and simple thickness measurements, but might not capture all features.
Rotational Rheometry โ Measures thickness at a variety of flow rates, but requires advanced devices.
Capillary Viscometry โ Provides accurate flow behavior analysis, but requires longer sample preparation.
Conclusion
The Melt Flow Index Tester is a useful instrument to analyze the properties of thermoplastic materials. When used correctly, it generates accurate and reliable outcomes, making it the best option for quality control and research purposes. Correct functioning, regular maintenance, and attention to standard testing techniques are required for maximum accuracy and productivity. Follow the guidelines suggested in this manual to achieve best reliability and performance in melt flow index testing.
Note: IndiBlogHub features both user-submitted and editorial content. We do not verify third-party contributions. Read our Disclaimer and Privacy Policyfor details.