The Modular Construction Market: Revolutionizing Building Practices
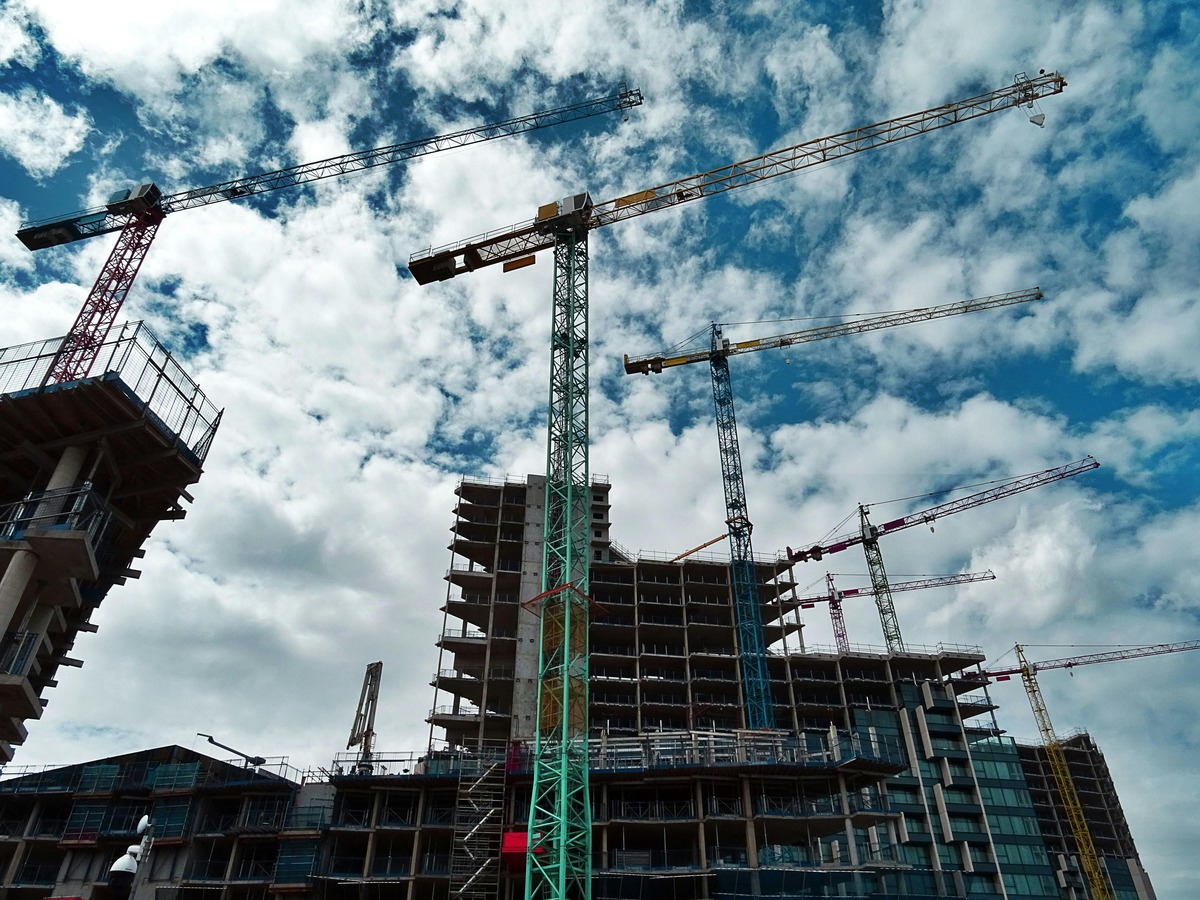
The Modular Construction Market has been making waves in the construction industry, offering a transformative approach to traditional building practices. This construction method, characterized by prefabricated modules that are assembled offsite, has gained immense popularity due to its efficiency, cost-effectiveness, and sustainable benefits. As the demand for quick and affordable construction rises, the modular construction market is seeing exponential growth. This blog dives deep into the modular construction market, exploring its advantages, challenges, key players, recent trends, and its potential for shaping the future of construction.
1. What is Modular Construction?
At its core, modular construction involves creating standardized building sections, or modules, in a factory setting. These prefabricated modules can range from small components like walls and ceilings to entire rooms or floors. Once completed, they are transported to the construction site, where they are assembled to form a finished structure. Unlike traditional construction methods, which build structures onsite from scratch, modular construction allows for simultaneous work on both the building’s foundation and the prefabricated modules, significantly speeding up the overall process.
2. Advantages of Modular Construction
Speed and Efficiency
Modular construction reduces project timelines by as much as 50% compared to traditional construction. This is primarily because of the concurrent nature of modular building, where site preparation and module fabrication happen simultaneously. With timelines shortened, construction firms can complete projects faster, reducing labor costs and maximizing profitability.
Cost Savings
Modular construction typically requires fewer materials, less onsite labor, and shorter project timelines, contributing to substantial cost savings. Factories can purchase materials in bulk, reducing costs and material waste. Moreover, the reduction in time spent on the construction site lowers labor costs and minimizes disruption for surrounding areas.
Enhanced Quality Control
Modules are built in a controlled environment, allowing for stringent quality checks at every stage. Unlike onsite construction, which can be affected by weather and environmental factors, factory-built modules maintain consistency in quality. This control ensures that materials are stored properly, measurements are accurate, and every module meets predefined standards.
Sustainability
Modular construction’s controlled environment leads to reduced waste, making it an eco-friendly alternative to traditional construction. Additionally, factories can recycle unused materials, reducing the environmental footprint further. Moreover, modular buildings can be disassembled and relocated, making them ideal for companies looking to minimize waste and contribute to sustainable practices.
Safety
By shifting much of the work to a factory setting, modular construction reduces the hazards associated with onsite building. Factory settings provide better control over safety protocols, limiting accidents and ensuring workers operate in a safer environment. This safety aspect is particularly attractive for large construction projects with numerous workers involved.
3. Challenges Facing Modular Construction
Logistical Complexities
Transporting large modules from factories to the construction site can be challenging, especially for urban projects where traffic and narrow roads pose obstacles. Additionally, managing the logistics of delivering modules in the correct sequence and on time requires meticulous planning, adding another layer of complexity.
Limited Flexibility
While modular construction is efficient, it can be restrictive in design flexibility. Since modules are created in a factory, last-minute design changes can be difficult and costly. This challenge is particularly significant for custom projects that require unique designs, which might limit the market appeal for high-end or highly customized constructions.
Building Code and Zoning Issues
Modular buildings must adhere to local building codes, which can vary widely. Factories producing modular components need to ensure that their products meet these regulations, which can be challenging in regions with stringent or varying codes. Furthermore, some local governments are hesitant to accept modular buildings, viewing them as non-traditional structures.
4. Key Players and Market Segmentation
The modular construction market has several prominent players, including companies like Laing O’Rourke, Katerra, Red Sea Housing, Sekisui House, and Skanska AB. These companies focus on different segments within the modular construction market, from residential to commercial and industrial.
Residential Segment
The demand for modular residential units has skyrocketed, especially in urban areas with high housing demand. Modular homes are seen as a solution to housing shortages, providing affordable, quick-to-assemble units without sacrificing quality.
Commercial Segment
Modular construction in the commercial sector includes hotels, office buildings, and retail spaces. With the need for rapid expansion and cost-effective solutions, modular construction has become a preferred choice for businesses looking to establish or expand their physical footprint quickly.
Industrial Segment
The industrial segment utilizes modular construction for buildings like warehouses, manufacturing facilities, and storage units. The flexibility of modular construction aligns well with the requirements of industrial buildings, which often need simple, functional, and quickly assembled structures.
5. Trends Shaping the Modular Construction Market
Green and Sustainable Construction
As sustainability takes center stage globally, modular construction companies are prioritizing eco-friendly practices. Some firms are experimenting with sustainable materials such as recycled steel and eco-friendly insulation. Additionally, modular buildings can incorporate energy-efficient systems, like solar panels, to further reduce their environmental impact.
Technological Integration
The integration of Building Information Modeling (BIM), 3D printing, and robotics in modular construction has streamlined design processes, improving efficiency and accuracy. BIM allows teams to create detailed digital models, reducing errors and enabling smoother coordination between factory and onsite teams. Robotics has also played a role in automating repetitive tasks, speeding up production and ensuring consistent quality.
Focus on Affordable Housing
With rising real estate prices and urban housing shortages, modular construction has become instrumental in addressing affordable housing needs. Governments and non-profit organizations are increasingly investing in modular housing projects, creating quality, low-cost housing that can be delivered quickly to those in need.
Offsite Construction as a Service (OCAAS)
OCAAS is an emerging business model where companies provide modular construction as a service. Under this model, the service provider manages everything from design to module production, transportation, and onsite assembly. This trend simplifies the process for clients and reduces the need for extensive involvement in the construction process.
6. Future Prospects of Modular Construction
The modular construction market shows no signs of slowing down, with market forecasts predicting steady growth over the next decade. Factors driving this growth include an increasing population, urbanization, and a growing focus on sustainable construction practices. As modular construction becomes more mainstream, the industry is likely to see greater innovation, especially as technology continues to advance. New materials, improved logistics, and enhanced design flexibility will likely address some of the current limitations of modular construction.
Furthermore, government support in many countries is bolstering the market’s growth. For instance, countries facing housing crises are offering incentives for modular construction projects to meet housing demand quickly and efficiently. Similarly, the commercial sector’s growing need for rapid expansion will continue to push the modular construction market forward.
7. Conclusion: A New Era in Construction
Modular construction is reshaping the construction industry, offering a modern, efficient, and sustainable solution for building in today’s fast-paced world. By providing quicker construction timelines, cost savings, quality control, and eco-friendly options, modular construction stands as a promising alternative to traditional methods. However, the industry faces challenges such as logistical constraints, limited flexibility, and regulatory hurdles. Overcoming these challenges will require collaboration between governments, construction firms, and technology providers.
As the modular construction market evolves, we can expect it to become an integral part of urban planning and development worldwide. The future of construction lies in modularity, where innovation meets efficiency, bringing new possibilities for how we think about and approach building. In a world that demands sustainable, affordable, and rapid solutions, modular construction is more than a trend—it’s the future of the built environment.
Note: IndiBlogHub features both user-submitted and editorial content. We do not verify third-party contributions. Read our Disclaimer and Privacy Policyfor details.