Pharma 4.0: Advanced Continuous Pharmaceutical Tablet Manufacturing
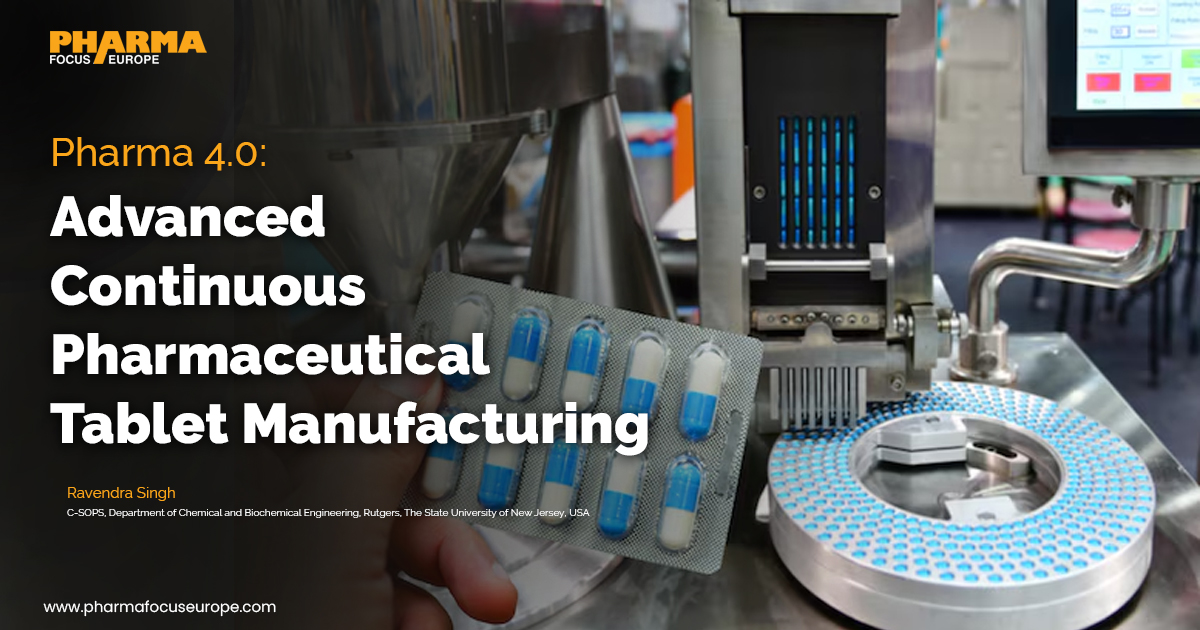
Pharma 4.0, an application of Industry 4.0 concepts in the pharmaceutical industry, aims to enhance manufacturing efficiency, product quality, and consistency. It faces challenges in areas like artificial intelligence, material traceability, optimization, process control, cyber-physical security, and data management due to the complexity involved. However, by incorporating artificial intelligence and advanced model predictive control with robust cyber-physical security measures, predictive capabilities and product quality can be significantly improved. This work focuses on implementing seven Industry 4.0 components, including AI/ML, modeling, material traceability, optimization, advanced control, cyber-physical security, and data science, in continuous pharmaceutical manufacturing processes.
Currently, Industry 4.0 concepts are being applied to the pharmaceutical industry to achieve Pharma 4.0 paradigm. It is promoted by both industries, academia and regulators. Pharma 4.0 reduces the time and resources needed for continuous pharmaceutical manufacturing and improves product quality and production consistency. It has many advantages but also have bigger challenges on the applications of artificial intelligence (AI)/machine learning (ML), material traceability, optimization, advanced process control, cyber-physical security, and data management side because of the different levels of complexities involved. The predictive capabilities and the quality of the pharmaceutical products can be improved significantly via employing the artificial intelligence and the advanced model predictive control (MPC) system if an appropriate cyber-physical security defense is in place.
In this work, seven components of Industry 4.0, namely artificial intelligence (AI)/machine learning (ML), modelling, optimization, advanced control, material traceability, cyber-physical security, and data science have been developed for the continuous pharmaceutical manufacturing process.
1. Process description
A continuous direct compaction tablet manufacturing pilot plant has been developed, situated at C-SOPS, Rutgers University, NJ, USA (Figure 1). This is vertical design of the plant that takes advantage of gravitational material flow and therefore no convayer belt is needed. This is direct compaction line that has three levels. The feeders are placed at top level to feed API and excipients. The co-mill and blender are placed in middle level. The API and excipient streams pass through the co-mill before entering to the bledner. The co-mill is used for delumping purposes. The lubricant feeder is also placed at middle level. The lubricant is directly fed to the blender without passing through the co-mill to avoid the over lubrication. The tablet press is placed on ground floor. A chute is placed in between blender and tablet press. The PAT sensor is integrated with the plant via chute interface.. The pharma 4.0 related tools are shown in Figure 1.
2. Development of industry 4.0 concepts for continuous pharmaceutical tablet manufacturing process
There are different methods and tools useful to achieve pharma 4.0 paradigm. Artificial intelligence (AI)/machine learning (ML), modelling, optimization, advanced control, material traceability, cyber-physical security, and data science have been developed for the continuous pharmaceutical manufacturing process.
2.1. Artificiel intelligence (AI)/ machine Learning (ML)
AI/ML algorithms have been highly successful in solving complex problems for many industries to predict the process response accurately. The pharmaceutical industry has yet to see the potential impact of a machine learning based self-trained process for efficient manufacturing of high-quality products. There are different AI approaches that may have potential applications in continuous pharmaceutical manufacturing. However, the identification of best performing AI method for continuous pharmaceutical manufacturing process is still a challenging task. In this work, four machine learning (ML) models have been trained to predict the response of continuous pharmaceutical manufacturing process and the performance of these ML models has been compared. The investigated ML methods are artificial neural network (ANN), 1D convolution neural network (CNN), long short-term memory (LSTM), and random forest (RF).
Inspired by the nervous system and chemical-based neuron activation in a biological brain, artificial neural networks (ANN) are a multi-layered black-box approach to digitally recreating non-linear systems' functionality with a series of interconnected signals that get sent to neurons.
Explore more: https://www.pharmafocuseurope.com/information-technology/pharma-advanced-continuous-pharmaceutical
Note: IndiBlogHub features both user-submitted and editorial content. We do not verify third-party contributions. Read our Disclaimer and Privacy Policyfor details.