Refractory Bricks Types in High Temperature Industrial Processes
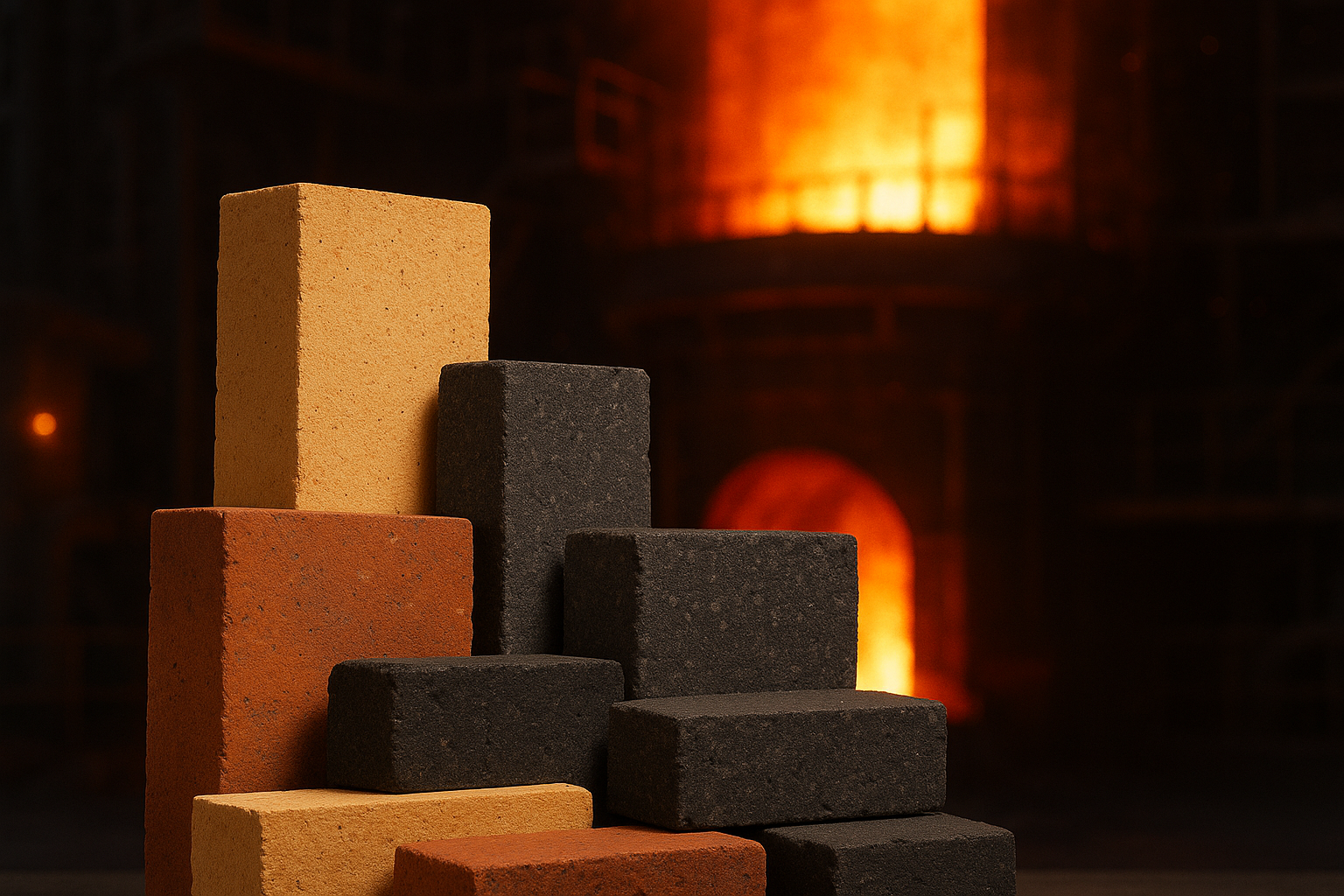
Refractory bricks, often called fire bricks, are indispensable material in a wide range of high temperature industrial processes. You will see them in the fiery heart of a blast furnace and the intense heat of a cement kiln. These specialized materials are engineered to withstand extreme conditions that would quickly degrade ordinary materials.
This comprehensive guide delves into the world of refractory bricks, exploring their diverse refractory brick types, crucial properties, varied applications, and the critical factors to consider when selecting the right brick for a specific need. We will also address some common challenges and discuss best practices for optimizing performance and longevity.
Defining Refractory Bricks and Their Importance
Refractory bricks are engineered systems designed to maintain structural integrity and chemical stability in the face of extreme temperatures, corrosive environments, and mechanical stress.
Your decision of selecting the appropriate refractory bricks is not a trivial matter. It is a critical decision that directly impacts many industrial operations' safety and productivity. For a comprehensive selection, exploring reputable fire bricks manufacturers is a good starting point.
Classifying Refractory Bricks by Composition and Application
Refractory bricks are typically categorized based on their chemical composition because they dictate their performance in different environments. Every businessperson must understand the intended application is equally important. Here is a closer look at the different types of refractory bricks.
1. Acidic Refractory Bricks:
These bricks are designed for use in environments dominated by acidic substances.
Silica Bricks:
Composed primarily of silica (over 93%), these bricks are known for their excellent thermal shock resistance. This characteristic makes them ideal for applications involving rapid temperature fluctuations, such as glass furnaces and coke ovens. However, they are vulnerable to attack by alkaline materials. A key consideration when using silica bricks is their volume stability at high temperatures because proper expansion joints are crucial to prevent cracking.
Ganister Bricks
Similar to silica bricks in their high silica content, ganister bricks also contain small additions of lime and clay. These additions enhance their high-temperature durability and resistance to certain types of chemical attack. They are often used in applications where slightly higher mechanical strength is required than pure silica bricks can offer.
2. Basic Refractory Bricks
These bricks are specifically designed for use in alkaline or basic environments because they make them essential in metal refining processes.
Magnesite Bricks
Manufactured from magnesium oxide (MgO), these bricks are renowned for their ability to withstand extremely high temperatures, often reaching up to 2100°C (3812°F). They are commonly used to line furnaces and kilns in the steel industry. A challenge with magnesite bricks is their susceptibility to hydration, so proper storage and handling are essential.
Dolomite Bricks
Containing high levels of dolomite these bricks are particularly effective in environments with basic slags and byproducts of metal smelting. They offer a cost-effective alternative to magnesite bricks in certain applications. Like magnesite bricks, dolomite bricks are also vulnerable to hydration.
3. Neutral Refractory Bricks
These versatile bricks can be used in both acidic and alkaline environments, offering greater flexibility in certain applications. These are also considered among the different types of fire bricks.
Chromite Bricks
Composed of chromium and iron oxides, these bricks exhibit exceptional mechanical strength and resistance to corrosion. They are particularly valuable in the non-ferrous metal industries, where they are used in furnaces and other high-temperature equipment. Chromite bricks can be challenging to manufacture, which contributes to their cost.
Spinel Bricks
Made from alumina (Al2O3) and magnesia (MgO), these bricks provide an excellent balance of mechanical strength, thermal stability, and chemical resistance. They are often used in cement kilns and other demanding high-heat applications. Spinel bricks offer good resistance to thermal shock and are less susceptible to hydration than magnesite or dolomite bricks.
Essential Properties of Refractory Bricks
Understanding the specific properties of refractory bricks is crucial for proper selection.
High Thermal Resistance
This measures the temperature at which a standard cone of the material softens. It's a key indicator of the brick's ability to withstand high temperatures.
Chemical Stability
This encompasses resistance to acids, bases, and other corrosive substances. The specific chemical environment of the application is paramount in selecting the right brick.
Mechanical Strength
This measures the brick's ability to withstand compressive forces at room temperature. It's an important consideration for load-bearing applications.
Thermal Conductivity
This measures the brick's ability to transfer heat. Lower thermal conductivity means better insulation.
Thermal Expansion
Understanding how the brick expands and contracts with temperature changes is crucial for designing proper joints and preventing cracking.
Porosity
The percentage of open space within the brick. Porosity affects thermal conductivity, strength, and resistance to chemical attack.
Applications Across Industries
Refractory bricks find application in a wide array of industries
Metallurgical Industry
In steelmaking, they line blast furnaces, basic oxygen furnaces, electric arc furnaces, ladles, and tundishes. Each of these applications demands specific refractory properties.
Cement and Glass Industry
They are used extensively in rotary kilns, calciners, and melting furnaces. The chemical environment and high temperatures in these processes require specialized refractory solutions.
Power Generation
They are employed in boilers, incinerators, and fluidized bed combustors. The increasing use of alternative fuels presents new challenges for refractory materials.
Petrochemical Industry
They are used in reactors, reformers, and other high-temperature processing units. The complex chemical environments in this industry require careful selection of refractory bricks.
Conclusion
Refractory bricks are vital for the success of numerous high-temperature industrial operations. A thorough understanding of the various types of refractory bricks, their properties, and their applications is essential for making well-informed choices.
By carefully evaluating all critical factors and partnering with trusted experts like Ganesha's Refractory, you can select the ideal fire bricks to maximize the efficiency, safety, and lifespan of your industrial equipment. Additionally, ongoing advancements in refractory technology continue to introduce innovative materials, offering superior performance and durability to meet the ever-evolving demands of modern industries.
Note: IndiBlogHub features both user-submitted and editorial content. We do not verify third-party contributions. Read our Disclaimer and Privacy Policyfor details.