The Intricate World of Injection Mold Making
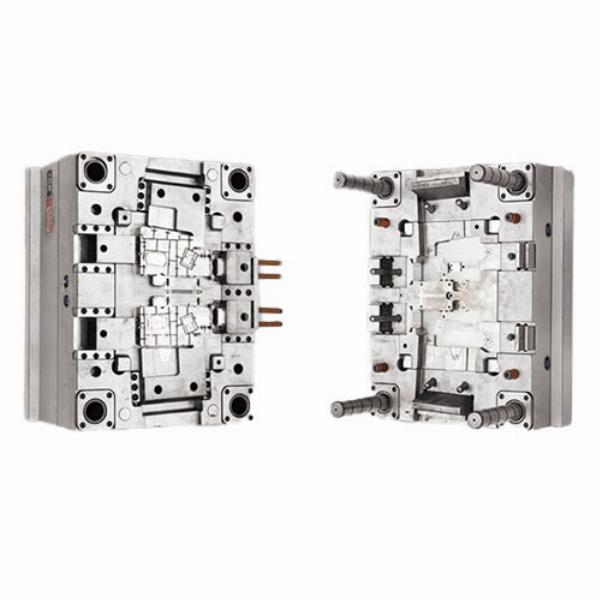
Introduction
Injection mold making is a crucial aspect of the manufacturing industry, enabling the production of complex and precise parts through the injection molding process. Crafting these molds requires a high level of expertise and attention to detail, as they must meet exact specifications to ensure the quality and consistency of the final products. This article explores the intricacies of injection mold making, from design to fabrication, and highlights its importance in various industries.
Understanding Injection Mold Making
What is Injection Mold Making?
Injection mold making is the process of creating molds that are used in injection molding machines to produce parts by injecting molten material into the mold cavity. These molds are typically made from durable materials like steel or aluminum and are designed to withstand the high pressures and temperatures of the injection molding process.
The Role of Molds in Injection Molding
Molds are at the heart of the injection molding process. They determine the shape, size, and surface finish of the final product. The accuracy and quality of the mold directly impact the efficiency and consistency of the manufacturing process.
The Injection Mold Making Process
Step 1: Concept and Design
The mold-making process begins with a detailed concept and design phase. This involves creating a 3D model of the part to be produced and designing the mold based on this model. Considerations include the part's geometry, material, and the injection molding machine's capabilities.
Step 2: Material Selection
Choosing the right material for the mold is critical. Common materials include hardened steel for high-volume production and aluminum for prototyping or low-volume production. The material must be durable and capable of withstanding the repeated cycles of the injection molding process.
Step 3: CNC Machining
Once the design is finalized, CNC (Computer Numerical Control) machining is used to cut the mold components with high precision. This step involves milling, drilling, and turning to create the mold's cavities and cores.
Step 4: Heat Treatment
Heat treatment is often applied to steel molds to enhance their hardness and durability. This process involves heating the mold components to a high temperature and then cooling them rapidly to achieve the desired mechanical properties.
Step 5: EDM (Electrical Discharge Machining)
For complex geometries and fine details, EDM is used. This process uses electrical discharges to erode material from the mold, allowing for precise shaping and finishing.
Step 6: Polishing and Surface Treatment
Polishing and surface treatments are essential to achieve the desired surface finish on the molded parts. Techniques like grinding, honing, and coating are used to ensure the mold surfaces are smooth and free from defects.
Step 7: Assembly and Testing
The final step involves assembling the mold components and testing the mold to ensure it meets the required specifications. Trial runs are conducted to identify and rectify any issues before full-scale production begins.
Materials Used in Mold Making
Hardened Steel
Hardened steel is the preferred material for high-volume production molds due to its exceptional durability and resistance to wear and tear.
Aluminum
Aluminum is commonly used for prototype molds and low-volume production. It is easier to machine and less expensive than steel but not as durable.
Copper Alloys
Copper alloys are used for specific applications requiring excellent thermal conductivity and reduced cycle times.
Applications of Injection Mold Making
Automotive Industry
Injection mold making is vital in the automotive industry for producing components like dashboards, bumpers, and engine parts with high precision and consistency.
Consumer Electronics
The consumer electronics industry relies on injection molds to create housings, connectors, and other intricate parts for devices like smartphones and laptops.
Medical Devices
Precision molds are essential for manufacturing medical devices, including syringes, implants, and diagnostic equipment, where accuracy and sterility are paramount.
Packaging Industry
Injection molds are used to produce a wide range of packaging products, from bottles and containers to caps and closures, ensuring uniformity and quality.
Advantages of Precision Mold Making
High Precision and Accuracy
Injection molds are crafted with meticulous precision, ensuring that the final products meet exact specifications and tolerances.
Consistency in Production
High-quality molds enable consistent production of parts, essential for maintaining quality standards in mass production.
Cost Efficiency
Although the initial cost of mold making is high, the durability and longevity of the molds result in cost efficiency over high-volume production runs.
Complex Geometries
Advanced mold-making techniques allow for the creation of complex geometries and fine details that would be challenging to achieve with other manufacturing methods.
Challenges in Injection Mold Making
High Initial Costs
The design and fabrication of injection molds require significant investment in materials, machinery, and skilled labor.
Design Complexity
Designing molds for complex parts can be challenging and requires a deep understanding of material behavior and injection molding principles.
Lead Time
The mold-making process can be time-consuming, with lead times varying based on the complexity of the mold and the part design.
Maintenance and Wear
Over time, molds can wear and require maintenance or refurbishment to ensure they continue to produce high-quality parts.
Innovations in Injection Mold Making
Advanced CAD/CAM Software
The use of advanced CAD (Computer-Aided Design) and CAM (Computer-Aided Manufacturing) software streamlines the design and machining processes, improving accuracy and efficiency.
Additive Manufacturing
Additive manufacturing, or 3D printing, is increasingly being integrated into mold making for rapid prototyping and creating complex mold components.
Improved Materials
Research into new materials and coatings enhances the durability and performance of injection molds, reducing maintenance requirements and extending their lifespan.
Quality Control in Mold Making
Inspection Techniques
Advanced inspection techniques, such as coordinate measuring machines (CMM) and laser scanning, ensure the molds meet precise dimensional specifications.
Testing and Validation
Trial runs and validation processes are conducted to test the molds under actual production conditions, ensuring they perform as expected.
Continuous Improvement
Implementing feedback loops and continuous improvement practices helps identify areas for enhancement, improving mold quality and performance over time.
Environmental Considerations
Sustainable Materials
The use of sustainable materials and practices in mold making reduces the environmental impact and promotes eco-friendly manufacturing.
Energy Efficiency
Improving the energy efficiency of mold-making processes and equipment helps reduce the carbon footprint of manufacturing operations.
Future of Injection Mold Making
Smart Manufacturing
The integration of IoT (Internet of Things) and smart technologies in mold making leads to more efficient, adaptive, and intelligent manufacturing processes.
Sustainable Practices
The industry continues to explore sustainable practices, including the use of biodegradable materials and improved recycling methods.
Global Trends
Global trends in mold making indicate a growing demand for high-precision, lightweight, and durable components across various sectors.
FAQs
What factors influence the cost of injection mold making?
Factors include material selection, mold complexity, production volume, and the precision required for the final parts.
How long does it take to make an injection mold?
Lead times vary based on complexity and design but typically range from several weeks to a few months.
Can molds be reused for different parts?
While molds are usually designed for specific parts, modifications can be made to adapt them for different components within certain limitations.
What maintenance is required for injection molds?
Regular maintenance includes cleaning, inspection, and repair of any worn or damaged components to ensure the mold continues to produce high-quality parts.
How does mold design impact the final product?
Mold design directly affects the quality, consistency, and functionality of the final product. Precise design ensures accurate dimensions and smooth surfaces.
What are the latest trends in injection mold making?
Current trends include the use of advanced materials, integration of additive manufacturing, and the adoption of smart manufacturing technologies.
Conclusion
Injection mold making is a sophisticated and vital process in modern manufacturing, enabling the production of high-quality, complex parts with remarkable precision. By understanding the steps involved, materials used, and the latest innovations, businesses can leverage mold making to achieve efficiency and excellence in production. As technology and sustainable practices continue to evolve, the future of injection mold making looks promising, offering even greater capabilities and environmental benefits.
Note: IndiBlogHub features both user-submitted and editorial content. We do not verify third-party contributions. Read our Disclaimer and Privacy Policyfor details.