The ABCs of ABS: Unraveling the Characteristics and Uses of Acrylonitrile Butadiene Styrene (2023-2034)
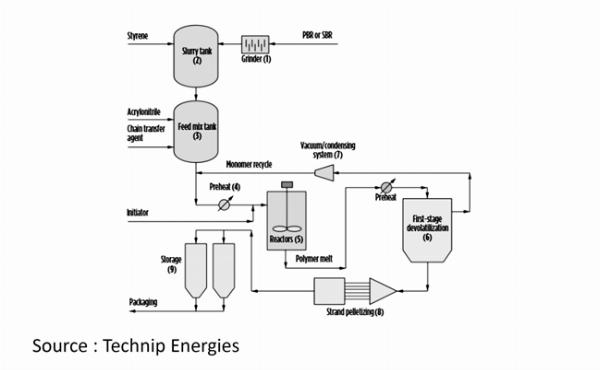
This blog will focus on Acrylonitrile Butadiene Styrene (ABS). ABS is comprised of three monomers: Acrylonitrile, Butadiene, and Styrene. In this article, we'll look at how the polymer's unique properties work together to give ABS its exceptional strength, toughness, as well as the manufacturing process. The global Acrylonitrile Butadiene Styrene (ABS) market is likely to flourish at a moderate CAGR of 5.90% by the year 2034.
Introduction
Styrene Acrylonitrile has existed since the 1940s. While they improved toughness over pure styrene, their limits necessitated the addition of rubber (butadiene) as a third monomer. ABS consists of three major monomers: acrylonitrile, butadiene, and styrene.
Acrylonitrile contributes to ABS's chemical resistance and heat stability.
Butadiene enhances the toughness and impact strength of ABS.
Styrene provides ABS with rigidity and facilitates its processability.
Manufacturing Process
ABS copolymers exhibit notable toughness, superior thermal resistance, and properties that surpass those of polystyrene plastics. ABS is produced through three distinct polymerization techniques: emulsion, suspension, and mass processes.
In the Mass Process, ABS is produced by the continuous copolymerization of styrene and acrylonitrile monomers with Polybutadiene Rubber (PBR) or Styrene-Butadiene Rubber (SBR) using a series of reactors, aided by organic peroxide. In a sequential process, chopped PBR or SBR is added to a slurry tank containing styrene monomer. The resultant mixture is then transferred to the ABS feed batch tank for complete rubber dissolution. This concentrated rubber solution is diluted with acrylonitrile, recycled monomer, and a chain transfer agent according to product requirements before preheating prior to entering the polymerization reactors.
Polymerization Section
The polymerization section employs a unique combination of plug flow and boiling stirred tank reactors arranged in series. Organic peroxide is introduced to initiate polymerization. This reactor setup allows precise control over various parameters such as rubber grafting, phase inversion, and molecular weight. Monomer conversion increases progressively throughout the reactor system, reaching final levels between 60% to 75%. Devolatilization is achieved through either extrusion or flash chamber methods.
Devolatization
In the extrusion devolatilization approach, the product from the last reactor undergoes stripping of unreacted monomers and byproducts in an extruder devolatilization system. Alternatively, the reactor product is subjected to volatile removal in a multistage flash devolatilization system operating under vacuum. Vapors are condensed, and the resulting mixture is recycled. The devolatilized polymer melts and then pelletizes and then dried.
Applications of Acrylonitrile Butadiene Styrene (ABS):
ABS (Acrylonitrile Butadiene Styrene) finds numerous applications across various industries. High impact grades are utilized in the production of travelling bags, helmets, furniture, sports goods, and automotive components, while medium impact grades are employed in radiator and air conditioner grills, heavy-duty domestic appliances, and control panels. Electroplating grades find their place in TV and radio knobs, bathroom fittings, refrigerator handles, and nameplates. High flow grades are ideal for housing domestic appliances, office equipment, and cabinets of electronic devices. High heat-resistant grades are utilized in automobile components and housing for electrical heaters and dryers. Transparent grades are sought after for areas requiring high transparency and impact strength, while impact modifier grades serve as modifiers for PVC compounding across various formulations. Glass-filled grades cater to applications demanding high flexural strength and stiffness, maintaining impact and tensile properties, while extrusion grades are used in refrigerator linings and luggage production.
Automotive
The automotive industry demands stringent standards from its materials. They must remain dimensionally stable and resist warping even when subjected to extreme stresses and significant temperature fluctuations.
Electronics & Electricals
ABS stands out in this regard due to its outstanding antistatic properties, providing a distinct advantage in meeting these requirements.
Appliances
ABS finds extensive applications in appliances, encompassing appliance control panels, housings for various devices such as shavers, vacuum cleaners, and food processors, as well as refrigerator liners, among others. Household and consumer goods represent the primary domains where ABS is widely utilized. Additionally, ABS is commonly employed in the manufacturing of keyboard keycaps.
Pipes & Fittings
ABS pipes and fittings are highly liked due to their ease of installation and rust resistance, making them a popular choice in a variety of applications.
Market Outlook:
ABS is an invariable thermoplastic polymer made up of three distinct monomers: acrylonitrile, butadiene, and styrene, which can change in proportion. They are also referred to as engineering plastics. Acrylonitrile provides chemical and thermal stability, styrene gives the plastic a glossy sheen, and butadiene provides strength and durability. These materials are widely used in the electronic appliance and automobile industries for vehicle and auto components production. The rapid growth of the medical business has increased demand for medical equipment, which is driving market growth. Furthermore, the growing construction and aerospace industries are predicted to significantly boost the ABS sector during the projection period. The global Acrylonitrile Butadiene Styrene (ABS) market is anticipated to reach approximately 15.7 million tonnes by 2034.
Acrylonitrile Butadiene Styrene (ABS) Major Manufacturers
Significant companies in the Global Acrylonitrile Butadiene Styrene (ABS) market are Formosa Chemicals and Fiber Corporation, LG Chem, LOTTE Chemical Corporation, Jilin Petrochemical Company, Toray Industries, CHIMEI Corporation, Tianjin Dagu Chemical Co., Ltd., and Others.
Challenges and Opportunities
While ABS possesses numerous advantageous properties, there are several restraining factors that could impact its market growth:
Environmental Concerns: ABS is derived from petrochemical sources, and its production and disposal can contribute to environmental pollution. Increasing environmental consciousness, combined with strict laws on plastic waste management and recycling, may present difficulties to the ABS market.
Competition from Alternative Materials: ABS faces competition from other engineering thermoplastics, such as polycarbonate (PC) and polypropylene (PP), which offer similar or enhanced properties in certain applications.
Conclusion:
Acrylonitrile Butadiene Styrene (ABS) is a versatile polymer with numerous useful applications. It is an essential in automotives and Electrical & Electronics industries owing to its unique set of properties. The surging demand for Acrylonitrile Butadiene Styrene (ABS) from Automotive, Home Appliances, Electrical & Electronics, and Building & Construction end-use industries, is anticipated to play a role in the demand-supply dynamics of the Acrylonitrile Butadiene Styrene (ABS) market.
Note: IndiBlogHub features both user-submitted and editorial content. We do not verify third-party contributions. Read our Disclaimer and Privacy Policyfor details.