Mercuric Chloride Production Cost Analysis 2025: Global and Regional Insights
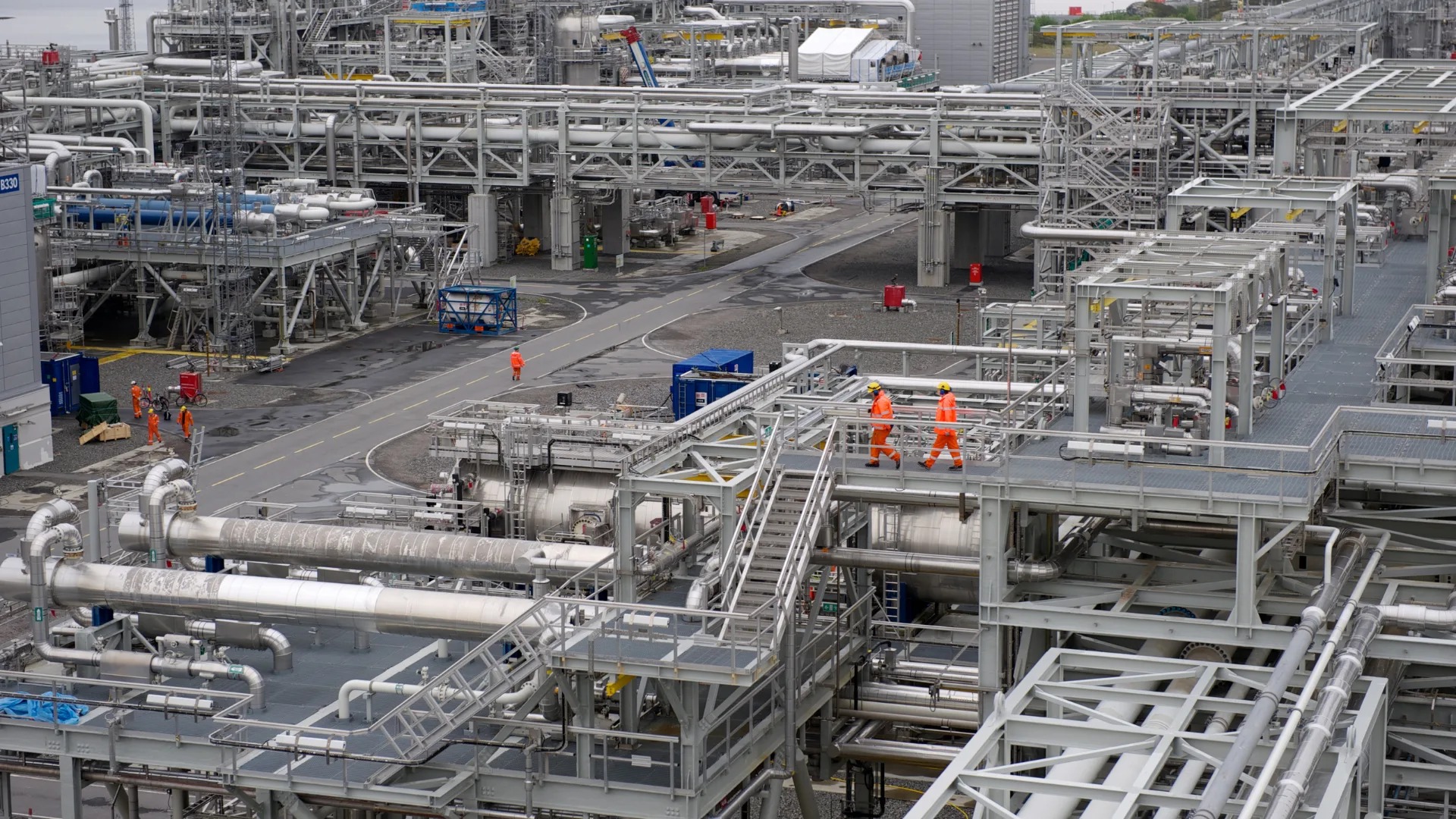
Mercuric Chloride Production Cost Analysis has become an essential reference point for entrepreneurs, investors, and MSMEs planning to enter the inorganic chemical manufacturing sector. With growing demand across research laboratories, pharmaceutical industries, and chemical synthesis applications, understanding the complete cost structure and feasibility of establishing a mercuric chloride manufacturing plant is critical. This analysis outlines the key cost determinants, including raw material requirements, machinery needs, setup cost analysis, and regional cost variation trends in 2025.
Overview of Mercuric Chloride Production
Mercuric chloride, also known as corrosive sublimate, is an inorganic compound typically synthesized through the reaction of elemental mercury with chlorine gas or via the chlorination of mercuric sulfate. The substance plays a vital role in a range of industrial and laboratory applications, such as fungicides, disinfectants, and catalyst agents in organic synthesis. Due to its toxic nature, production must adhere to stringent environmental and safety regulations, influencing both capital investment and operational costs.
Request a Sample Report: https://www.imarcgroup.com/mercuric-chloride-manufacturing-plant-project-report
What is Mercuric Chloride?
Mercuric chloride is a white crystalline compound made from mercury and chlorine, known for its powerful antiseptic and preservative properties. Historically used in medicine and disinfectants, it is now primarily applied in industrial processes such as chemical synthesis, wood preservation, and laboratory research. Despite its effectiveness, mercuric chloride is highly toxic and corrosive, requiring careful handling and strict safety measures. Exposure, even in small amounts, can pose serious health risks, including damage to the kidneys and nervous system. This has led to tighter regulations on its use and transport in many countries. Today, industries using mercuric chloride prioritize advanced safety protocols and environmental safeguards to ensure responsible usage. For businesses and manufacturers, understanding the nature and risks of this compound is crucial not only for compliance but also for ethical and sustainable operations. Its role in modern industry remains significant, but only under careful, controlled conditions.
Market Trends & Drivers of Mercuric Chloride:
The market for mercuric chloride is influenced by a mix of industrial demand, regulatory shifts, and growing environmental awareness. One of the key drivers is its continued use in specialized chemical synthesis and laboratory applications, where alternatives may not offer the same efficiency. However, rising health and environmental concerns are pushing industries to adopt safer handling practices and invest in compliant technologies. Regulatory bodies across the globe are tightening restrictions, which is prompting innovation in mercury management and safer production methods. In some regions, government support for industrial modernization and waste reduction is helping businesses upgrade facilities and stay competitive. While overall demand may remain steady, especially in research and niche manufacturing, the focus is clearly shifting toward sustainable practices. For entrepreneurs and MSMEs, staying ahead of these trends by aligning with safety and environmental standards can open doors to long-term growth and market trust.
Raw Material Requirements for Mercuric Chloride Manufacturing
One of the foundational aspects of Mercuric Chloride Production Cost Analysis is identifying and evaluating the raw material requirements. The core inputs include:
- Elemental Mercury: Sourced through recycling or mining, mercury forms the base reactant. Its procurement is subject to environmental controls and international trade regulations, affecting cost and availability.
- Chlorine Gas: Chlorine is typically generated through electrolysis and used in its gaseous form. The requirement for high-purity chlorine adds to the overall raw material cost.
- Supporting Chemicals: In some processes, additional reagents like nitric acid or sulfuric acid are employed for purification or conversion steps.
These raw materials contribute significantly to the variable cost component of production. Their price volatility, driven by supply chain disruptions and environmental policies, plays a central role in shaping production economics.
Machinery Requirements and Infrastructure
Machinery requirements for mercuric chloride production vary based on the process scale and technological sophistication. A detailed cost breakdown begins with identifying the essential equipment, which includes:
- Reactor Systems: These are corrosion-resistant units where the primary chemical reactions occur. Material selection, typically glass-lined or high-grade steel, impacts cost.
- Chlorine Handling Systems: Secure pipelines and scrubbers are essential for safely handling and neutralizing excess chlorine emissions.
- Distillation and Crystallization Units: These are used for product purification and recovery, contributing to both energy consumption and setup cost.
- Safety and Environmental Control Units: Specialized systems for fume extraction, waste treatment, and hazardous material storage are mandatory under global regulatory standards.
The machinery requirements significantly influence the fixed capital investment and are often tailored based on regional compliance norms and production capacity targets.
Setup Cost Analysis: Key Considerations
A thorough setup cost analysis involves both direct and indirect cost elements necessary for establishing a functional production plant. These include:
- Land and Building Costs: Location plays a major role in determining real estate prices, utility accessibility, and proximity to raw material sources and distribution hubs.
- Machinery Procurement and Installation: Capital expenditure on equipment and its installation is a critical component of the initial investment.
- Utility Infrastructure: Setting up electrical systems, water supply, and gas handling units involves additional capital costs.
- Labor and Administrative Expenses: Hiring skilled labor, compliance officers, and administrative staff represents a recurring cost in both setup and operational stages.
Furthermore, licensing, registration, and environmental clearance costs vary across jurisdictions, impacting the overall setup budget. These costs are vital for long-term compliance and risk mitigation.
Cost Breakdown in Mercuric Chloride Production
Understanding the detailed cost breakdown provides insights into the operational efficiency and scalability of a manufacturing unit. The typical cost components include:
- Raw Material Costs: As discussed earlier, these are highly variable and constitute a substantial portion of the total production cost.
- Energy and Utilities: The production process is energy-intensive, particularly in the heating and crystallization stages. Local energy tariffs can influence regional cost competitiveness.
- Labor Costs: Skilled technical personnel are required for handling hazardous substances and operating complex machinery.
- Maintenance and Depreciation: Periodic maintenance, equipment depreciation, and replacement costs must be accounted for in the long-term cost structure.
- Waste Treatment and Compliance: Treating hazardous waste and ensuring emissions control adds to both capital and recurring costs.
This cost breakdown forms the core of any Mercuric Chloride Production Cost Analysis, allowing stakeholders to assess profitability margins and optimize operational strategies.
Regional Insights and Global Cost Variations
The regional dimension of production cost is shaped by multiple factors such as labor availability, environmental regulations, and industrial infrastructure. Some key insights include:
- Asia-Pacific: Countries in this region, particularly in Southeast Asia, offer competitive labor costs and growing industrial hubs. However, regulatory tightening on mercury usage can influence long-term feasibility.
- North America and Europe: While these regions provide advanced infrastructure and technological know-how, stringent environmental laws and high energy costs contribute to elevated setup and operational expenses.
- Middle East and Africa: With improving industrial ecosystems and access to cheaper energy resources, these regions present emerging opportunities for cost-effective plant setup.
Entrepreneurs and investors must weigh these regional insights against their strategic objectives, regulatory risk appetite, and market access preferences.
Ask for Analysist For Customized Report: https://www.imarcgroup.com/request?type=report&id=9269&flag=C
Strategic Recommendations for New Entrants
To optimize the outcome of a mercuric chloride manufacturing venture, new entrants should consider the following strategic steps:
- Detailed Feasibility Study: A comprehensive cost-benefit analysis tailored to the selected region and market demand is essential before committing to capital investment.
- Supplier Agreements: Establishing stable, long-term agreements with raw material suppliers can help mitigate price volatility.
- Technology Selection: Adopting modular and energy-efficient machinery enhances scalability and reduces long-term operational costs.
- Environmental Compliance: Early engagement with regulatory bodies can expedite approvals and reduce compliance risks.
- Waste Management Planning: Proactive investment in waste treatment and emission control systems ensures sustainable operations and aligns with global ESG standards.
Conclusion
A robust Mercuric Chloride Production Cost Analysis offers valuable guidance for entrepreneurs, MSMEs, and investors seeking to establish a competitive foothold in the chemical manufacturing domain. From raw material requirements and machinery specifications to a comprehensive setup cost analysis and regional production insights, every element contributes to the viability of the investment. In an evolving regulatory and economic landscape, staying informed and strategically prepared is crucial for long-term success in mercuric chloride production.
Note: IndiBlogHub features both user-submitted and editorial content. We do not verify third-party contributions. Read our Disclaimer and Privacy Policyfor details.