Obtaining Quotes for Injection Molding Services: A Comprehensive Guide
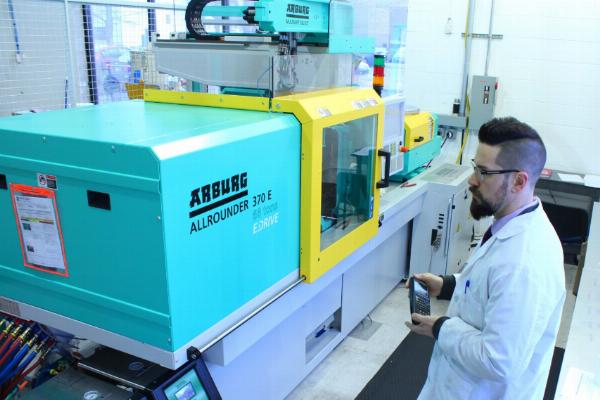
Securing accurate and competitive quotes for injection molding services is a crucial step in the manufacturing process. Whether you are developing a new product or ramping up production, understanding how to get quotes and what factors influence the cost can help you make informed decisions. This guide will walk you through the steps and considerations for obtaining injection molding quotes.
Steps to Obtain Injection Molding Quotes
Prepare Detailed Specifications:
Design Files: Provide 3D CAD files (such as STL, STEP, or IGES formats) of the parts you need to be molded. Detailed drawings can also be helpful.
Material Requirements: Specify the type of plastic material you want to use, such as ABS, PP, PC, or specialized materials like PEEK or PMMA.
Production Volume: Clearly state the quantity of parts you need, including any projections for future orders.
Identify Potential Suppliers:
Research: Look for reputable injection molding companies that have experience with your type of product and material. Consider companies both locally and internationally.
Certifications: Check if the suppliers have relevant certifications, such as ISO 9001, ISO 13485 (for medical devices), or other industry-specific standards.
Request Quotes:
RFQ (Request for Quotation): Send a formal RFQ to selected suppliers, including all relevant specifications and requirements. Be as detailed as possible to ensure accurate quotes.
Lead Times: Inquire about the lead times for tooling and production, as these can vary significantly between suppliers.
Evaluate Quotes:
Cost Breakdown: Ensure the quotes include a detailed cost breakdown, covering tooling costs, unit price, material costs, and any additional charges (such as shipping or post-processing).
Tooling Costs: These are typically a significant upfront investment. Understand the tooling lifetime and maintenance policies.
Unit Price: Compare the cost per part across different volume ranges to assess economies of scale.
Additional Services: Consider if the supplier offers design support, prototyping, assembly, or secondary operations that might add value to your project.
Assess Quality and Capabilities:
Sample Parts: Request sample parts or a small production run to evaluate the quality of the parts produced.
Quality Control: Inquire about the supplier’s quality control processes and inspection capabilities to ensure consistent part quality.
Negotiate Terms:
Payment Terms: Discuss payment terms and conditions, including any discounts for bulk orders or long-term contracts.
Lead Times: Negotiate lead times to align with your project timeline and production schedule.
Service Agreements: Ensure that all terms, including warranties and after-sales support, are clearly documented in a service agreement.
Factors Influencing Injection Molding Quotes
Tooling Costs:
Complexity of Design: More complex molds with intricate features or multiple cavities are more expensive to produce.
Tooling Material: High-grade steel molds last longer but are more costly than aluminum molds, which are suitable for lower volumes or prototyping.
Material Selection:
Type of Plastic: The cost of raw materials varies; engineering plastics like PEEK or PMMA are more expensive than standard materials like ABS or PP.
Material Properties: Special additives (e.g., UV resistance, flame retardants) can increase material costs.
Production Volume:
Economies of Scale: Higher production volumes typically reduce the unit cost due to the distribution of tooling costs over more parts.
Batch Sizes: Smaller batches may incur higher costs due to more frequent setup and changeover times.
Part Complexity:
Geometric Complexity: Parts with complex geometries, undercuts, or tight tolerances may require more advanced tooling and longer cycle times.
Size of the Part: Larger parts require more material and longer cooling times, impacting cycle times and costs.
Secondary Operations:
Post-Processing: Additional operations such as painting, coating, assembly, or machining add to the overall cost.
Quality Assurance: Enhanced quality control measures, such as detailed inspections or testing, can also increase costs.
Location of Supplier:
Local vs. Overseas: Offshore manufacturing can offer lower production costs but consider the trade-offs with shipping costs, lead times, and potential communication barriers.
Shipping and Logistics: Include the cost and time for shipping, customs duties, and potential delays in your cost evaluation.
Conclusion
Obtaining injection molding quotes involves careful preparation and consideration of various factors that influence cost and quality. By providing detailed specifications, researching potential suppliers, and thoroughly evaluating quotes, you can find a reliable injection molding partner that meets your technical and budgetary requirements. Remember to assess the total value offered by each supplier, including quality, lead times, and additional services, to make the best decision for your project.
Note: IndiBlogHub features both user-submitted and editorial content. We do not verify third-party contributions. Read our Disclaimer and Privacy Policyfor details.