Polyurethane Production Cost Analysis: Raw Material Requirements and Market Dynamics in 2025
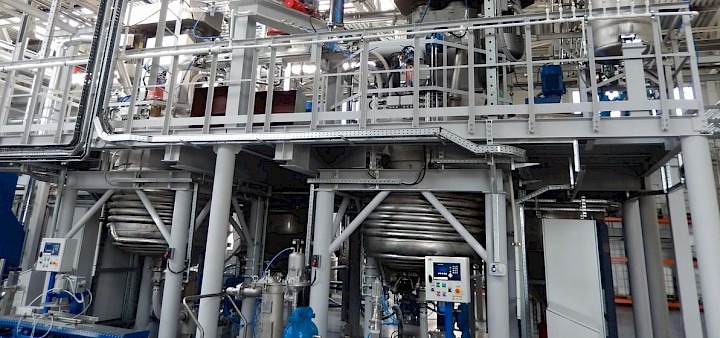
Polyurethane production cost analysis plays a crucial role in understanding the economic feasibility and strategic planning required to establish a successful manufacturing plant in 2025. For entrepreneurs, investors, and MSMEs aiming to enter this dynamic sector, a detailed understanding of cost structures, raw material requirements, machinery needs, and market drivers is essential. With growing applications in automotive, construction, electronics, and furniture industries, polyurethane remains one of the most versatile and in-demand polymer materials. This comprehensive analysis delves into the critical aspects influencing production costs and offers insight into setup strategies that can maximize returns while minimizing inefficiencies.
Understanding Polyurethane and Its Industrial Demand
Polyurethane is a polymer composed of organic units joined by carbamate (urethane) links. It can be tailored to be either rigid or flexible, making it suitable for diverse applications such as insulation panels, foams, coatings, adhesives, sealants, and elastomers. Global demand for polyurethane is projected to witness steady growth in 2025, driven by sustainability trends, lightweight automotive solutions, and energy-efficient construction materials.
This rising demand directly impacts the raw material supply chain, pricing strategies, and ultimately, the total polyurethane production cost. Therefore, a well-structured cost analysis is imperative for identifying profitability opportunities and avoiding common operational pitfalls.
Raw Material Requirements for Polyurethane Manufacturing
The raw material requirements form the core of polyurethane production cost analysis. The primary inputs include:
• Polyols: These are long-chain diols used to provide the soft segment of polyurethane. Common polyols include polyether polyols and polyester polyols.
• Isocyanates: Typically methylene diphenyl diisocyanate (MDI) or toluene diisocyanate (TDI), these react with polyols to form polyurethane.
• Additives: Catalysts, blowing agents, surfactants, stabilizers, flame retardants, and pigments are used depending on the end-product specifications.
• Solvents and Fillers: While not always necessary, these can be used to enhance processability or alter product characteristics.
In 2025, fluctuations in crude oil prices (from which many polyols and isocyanates are derived) are expected to significantly impact input costs. Additionally, increased regulatory pressure regarding environmentally friendly alternatives could influence sourcing and pricing strategies.
Request a Sample Report: https://www.imarcgroup.com/polyurethane-manufacturing-plant-project-report/requestsample
Machinery Requirements and Plant Setup
A polyurethane production facility requires a well-integrated system of equipment to ensure product quality and manufacturing efficiency. Key machinery requirements include:
• Reactors and Mixing Units: Used for precisely combining polyols and isocyanates under controlled conditions.
• Foaming Machines: Critical for producing flexible and rigid polyurethane foams in various densities.
• Casting and Molding Machines: Required for shaped products such as seats, panels, and insulation boards.
• Curing Chambers: Ensure proper polymerization and setting of the material.
• Quality Testing Equipment: Necessary to ensure that physical and chemical properties meet industry standards.
Depending on the plant scale, the setup cost can vary widely. Small and medium enterprises may start with modular, semi-automatic systems to reduce initial capital expenditure. However, automation and digital integration provide long-term advantages in quality control and operational efficiency.
Key Cost Factors in Polyurethane Production
A thorough polyurethane production cost analysis must incorporate all direct and indirect expenses. Key cost factors include:
1. Raw Material Costs: These represent the largest share, often exceeding 60% of the total production expense.
2. Utilities and Energy Consumption: Reactors and curing units are energy-intensive, particularly for high-volume continuous processes.
3. Labor and Skilled Workforce: Specialized training is required for handling isocyanates and maintaining chemical processing equipment.
4. Machinery Depreciation and Maintenance: Regular servicing is essential to maintain precision and product consistency.
5. Packaging and Storage: Depending on the product form—liquid, foam, or molded goods—storage conditions may vary.
6. Compliance and Waste Management: Environmental regulations mandate proper disposal or treatment of chemical waste, influencing operational costs.
Understanding these variables helps MSMEs and investors benchmark their expenditure against industry norms and identify areas for cost optimization.
Setup Cost Analysis for 2025: Capital Investment Outlook
The setup cost analysis of a polyurethane plant in 2025 depends on several factors such as production capacity, product range, level of automation, and geographical location. On average:
• Small-scale facility (2–5 tons/day): $500,000 to $1.5 million
• Medium-scale facility (10–20 tons/day): $2 million to $5 million
• Large-scale automated plant (50+ tons/day): $10 million and above
Costs include plant construction, machinery acquisition, installation, initial raw material inventory, workforce recruitment, and regulatory certifications. Strategic location selection can reduce logistics costs and ease access to key markets and raw materials.
Cost Optimization Strategies for Polyurethane Plants
In an increasingly competitive market, deploying effective cost optimization strategies is essential to remain profitable. Common approaches include:
• Sourcing Alternatives: Building a diversified supplier base for polyols and isocyanates helps manage price volatility.
• Process Efficiency: Implementing lean manufacturing and real-time process control systems can reduce material waste and energy consumption.
• Technology Upgradation: Investing in modern machinery with energy-saving features minimizes long-term operational costs.
• Product Diversification: Expanding into high-margin products such as medical-grade foams or bio-based polyurethane can improve revenue per unit cost.
• Supply Chain Integration: Vertical integration with raw material producers or downstream users offers better pricing control and logistical benefits.
These strategies not only reduce costs but also position the business to scale sustainably in the evolving polyurethane landscape.
Ask Analyst for Customization Report: https://www.imarcgroup.com/request?type=report&id=9075&flag=C
Market Dynamics and Regulatory Trends in 2025
The global polyurethane market is expected to reach a valuation of over $90 billion in 2025, growing at a CAGR of 5–6%. Demand is particularly strong in Asia-Pacific, where urbanization, infrastructure development, and automotive production continue to rise.
At the same time, increasing focus on sustainability is leading to:
• Development of bio-based polyurethanes
• Phase-out of harmful blowing agents
• Tighter restrictions on VOC emissions
Entrepreneurs and investors must align their production methods with these evolving regulatory requirements to secure long-term market relevance. Incorporating circular economy principles and green chemistry can also improve brand equity and attract eco-conscious consumers.
Conclusion
A detailed polyurethane production cost analysis is indispensable for any entrepreneur, investor, or MSME planning to establish a manufacturing plant in 2025. By carefully evaluating raw material requirements, machinery investments, and key cost factors, businesses can devise a cost-effective and scalable setup. Additionally, incorporating robust cost optimization strategies and adapting to market dynamics enhances long-term profitability and competitiveness. With the right combination of strategic planning, technological integration, and market insight, polyurethane manufacturing can offer substantial returns in the coming years.
Note: IndiBlogHub features both user-submitted and editorial content. We do not verify third-party contributions. Read our Disclaimer and Privacy Policyfor details.