Reciprocating Mud Pumps, The Powerhouses Behind Efficient Drilling Operations
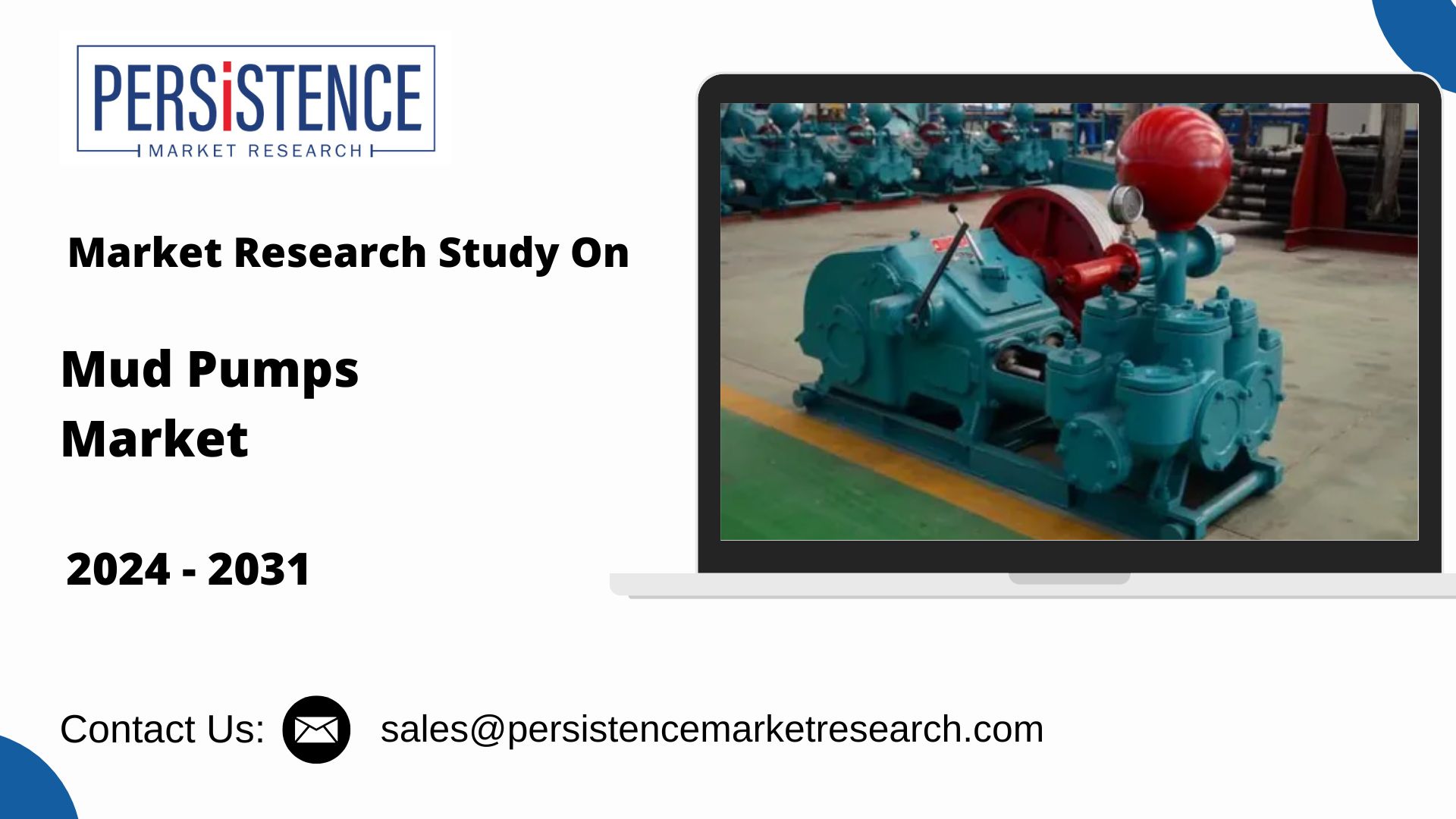
In the world of drilling, whether it's for offshore oil platforms or onshore oil fields, the efficiency of operations depends heavily on the performance of essential equipment. One such critical piece of equipment is the reciprocating mud pump.
These mud pumps market are vital to ensuring the smooth flow of drilling fluids, also known as mud, throughout the wellbore during drilling operations.
A reciprocating mud pump is a type of positive displacement pump that relies on the back-and-forth motion of a piston or plunger to move fluid. This design makes them the preferred choice for handling the high-pressure requirements typically seen in oil and gas drilling. In this article, we will explore how reciprocating mud pumps serve as the "powerhouses" behind efficient drilling operations, focusing on their functionality, advantages, and impact on the drilling process.
1. Understanding the Role of Reciprocating Mud Pumps in Drilling Operations
Mud pumps are a core component of the drilling fluid circulation system. Their main purpose is to circulate drilling mud through the wellbore, from the surface down to the drill bit, and back to the surface. The fluid is responsible for several essential functions:
Cooling and lubricating the drill bit to minimize wear.
Carrying rock cuttings from the bottom of the well to the surface.
Maintaining wellbore stability and controlling pressure within the well.
In reciprocating mud pumps, the motion of the piston or plunger drives the fluid through the pump, creating a high-pressure environment necessary to lift cuttings and circulate the mud back up to the surface. These pumps are designed to handle extremely high pressures, often exceeding 10,000 psi, making them suitable for the demanding environments of deepwater drilling, high-pressure, high-temperature (HPHT) fields, and onshore operations with challenging conditions.
2. How Reciprocating Mud Pumps Work
The working principle of a reciprocating mud pump revolves around the movement of a piston or plunger within a cylinder. The process typically involves several key steps:
a. Suction Stroke
The suction stroke begins when the piston moves backward (away from the pump discharge side). This creates a vacuum within the pump, allowing the drilling fluid to be drawn into the cylinder from the suction side.
b. Discharge Stroke
As the piston moves forward (toward the discharge side), it forces the fluid through a discharge valve and into the drilling fluid circulation system. The fluid then travels down the wellbore to the drill bit, where it performs its functions of cooling, cleaning, and pressure control.
c. Continuous Operation
Reciprocating mud pumps are designed to operate continuously, with the piston moving back and forth at a steady pace to ensure a constant flow of fluid. These pumps typically operate in a set of three or more to provide continuous fluid circulation and ensure that no interruption occurs during the drilling process.
3. Types of Reciprocating Mud Pumps
There are two primary types of reciprocating mud pumps commonly used in the oil and gas industry: triplex and duplex pumps.
a. Triplex Mud Pumps
Triplex mud pumps are the most commonly used type in drilling operations. They feature a three-cylinder design, with three plungers working in unison to create a continuous flow of fluid. These pumps offer high flow rates and are capable of handling high-pressure operations, making them ideal for deepwater drilling, HPHT wells, and other demanding drilling environments.
Advantages of Triplex mud pumps:
Higher pressure capabilities for deep or difficult wells.
Increased efficiency due to the synchronized operation of three pistons.
Reliable fluid flow, minimizing downtime during drilling operations.
b. Duplex Mud Pumps
Duplex mud pumps, in contrast, use a two-cylinder design and are typically used for less demanding applications compared to triplex pumps. While they offer slightly lower pressure capabilities, they are often more cost-effective and easier to maintain.
Advantages of Duplex mud pumps:
Compact design, suitable for smaller-scale drilling operations.
Lower operational cost due to fewer components.
Reliability in medium-pressure environments, such as onshore drilling.
4. Key Benefits of Reciprocating Mud Pumps
Reciprocating mud pumps offer several advantages that make them indispensable in modern drilling operations:
a. High Pressure Capabilities
One of the primary reasons reciprocating mud pumps are favored in drilling operations is their ability to handle high-pressure requirements. In deepwater drilling and HPHT fields, pressure can reach up to 20,000 psi or higher. Reciprocating pumps, especially triplex models, are capable of sustaining these extreme pressures, ensuring efficient fluid circulation even in the most challenging environments.
b. Durability and Reliability
Reciprocating pumps are known for their durability and ability to operate continuously without failure. With proper maintenance, these pumps can perform reliably for extended periods. Their robust design ensures they are capable of withstanding the wear and tear associated with high-pressure, high-flow environments, which is crucial for avoiding costly downtime.
c. Versatility
Reciprocating mud pumps are versatile, capable of handling a wide variety of drilling fluids, including water-based, oil-based, and synthetic muds. This versatility is essential for adapting to the specific requirements of different well types and drilling conditions. Whether it's a simple onshore well or a complex offshore deepwater well, reciprocating pumps can handle the unique fluid circulation demands of each operation.
d. Easy Maintenance
Although reciprocating pumps are complex in design, they are relatively easy to maintain. Key components such as the piston, valves, and seals are designed for easy access and replacement. Regular maintenance and monitoring ensure that the pumps can operate at peak efficiency throughout the drilling process, reducing the likelihood of unexpected breakdowns.
5. Innovations Driving Reciprocating Mud Pump Efficiency
In recent years, there have been several innovations that have improved the performance, efficiency, and reliability of reciprocating mud pumps:
a. Advanced Materials
Manufacturers have introduced advanced materials for critical components like pistons and plungers to enhance the strength and resilience of reciprocating mud pumps. These materials are specifically designed to withstand the abrasive nature of drilling fluids and the extreme pressures of deepwater drilling.
b. Monitoring and Automation Systems
Modern reciprocating mud pumps are equipped with digital sensors and real-time monitoring systems that allow operators to track performance metrics such as flow rate, pressure, and temperature. These monitoring systems help optimize pump efficiency, alert operators to potential issues, and enable predictive maintenance to prevent failures before they occur.
c. Energy-Efficient Designs
With the increasing push for energy efficiency in drilling operations, manufacturers have been focusing on designing reciprocating pumps that consume less power while delivering the required performance. Innovations such as variable-speed drives help reduce energy consumption without compromising on pumping efficiency.
6. Challenges and Solutions
While reciprocating mud pumps are essential to drilling operations, they are not without challenges. One of the primary challenges is the wear and tear that can occur over time, especially when dealing with abrasive drilling fluids or high-pressure environments. To address this, regular maintenance and the use of wear-resistant coatings on key components have become standard practices to extend the life of the pump and reduce downtime.
7. Conclusion
Reciprocating mud pumps are the backbone of efficient and reliable drilling operations, particularly in high-pressure, deepwater, and complex drilling environments. Their ability to handle extreme pressures, high-flow rates, and abrasive fluids makes them essential for maintaining smooth operations across both onshore and offshore drilling sites. With ongoing innovations in materials, monitoring systems, and energy-efficient designs, reciprocating mud pumps will continue to play a critical role in shaping the future of drilling operations, ensuring greater reliability, reduced operational costs, and enhanced overall performance in the oil and gas industry.
Note: IndiBlogHub features both user-submitted and editorial content. We do not verify third-party contributions. Read our Disclaimer and Privacy Policyfor details.