Understanding the Role of a Brass Inserts Manufacturer in the Industry
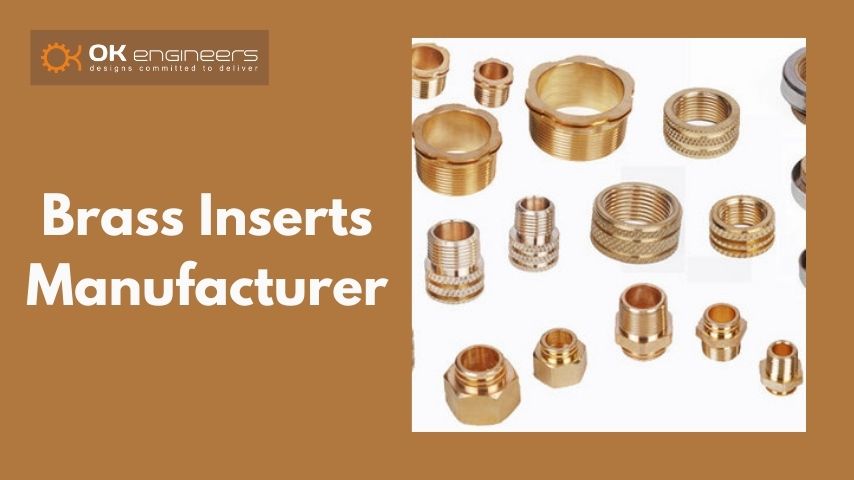
When it comes to precision manufacturing, the role of a Brass Inserts Manufacturer is crucial in various sectors, from automotive to plumbing, and electrical to mechanical applications. Brass inserts are commonly used to provide threaded components for joining other parts, ensuring the integrity and durability of an assembly. In this blog, we will explore the significance of Brass Inserts Manufacturer, their processes, applications, and what to look for when selecting a supplier.
What Are Brass Inserts?
Brass inserts are metal components used in applications where a strong, secure threading is necessary. These inserts are designed to fit into holes in other materials, such as plastic or soft metals, to create a threaded hole for bolts, screws, or other fasteners. Their ability to withstand wear and corrosion makes them ideal for high-stress and high-temperature applications. As a Brass Inserts Manufacturer, providing high-quality inserts ensures the functionality and longevity of the final product.
The Importance of Choosing the Right Brass Inserts Manufacturer
Selecting a Brass Inserts Manufacturer is a critical decision for any business that requires precision threaded inserts. The quality of brass inserts can directly impact the performance of the end product, especially in demanding industries like automotive, aerospace, and electronics. It’s essential to work with a manufacturer that prioritizes quality control, material selection, and design expertise.
Types of Brass Inserts
Brass inserts come in various types and designs to meet the needs of different applications. Some common types include:
Threaded Inserts: These are the most common type of brass insert. They are designed to create strong, reliable threads in materials like plastics, aluminum, or composite materials. A Brass Inserts Manufacturer typically offers inserts in various sizes and thread patterns to suit specific customer needs.
Helical Inserts: These are used to repair or reinforce threads in worn or damaged materials. A Brass Inserts Manufacturer creates these inserts with a helical design, making them ideal for long-lasting applications.
Self-Embedding Inserts: This type of insert is designed to embed itself into softer materials, providing a secure and reliable hold without requiring external threading tools.
Expansion Inserts: Expansion inserts are used to create a secure grip when installed into a material. These inserts expand as they are driven in, making them ideal for creating strong, vibration-resistant joints.
Key Advantages of Brass Inserts
As a Brass Inserts Manufacturer, it's important to highlight the numerous benefits that brass inserts offer to industries. Some of these advantages include:
Durability: Brass is highly resistant to corrosion, oxidation, and wear, making it perfect for long-lasting applications.
Strength: Brass inserts offer robust mechanical strength, which is essential for ensuring the integrity of threaded joints.
Ease of Use: Installing brass inserts is straightforward, requiring minimal tooling or labor, making them ideal for mass production.
Customization: Brass inserts can be manufactured in various sizes, designs, and threading configurations, offering flexibility for a wide range of applications.
The Manufacturing Process of Brass Inserts
The process of creating brass inserts involves several key steps, which a skilled Brass Inserts Manufacturer follows to ensure the product's quality and precision:
Material Selection: The first step is selecting the appropriate brass alloy. Brass is typically composed of copper and zinc, but the ratio may vary depending on the desired properties, such as strength, corrosion resistance, or ease of machining.
Molding and Casting: After the material is selected, it is melted and poured into molds. This process creates the basic shape of the brass insert. A Brass Inserts Manufacturer uses advanced casting techniques to create components with intricate designs.
Machining: After the initial molding, the inserts undergo machining processes like turning, threading, or tapping to create the final threaded structure. Precision machinery is used to ensure the threads are cut to exact specifications.
Quality Control: Once the brass inserts are manufactured, they undergo rigorous quality control tests. These may include dimensional checks, strength testing, and corrosion resistance evaluations. Ensuring the final product meets industry standards is a crucial responsibility for a Brass Inserts Manufacturer.
Applications of Brass Inserts
Brass inserts are used in a wide range of industries due to their strength, durability, and versatility. Some common applications include:
Automotive Industry: Brass inserts are used in automotive assemblies, such as engine components, to provide secure and durable threaded connections. As a Brass Inserts Manufacturer, producing inserts for automotive applications requires attention to the high performance and safety standards of the industry.
Aerospace Industry: Aerospace components require extremely reliable parts that can withstand high stress and environmental conditions. Brass inserts provide the necessary strength and durability for aerospace applications.
Electronics: Brass inserts are widely used in electronic devices, where they facilitate the assembly of circuit boards and enclosures. They provide secure threading for connectors, fasteners, and other components in electronic devices.
Plumbing: In plumbing systems, brass inserts are used to create durable connections in pipes and fixtures. Their resistance to corrosion makes them ideal for both water and gas systems.
Furniture and Construction: Brass inserts are also used in furniture manufacturing and construction to provide threaded inserts for furniture hardware or structural components.
What to Look for in a Brass Inserts Manufacturer
When selecting a Brass Inserts Manufacturer, there are several factors to consider:
Experience: Look for manufacturers with years of experience in producing high-quality brass inserts. A manufacturer with a proven track record is more likely to deliver products that meet your needs.
Customization: A good manufacturer should be able to customize brass inserts to fit your specific requirements. Whether you need different sizes, thread configurations, or special materials, customization is key.
Quality Control: Quality assurance processes should be stringent, ensuring that each batch of brass inserts meets the necessary standards and specifications.
Material Expertise: A reliable Brass Inserts Manufacturer should have extensive knowledge of different types of brass alloys and how they perform in various applications.
Timely Delivery: Look for a manufacturer who can deliver your brass inserts on time, especially for industries that rely on just-in-time manufacturing processes.
Conclusion
In conclusion, a Brass Inserts Manufacturer plays a vital role in industries that require precision, durability, and reliability in threaded components. From automotive to electronics, and aerospace to plumbing, brass inserts are essential in ensuring secure connections in a wide range of applications. By choosing a reputable manufacturer with experience and expertise, businesses can ensure they receive high-quality brass inserts that meet their specific needs.
Note: IndiBlogHub features both user-submitted and editorial content. We do not verify third-party contributions. Read our Disclaimer and Privacy Policyfor details.