Understanding Cast Iron Melting Point and Its Crucial Role in Casting
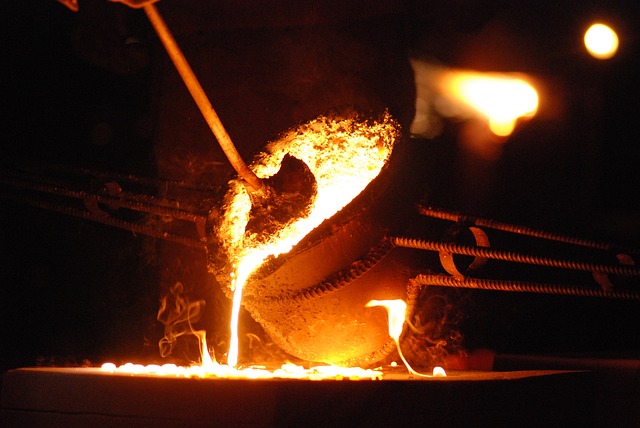
Melting is a very important process in casting because the raw metal materials are formed into usable parts through casting. For cast iron producers, it is important to know the cast iron melting point because this parameter defines the features of the final metal and its tendency to corrosion, as well as the metal’s performance in mechanical applications. This blog post focuses on the process of melting cast iron, describing its significance, conditions, and stages.
Benefits of Cast Iron Melting Point
The cast iron melting point is one of the most important factors that influence the success of the casting process. It determines many attributes of the final product, such as the mechanical properties and the durability of the deliberated product. Here’s why the melting point is so crucial:
1. Quality of Castings
The quality of castings is directly related to the melting process. A proper understanding of the cast iron melting point helps ensure that the metal is heated to the right temperature, which is essential for achieving the desired fluidity. This helps to fill the required moulds with melted cast iron. This results in the production of high-quality casting products with minimal defects.
2. Mechanical Properties
The process of melting the metal also has an impact on the strength, hardness, and ductility of the cast iron. If the melting point of the cast iron is not well controlled, it can cause defects in the final product, such as cold shuts, porosity, and weak structural features. This can impact the performance of the final work extensively.
3. Chemical Composition
The melting point affects the chemical constitution of cast iron since it has to be at the right temperature. Some materials, such as carbon, silicon, and sulfur, exhibit certain properties at one temperature and completely different properties at another temperature. The correct melting point makes castings of the right toughness or strength and the perfect level of resistance to corrosion.
Minimum Requirements for Melting Cast Iron
A few conditions concerning the process of melting have to be fulfilled to reach the required cast iron melting point. These specifications help to guarantee that the molten iron comprises the right ingredients for one to get strong casting systems.
1. Temperature Control
The temperature used to melt the cast iron is another important factor in the casting process. The normal melting point of cast iron varies between 1200 and 1300 degrees Celsius, depending on the nature of the cast iron. Moreover, the tapping temperature, or the temperature at which the molten iron is taken out of the furnace to be poured, needs to be slightly higher than the pouring temperature to prevent the loss of heat during this process. It also requires stringent temperature control so that problems such as inadequate mould filling or the formation of poor castings do not occur.
2. Chemical Composition Management
The chemical composition of molten cast iron is also required to be at certain specifications to achieve high-quality casts. Controlling of constituents like carbon, silicon, phosphorus, etc., during the melting stage is essential. For example, the carbon content needs to be controlled and regulated to ensure it gets to the right hardness and strength as required in the final product. Similarly, to maintain a proper level of silicon and get the right flow, the control of this element will be effective in avoiding defects.
3. Minimizing Harmful Impurities
In the process of melting, it is desirable to reduce the amount of impurities like sulfur and phosphorus within the casting. This requires desulphurization and dephosphorization techniques that minimize impurities to tolerable levels. For instance, melting in a hot blast cupola furnace reduces sulfur, while charging low phosphorus pig iron can regulate phosphorus.
4. Ensuring the Purity of Molten Iron
Another very important parameter is the purity of molten iron Used in the casting process. The formation of slag, gas, and inclusions causes cracks and porosity on the surface of the final product. In order to maintain purity, limestones, and fluorites are added to the raw materials during the melting process to form a slag that can easily be skimmed off, leaving behind molten iron for the casting process.
Steps in the Cast Iron Melting Process
Here is an overview of the key steps involved in the cast iron melting process:
1. Preparation of Charge Material
The charge material, which consists of pig iron, scrap steel, and other alloying additions, is prepared before the procedure of melting starts. This material is chosen according to the required composition of the alloy in the final casting process. It is also important to preheat the charge material to lower the energy needed to melt the material.
2. Charging the Furnace
The charge material is prepared and then introduced to the furnace to undergo a series of transformations. The types of materials to be loaded are characterized by a sequence, and depending on the furnace, the materials with higher density, like pig iron, are loaded first, followed by scrap steel and then the alloying elements. This sequence makes for even melting and prevents the chemical composition from getting altered in any way.
3. Melting and Refining
After that, the furnace is charged, and the process of melting starts. The charge material is heated to the temperature where cast iron has to melt, thus turning it into molten iron. At this stage, refining agents are accepted, and undesirable impurities in the molten iron are removed.
4. Temperature Adjustment
Once the molten iron is at or close to the intended temperature, more modification is done to maintain the temperatures appropriate for casting. This step is critical in ensuring that the molten iron stays in a liquid state and does not solidify before it is poured into the moulds to make the finished product.
5. Pouring and Casting
When the iron is in a molten state, it is poured into the moulds to get the required castings. This process must be done as soon as possible and in the shortest time possible to prevent the molten iron from cooling and, therefore, not filling the moulds. After the completion of the casting process, the moulds are allowed to cool, and the castings are taken for further finishing processes.
Reliable Cast Iron Solutions for Industrial Needs
The melting point of cast iron is a critical factor in the casting technique, affecting all aspects of the casting process, including the quality, mechanical properties, and chemical nature of the final product. By managing this factor, the manufacturers will be able to manufacture high-quality castings that are in demand by different industries.
At AKP Ferrocast, we provide ductile and gray iron casting products that are produced to the highest standards of quality and are useful in various industries. Through our experience in the cast iron melting point, we guarantee that our products are of high quality and accredited for use in many different applications throughout the world.
Note: IndiBlogHub features both user-submitted and editorial content. We do not verify third-party contributions. Read our Disclaimer and Privacy Policyfor details.