Ultimate Guide to Liquid Filling Machines: Types, Applications, and Buying Tips
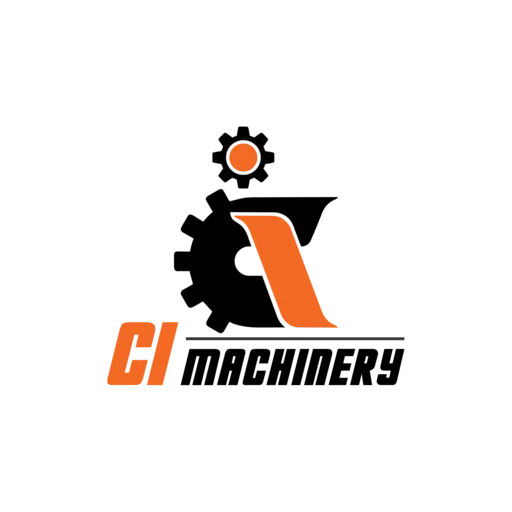
In today’s fast-paced industrial landscape, liquid filling machines play a critical role in packaging efficiency, precision, and hygiene. At our company, we understand the importance of selecting the right filling solution for your production line. In this comprehensive guide, we dive deep into every aspect of liquid filling machines, from types and functionalities to maintenance and best practices, ensuring you make informed decisions that optimize productivity and product quality.
What is a Liquid Filling Machine?
A liquid filling machine is an automated or semi-automated system used to accurately dispense liquids into containers, bottles, or pouches. These machines are indispensable across industries such as food and beverage, pharmaceutical, cosmetic, chemical, and petrochemical.
With increasing demand for consistency, speed, and hygiene, liquid filling machines have evolved to incorporate advanced technologies like PLC control systems, servo motors, and touchscreen HMIs.
Types of Liquid Filling Machines
1. Gravity Fillers
Gravity filling machines rely on the force of gravity to fill containers with thin, free-flowing liquids like water, vinegar, or juice. These are ideal for products that do not foam and require simple, low-cost solutions.
2. Pressure Fillers
These machines use pressure to fill containers with thicker liquids such as sauces, oils, or shampoos. Pressure filling machines are especially useful in high-speed production environments.
3. Vacuum Fillers
Used mainly for low-viscosity liquids, vacuum fillers draw liquid into the container by creating a vacuum within the bottle. They’re widely used in industries where maintaining product purity is vital.
4. Piston Fillers
Piston filling machines are highly accurate and capable of handling a variety of liquid viscosities. Ideal for creamy or chunky products like peanut butter or cosmetic gels, these machines use a piston-cylinder mechanism for precise volumetric filling.
5. Peristaltic Pump Fillers
Mostly used in pharmaceutical and biotech applications, peristaltic pump fillers are suitable for sterile and precise small-volume fillings. The liquid only contacts the tubing, making cleaning and changeovers quick and contamination-free.
Applications of Liquid Filling Machines
Food and Beverage Industry
From juices and sauces to condiments and dairy products, liquid filling machines ensure hygienic, tamper-proof, and efficient filling that adheres to food safety regulations.
Pharmaceutical and Healthcare
Accuracy is paramount when it comes to medications and supplements. Machines equipped with high-precision dosing systems and cleanroom compatibility meet the stringent requirements of this industry.
Cosmetics and Personal Care
Lotions, creams, serums, and oils demand not only accuracy but also gentle handling to preserve their texture and efficacy. Liquid filling solutions for this sector often include features like anti-drip nozzles and adjustable fill speeds.
Chemical Industry
From household cleaners to industrial lubricants, these machines handle a wide range of chemicals—some corrosive, flammable, or toxic. This requires corrosion-resistant components, explosion-proof designs, and safety interlocks.
Key Features to Look for in a Liquid Filling Machine
1. Filling Accuracy
Opt for a machine with a high-precision filling system to reduce product waste and meet regulatory standards. Features like digital flow meters, servo-controlled pistons, and weighing systems are highly beneficial.
2. Versatility
A good machine should accommodate various container types and sizes. Modular designs and adjustable filling heads ensure your production line stays flexible.
3. Speed and Efficiency
Speed is vital in mass production. Evaluate machines based on containers per minute (CPM) and downtime minimization technologies, such as automatic bottle indexing and changeover-free operations.
4. Clean-in-Place (CIP) Capability
To comply with hygiene standards, especially in food and pharma industries, choose machines with CIP or SIP (Sterilize-in-Place) features that allow automated internal cleaning.
5. User Interface and Control System
A touchscreen HMI, integrated PLC system, and intuitive software enhance operational control and troubleshooting, making your production line smoother and more manageable.
Choosing the Right Liquid Filling Machine for Your Business
Step 1: Define Your Liquid Characteristics
Is your product foamy, thick, or corrosive? Understanding the liquid's viscosity, temperature, and chemical nature is critical to choosing the right filling technology.
Step 2: Identify Your Packaging Needs
Are you filling bottles, jars, tubes, or pouches? Different containers require specialized nozzles, handling systems, and orientation tools.
Step 3: Determine Production Volume
Your average daily or hourly output should dictate whether you need a semi-automatic, fully-automatic, or rotary filling system.
Step 4: Consider Expansion Plans
Invest in machines that offer scalability. Modular systems that allow adding more filling heads or conveyor integrations save long-term costs.
Step 5: Budget Wisely
While initial investment is important, evaluate total cost of ownership—including maintenance, energy consumption, and potential product loss due to inaccuracies.
Maintenance and Troubleshooting Tips
Proper maintenance ensures the longevity and efficiency of your liquid filling machine. Follow these tips for optimal performance:
Regular Lubrication: Keep moving parts well-oiled to reduce wear and tear.
Scheduled Calibration: Check and adjust filling accuracy periodically.
Clean After Every Shift: Prevent residue buildup to avoid contamination and clogging.
Check Nozzles and Hoses: Inspect for blockages or wear regularly.
Train Operators Thoroughly: Well-trained personnel can detect issues early and reduce downtime.
Top Liquid Filling Machine Manufacturers
When investing in a liquid filling system, it’s crucial to source from reputed manufacturers. Some of the top names in the industry include:
Krones AG – Known for their high-speed beverage filling systems.
Tetra Pak – Specializing in hygienic food-grade solutions.
GEA Group – Providing pharma and cosmetic filling lines.
Accutek Packaging Equipment – Offering versatile and affordable filling solutions.
Future Trends in Liquid Filling Technology
1. Smart Automation
IoT-enabled machines that provide real-time diagnostics, predictive maintenance alerts, and remote monitoring are becoming mainstream.
2. AI and Machine Learning Integration
Some modern systems are beginning to use AI algorithms to optimize fill speeds and detect anomalies during operation.
3. Sustainable and Eco-Friendly Designs
Manufacturers are increasingly focusing on energy-efficient motors, minimal wastage technologies, and biodegradable packaging compatibility.
Conclusion
Investing in the right liquid filling machine can significantly boost production efficiency, product consistency, and overall profitability. By understanding the various types, applications, features, and maintenance requirements, businesses can make informed choices tailored to their unique needs.
Why Liquid Filling Machines are the Backbone of Modern Manufacturing
In high-volume industries, consistency, speed, and precision are non-negotiable. A liquid filling machine ensures each unit gets the right amount of liquid product—every single time. Whether you’re running a beverage factory or producing pharmaceutical-grade medicines, your business relies on automated liquid filling systems for efficiency and reliability.
When manually filling is no longer feasible due to scale, error rates, or contamination risks, liquid filling machines provide a seamless upgrade to automated production. They reduce spillage, maintain hygiene, and ensure exact fill levels across thousands of containers per hour.
Components of a Liquid Filling Machine
Understanding the main parts of a liquid filling machine helps in choosing, operating, and maintaining it effectively.
1. Hopper or Product Tank
This is where the liquid is initially stored before it is distributed to the containers. It must be made from food-grade stainless steel (SS304 or SS316) to resist corrosion and allow easy cleaning.
2. Nozzles
These control the flow of liquid into each container. Anti-drip, shut-off, or multi-head nozzles are common for ensuring a clean, spill-free operation.
3. Conveyor System
A powered conveyor moves the containers into position. Conveyors can be made from belt, chain, or slat systems, depending on the product type and container design.
4. Filling Mechanism
This could be volumetric, gravimetric, or time-based, depending on the product and accuracy needed. Volumetric piston fillers are ideal for precise fill volumes, while gravity-based fillers are more cost-effective for simpler applications.
5. Control Panel
Modern machines include PLC controls and touchscreen HMIs for managing fill levels, speed, and troubleshooting diagnostics. Advanced systems can store recipes for different product runs.
Liquid Filling Machines for Small-Scale and Startup Use
Startups and craft-based businesses often think they can't afford high-end machines. However, tabletop liquid filling machines and semi-automatic fillers provide an affordable entry into automation. These machines are perfect for short batches, custom formulations, or boutique productions.
Benefits include:
Affordable initial investment
Compact design
Easy to clean and maintain
Upgradable to full automation later
Common Challenges and How to Avoid Them
Despite their many advantages, liquid filling machines must be used correctly to prevent problems. Here are some challenges and proven solutions:
1. Foaming During Filling
Foamy liquids like shampoos or carbonated beverages can overflow. Use bottom-up filling nozzles and adjustable fill speeds to avoid foaming.
2. Dripping and Spillage
This is often caused by poorly maintained nozzles or incorrect timing. Opt for anti-drip nozzles and regularly check valve integrity.
3. Inconsistent Fill Levels
This usually results from improper calibration or air bubbles in the product. Regular calibration and using degassing systems can resolve these issues.
4. Container Misalignment
If bottles are not correctly positioned, they may not fill properly. Use sensor-based indexing systems to align and detect containers before filling starts.
Note: IndiBlogHub features both user-submitted and editorial content. We do not verify third-party contributions. Read our Disclaimer and Privacy Policyfor details.