OEE in Manufacturing Essential Knowledge for Operational Excellence
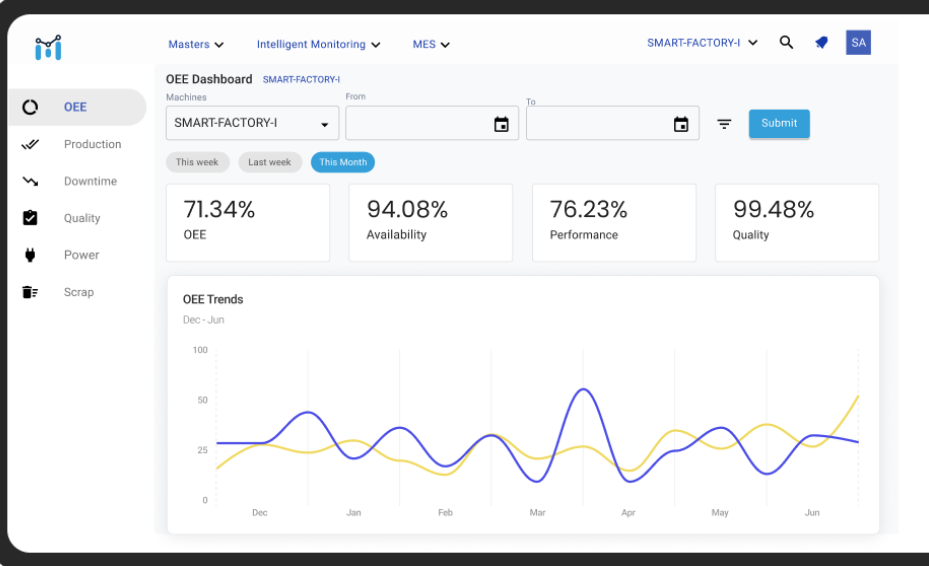
Efficiency is everything in the competitive manufacturing sector. Businesses who can rapidly create premium products with low waste have a clear advantage. Here is where Overall Equipment Effectiveness (OEE) comes in—a potent indicator that lets producers gauge and enhance the effectiveness of their manufacturing operations. Optimising production and profitability depends on knowing OEE in manufacturing, regardless of your position—plant manager, quality analyst, operations executive, or otherwise.
OEE stands for:
Manufacturing Oee in production is measured against OEE, or overall equipment effectiveness. It finds the proportion of manufacturing time that is really effective. With an OEE score of 100%, you are manufacturing just good components, fast enough, without downtime.
Comprising three elements, OEE is a composite measure:
Availability: The proportion of the allocated time the equipment can be run upon.
Performance: The machine's running speed expressed as a proportion of its intended speed.
Quality: The ratio of good to total units initially produced.
Your OEE score is obtained by three component multiplication:
OEE is availability times performance times quality.
Why OEE in Manufacturing Matters:
Measuring OEE in manufacturing helps companies identify areas needing improvement and the underlying reasons of production losses. Manufacturers run the danger of operating blindly without OEE, unable to recognise inefficiencies in their systems or the actual cost of downtime.
Here are main advantages of using OEE in production settings:
- OEE identifies production's inefficiencies and bottlenecks, so allowing focused process enhancements.
- Finding causes of unplanned downtime helps manufacturers to act early to stop equipment breakdowns.
- Clear view of quality losses allows teams to solve reoccurring flaws and increase consistency.
- OEE offers a basis for operational decisions anchored in actual performance data.
OEE in Production: Closing the Data and Action Gap
OEE in manufacturing offers the structure; OEE in production is where the metric is implemented. This entails exploiting OEE data on the shop floor actively in order to propel real-time enhancements. Teams track OEE at the line, machine, or shift level and monitor important performance indicators (KPIs) using dashboards or digital displays.
Real-Time Watch
Modern manufacturers immediately gather data straight from machines using IoT-enabled devices and software. These technologies instantly feedback on performance declines and calculate OEE in manufacturing in real time, therefore allowing quick response.
Root Cause Investigation
Production teams can employ root cause analysis (RCA) to ascertain whether mechanical faults, operator errors, material quality, or outside delays cause OEE measurements to fall short of target. RCA fuels ongoing development.
Benchmarking and Comparison Shifts
OEE also makes long-term benchmarks and shift-by- shift comparisons possible. This helps pinpoint areas where more instruction might be required, best practices, and outstanding teams.
Common OEE in Manufacturing Losses: Causes
One must first know where and why losses happen if one is to apply OEE properly. Every OEE component lends itself to particular loss classification:
Unplanned downtime, machine breakdowns, changeovers, setup time—losses in availability.
Performance Losses: Minor stops, operator inexperience, worn-out tools, speed loss
Errors in start-up, scrap, rework, setting, quality loss.
Through loss classification, firms can apply particular countermeasures including process automation, operator training, or preventative maintenance.
Methods to Boost Production OEE
Increasing OEE in manufacturing calls both methodical analysis and action. Here are tried techniques to improve OEE results:
Standardise Methodologies of Work
Different running techniques by operators for machines could result in performance losses. Standardising processes guarantees consistency and simplifies deviations' detection.
2. Preventive upkeep
Strong maintenance programs help to lower unplanned downtime. Plan services and inspections depending on usage patterns to maximise the lifetime of tools.
3. Applied Visual Management
Visual OEE dashboards on the production floor help teams remain informed of performance targets. Alerts coloured in colours indicate when measurements go below thresholds.
4. Track Data Automatically
Manual tracking leaves mistakes and delays quite prone. Use sensors and software designed to record real-time manufacturing data to simplify OEE monitoring.
5. Coach Operators on OEE.
Front lines are occupied by operators. Give them instruction on what OEE is, how it's computed, and how their behaviour affects the measure.
Calculating Success: What Should an OEE Score Be?
While it's hardly realistic, a "perfect" OEE score is 100%. Industry standards may differ:
Common for businesses just starting to track OEE is 40% to 60%.
For most manufacturers, 60%–80% is their average range.
Considered world-class for discrete manufacturing, 85% and above.
The aim should be constant improvement rather than perfection chasing. Little, steady improvements in availability, performance, or quality will over time significantly increase output.
OEE in Manufacturing: Looking Ahead
OEE is changing from a lagging indicator into a predictive and prescriptive tool as Industry 4.0 technologies get more common. To predict losses before they occur, maximise schedules, and lower waste, artificial intelligence and machine learning are being included into production monitoring systems.
Remote OEE tracking made possible by cloud-based systems also helps worldwide companies standardise performance monitoring throughout several facilities.
Conclusion
In manufacturing, OEE represents a philosophy of ongoing development rather than as a statistic. Applied correctly, OEE in production may match people, processes, and technology to reach operational excellence, hence driving significant change on the shop floor. Understanding and raising OEE helps firms lower costs, raise output, improve product quality, and raise customer satisfaction all around.
Any OEE in manufacturing trying to compete in the fast-paced, data-driven environment of today should give tools and training top strategic focus in OEE monitoring.
Note: IndiBlogHub features both user-submitted and editorial content. We do not verify third-party contributions. Read our Disclaimer and Privacy Policyfor details.