The Evolution of Dual Inline Package Technology
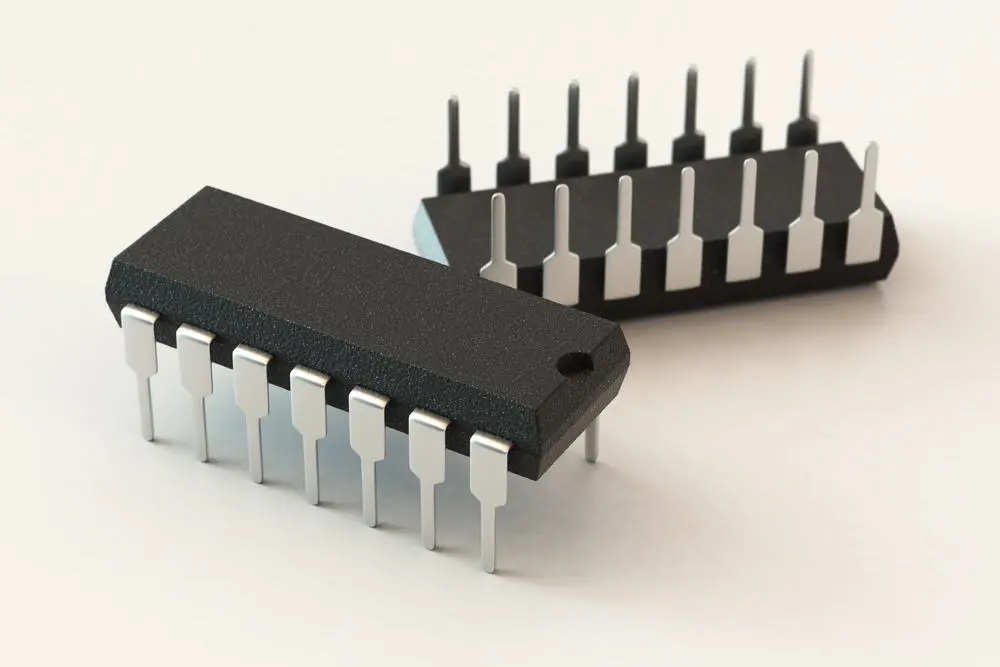
Introduction
In the world of electronics, the Dual Inline Package (DIP) has been a cornerstone in the development of circuit boards and devices.
Characterized by its two parallel rows of connecting pins, DIP technology facilitated significant advancements in electronics manufacturing and design. For more information about the meaning of Dual Inline Package, KingSunPCB has made the ultimate summary.
This article provides a comprehensive look at how DIP technology evolved, its impact on the electronics world, and its status in the modern technological landscape.
The Birth of DIP
Origins and Early Development
The inception of DIP technology dates back to the 1960s, a time when the electronics industry was seeking more efficient ways to integrate and connect components.
DIP was revolutionary, offering a standardized and compact way to organize electronic components on a circuit board. The design was simple: a rectangular chip with two rows of pins on either side, which could be easily inserted into a socket or soldered onto a board.
First Uses in Electronics
Initially, DIPs were predominantly used in computer systems, particularly for memory chips and microprocessors. Their ease of use and practical design made it possible for manufacturers to produce more complex and reliable electronics.
This period marked the beginning of rapid technological development, fueled in part by the versatility and functionality of DIPs.
Evolution and Advancements
Technological Improvements
As the demand for more sophisticated electronics grew, so did the technology behind DIPs. The packages became smaller, more efficient, and were made to withstand varying environmental conditions. Innovations such as shrink DIP (SDIP) and skinny DIP (SKDIP) emerged, which offered reduced sizes and pin counts adapted to more compact circuit boards.
Adoption Across Industries
Beyond personal computers, DIP technology spread to other areas such as telecommunications, consumer electronics, and automotive systems. This broad adoption underscored the versatility of DIPs, proving that they could meet diverse technological needs and applications.
Decline and Niche Status
Shift to Surface Mount Technology
The late 1980s and early 1990s saw a shift towards Surface Mount Technology (SMT), which allowed components to be mounted directly onto the surface of circuit boards. SMT was more space-efficient and suited to automated manufacturing processes, leading to a gradual decline in the use of DIPs in mass-produced electronics.
Current Niche Applications
Despite being overshadowed by newer technologies, DIPs have not disappeared. They remain popular in prototyping, educational kits, and in applications where manual adjustments and replacements are necessary.
Their ease of use and the ability to quickly change components without specialized equipment make DIPs ideal for learning environments and DIY projects.
The Legacy and Future of DIP
Lasting Impact on Electronics Design
DIPs laid the groundwork for modern electronic design, establishing standards that are still in use today. The concept of pin configuration and package standardization introduced with DIPs influences how current technologies are developed and implemented.
Future Prospects
Although DIPs are no longer at the forefront of technology, they continue to be relevant in specific sectors, particularly in education and in areas requiring high reliability and easy maintenance. DIP plays a key role in PCB assembly. If you want to know more about PCB, please visit the official website: kingsunpcba.com
Emerging technologies occasionally integrate DIP configurations to leverage these benefits.
Conclusion
The evolution of Dual Inline Package technology is a testament to its lasting impact on the field of electronics.
From powering the early computers to teaching the fundamentals of electronic design, DIPs have played a pivotal role in the technological advancements we see today.
As the industry moves forward, the principles pioneered by DIP technology will continue to influence and shape future innovations.
Note: IndiBlogHub features both user-submitted and editorial content. We do not verify third-party contributions. Read our Disclaimer and Privacy Policyfor details.