PEEK Injection Molding: Advanced Manufacturing for High-Performance Applications
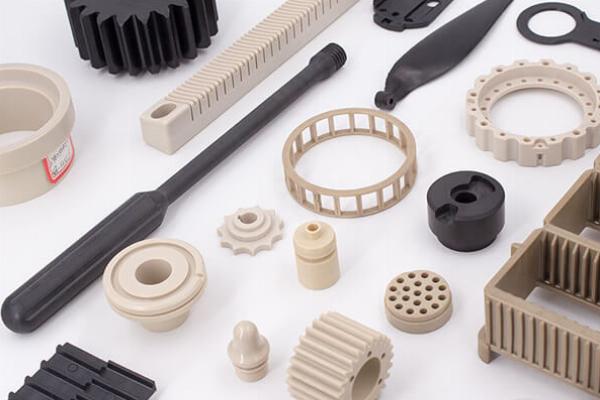
PEEK (Polyether ether ketone) is a high-performance engineering thermoplastic known for its exceptional mechanical properties, chemical resistance, and thermal stability. PEEK injection molding is a specialized manufacturing process that leverages these properties to produce high-quality components for demanding applications. This article will explore the process, benefits, and applications of PEEK injection molding.
What is PEEK Injection Molding?
PEEK injection molding involves the use of PEEK resin to create parts through the injection molding process. This process is similar to standard injection molding but requires specific considerations due to the unique properties of PEEK.
The PEEK Injection Molding Process
Material Preparation:
PEEK resin is typically supplied in pellet form and must be thoroughly dried before processing to prevent moisture-related defects. Drying is usually done at around 150°C for 3-4 hours.
Melting:
PEEK has a high melting temperature, typically between 343°C and 393°C. The resin is heated in the injection molding machine until it reaches the appropriate melt temperature.
Injection:
The molten PEEK is injected into a pre-heated mold cavity under high pressure. Due to its high melting temperature, PEEK requires robust and temperature-resistant molds.
Cooling:
The part is cooled within the mold until it solidifies. Proper cooling is crucial to ensure dimensional stability and to avoid warping or internal stresses.
Ejection:
Once cooled, the molded part is ejected from the mold. Post-processing steps such as machining or annealing may be necessary to achieve the desired properties and tolerances.
Benefits of PEEK Injection Molding
High Mechanical Strength:
PEEK components exhibit excellent mechanical properties, including high tensile strength, rigidity, and impact resistance, making them suitable for structural applications.
Thermal Stability:
PEEK maintains its mechanical properties at elevated temperatures, with a continuous service temperature of up to 250°C, and short-term exposure up to 300°C.
Chemical Resistance:
PEEK is highly resistant to a wide range of chemicals, including acids, bases, and organic solvents, which makes it ideal for use in harsh chemical environments.
Wear and Abrasion Resistance:
PEEK parts have low friction and high wear resistance, making them suitable for applications involving sliding contact or abrasive conditions.
Biocompatibility:
PEEK is biocompatible and can be sterilized using various methods, making it an excellent choice for medical implants and devices.
Applications of PEEK Injection Molding
Aerospace:
PEEK components are used in aerospace applications due to their high strength-to-weight ratio, thermal stability, and resistance to aggressive chemicals.
Automotive:
In the automotive industry, PEEK is used for under-the-hood components, electrical connectors, and transmission parts that require high performance and durability.
Medical Devices:
PEEK is utilized in medical applications for implants, surgical instruments, and dental devices due to its biocompatibility and resistance to repeated sterilization.
Electronics:
PEEK is employed in electronics for insulating components, connectors, and other parts that require excellent electrical properties and heat resistance.
Industrial Machinery:
PEEK parts are used in pumps, valves, and compressor components due to their ability to withstand high pressures, temperatures, and corrosive environments.
Challenges in PEEK Injection Molding
Processing Requirements:
PEEK’s high melting temperature and viscosity require specialized equipment and precise control over processing parameters.
Tooling Costs:
The molds for PEEK injection molding must be made from high-strength, temperature-resistant materials, which can be costly.
Material Cost:
PEEK resin is more expensive than many other thermoplastics, which can impact the overall cost of the molded parts.
Conclusion
PEEK injection molding is a vital process for producing high-performance parts that require exceptional mechanical properties, thermal stability, and chemical resistance. Its applications span across various demanding industries, including aerospace, automotive, medical, electronics, and industrial machinery. Despite the challenges associated with processing and cost, the benefits and versatility of PEEK make it a preferred material for critical applications where performance cannot be compromised. By leveraging the advanced capabilities of PEEK injection molding, manufacturers can achieve superior quality and reliability in their products.
Note: IndiBlogHub features both user-submitted and editorial content. We do not verify third-party contributions. Read our Disclaimer and Privacy Policyfor details.