The Importance of Quality Control in Syrup Manufacturing
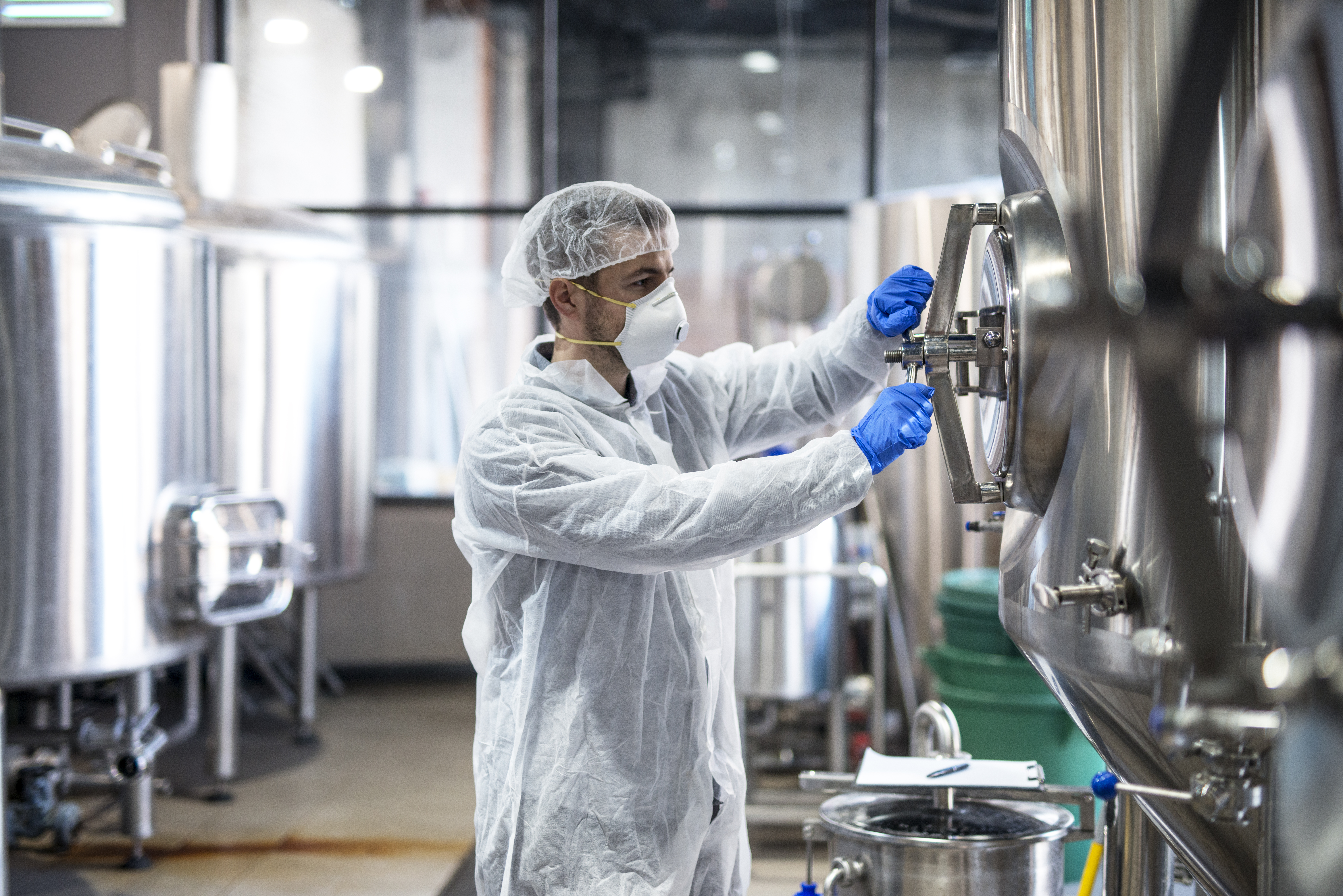
Quality control plays a crucial role in ensuring the safety, effectiveness, and consistency of pharmaceutical products, especially in syrup manufacturing. Whether it’s a liquid syrup or a dry syrup, every step of the manufacturing process requires strict monitoring to guarantee that the final product is safe for consumers. Pharmaceutical syrup manufacturers and dry syrup manufacturers must maintain high-quality standards to prevent errors that could harm patients or impact the effectiveness of the medicine. Let’s dive deeper into why quality control is so important and how it impacts syrup manufacturing.
What is Quality Control in Syrup Manufacturing?
Quality control in syrup manufacturing is the process of ensuring that each batch of syrup whether liquid or dry meets the required standards for safety, potency, and consistency. From sourcing raw materials to packaging the final product, every step of the process is carefully monitored to ensure that the syrup is safe for use and effective in treating the intended condition.
For pharmaceutical syrup manufacturers, this process involves a series of checks and tests designed to ensure the final product adheres to all regulatory standards and meets patient safety requirements.
Why is Quality Control Essential?
Ensuring Patient Safety
The most important reason for quality control in syrup manufacturing is to ensure patient safety. Pharmaceutical syrups are often used by children, the elderly, and other vulnerable groups. If there is any variation in the syrup’s ingredients, potency, or consistency, it can have serious consequences. Quality control ensures that each bottle contains the correct dosage, the ingredients are safe, and there are no contaminants present.
Consistency Across Batches
Consistency is key in pharmaceutical manufacturing. Patients expect the same effectiveness from each bottle of syrup, and healthcare professionals rely on manufacturers to provide a product that meets specific standards. Without rigorous quality control, syrups might vary from batch to batch, leading to inconsistent treatment outcomes. Ensuring each batch of syrup is consistent helps maintain trust in the product and the manufacturer.
Regulatory Compliance
Pharmaceutical syrup manufacturers must adhere to strict guidelines set by health authorities like the Food and Drug Administration or the European Medicines Agency. These regulations are in place to protect consumers from unsafe products. Through quality control, manufacturers can meet regulatory requirements, avoiding costly recalls or penalties that could damage the company’s reputation.
Product Stability
Pharmaceutical syrups need to be stable throughout their shelf life. Factors like temperature, humidity, and light can affect the stability of the syrup. Dry syrup manufacturers, in particular, face additional challenges because the powdered form is more sensitive to moisture. Quality control checks help ensure that the syrup will remain effective, potent, and safe for consumption until its expiry date.
Key Elements of Quality Control in Syrup Manufacturing
Raw Material Testing
The first step in quality control begins with the raw materials used to make the syrup. Ingredients such as active pharmaceutical ingredients (APIs), flavoring agents, preservatives, and excipients must meet specific standards. Quality control checks ensure that these raw materials are sourced from trusted suppliers and are free from contaminants or defects. Any substandard raw material can compromise the final product’s quality.
In-Process Monitoring
Throughout the manufacturing process, pharmaceutical syrup manufacturers need to monitor the syrup’s characteristics to ensure it is developing as expected. This includes testing for factors such as viscosity, pH levels, and the uniformity of ingredients. These tests help detect any problems during production, allowing for quick corrective actions before a batch goes out of specification.
Microbial Testing
Microbial contamination is a serious concern in the manufacturing of pharmaceutical syrups. Syrups can be breeding grounds for bacteria, fungi, or other harmful microorganisms. Regular microbial testing ensures that syrups are free from harmful pathogens that could pose a health risk to consumers. This is especially important for dry syrup manufacturers, as the powder must be free from microorganisms that could multiply when reconstituted with water.
Stability Testing
Syrups must maintain their quality over time. Stability testing involves placing syrups under different environmental conditions, such as varying temperatures and humidity, to ensure that they maintain their safety and effectiveness until the product expires. These tests help identify the shelf life of the syrup and any potential changes in taste, appearance, or potency.
Packaging Checks
After the syrup is manufactured and tested, it is packaged for sale. Packaging plays an essential role in maintaining the quality of the syrup. Quality control checks ensure that the packaging is airtight, tamper-proof, and able to protect the syrup from light and moisture. For dry syrup manufacturers, proper sealing is crucial to avoid moisture absorption, which can affect the syrup’s quality.
The Role of Technology in Quality Control
Advancements in technology have significantly improved the quality control process in syrup manufacturing. Automated systems now help in monitoring temperature, viscosity, and other factors more accurately and efficiently than ever before. Additionally, technology allows manufacturers to track the testing and quality control results in real-time, providing more transparency and traceability in the production process.
Technological tools such as data analytics can also be used to predict potential issues in syrup production, allowing manufacturers to take proactive measures before problems arise. This helps in maintaining a consistent product and avoiding costly recalls.
Challenges Faced by Dry Syrup Manufacturers
While the importance of quality control applies to both liquid and dry syrup manufacturers, dry syrup manufacturers face unique challenges:
Moisture Sensitivity
Dry syrups are sensitive to moisture, which can cause the powder to clump together or lose potency. Dry syrup manufacturers must ensure that the manufacturing environment is dry and that the packaging is moisture-proof. Without proper quality control, there is a risk that the dry syrup may not dissolve properly when reconstituted.
Accurate Reconstitution
For dry syrups, the reconstitution process is crucial. The patient is required to add water to the dry powder to create a liquid syrup. Quality control ensures that the powder is evenly distributed and will dissolve properly in water. Any issues in this process could result in an incorrect dose or ineffective treatment.
Packaging and Storage
Dry syrup manufacturers need to ensure that the powder is stored and transported under appropriate conditions. Improper packaging can lead to contamination, moisture absorption, or loss of potency. Rigorous quality control during packaging and storage is necessary to maintain the product’s effectiveness until it reaches the consumer.
Conclusion
Quality control in syrup manufacturing is not just about following regulations—it’s about ensuring that every bottle of syrup is safe, effective, and consistent. Pharmaceutical syrup manufacturers and dry syrup manufacturers must maintain strict quality control measures to protect patients and maintain the trust of healthcare professionals. By focusing on the safety of raw materials, in-process testing, microbial testing, stability, and packaging, manufacturers can produce a reliable and effective product.
Note: IndiBlogHub features both user-submitted and editorial content. We do not verify third-party contributions. Read our Disclaimer and Privacy Policyfor details.