Understanding the Science Behind Hollow Fiber Spinning Machines
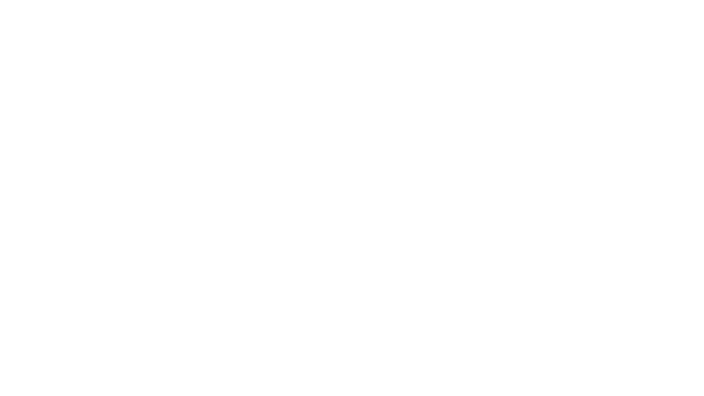
In the world of advanced manufacturing, the creation of high-performance fibers plays a pivotal role in industries ranging from textiles to medical devices, filtration systems, and even water purification. One of the most innovative technologies that has revolutionized fiber production is the Hollow Fiber Spinning Machine. While these machines are often taken for granted, their science and engineering are truly remarkable. This blog will delve into the intricate workings of hollow fiber spinning machines, exploring how they operate and the science behind their functionality.
What Is a Hollow Fiber Spinning Machine?
Before diving into the mechanics, let's first understand what hollow fibers are. Hollow fibers are fibers that feature a hollow core or tube-like structure in their cross-section. These fibers can be made from a wide variety of materials, including polymers such as nylon, polypropylene, and polyvinylidene fluoride (PVDF). The unique structure of hollow fibers gives them special properties, including light weight, increased surface area, and greater strength-to-weight ratio, making them highly desirable for applications in medical devices (e.g., dialysis machines), water filtration, and even insulation materials.
A hollow fiber spinning machine is a specialized industrial device used to create these hollow fibers by spinning a polymeric material into fibers with a hollow central cavity. The machine uses a combination of precise temperature control, air pressure, and extrusion techniques to create fibers that possess the required hollow structure.
The Science Behind the Process
The process of creating hollow fibers involves several complex steps, with precise control over the material’s behavior at each stage to ensure optimal results. Let’s break down the fundamental science behind how hollow fiber spinning machines work:
1. Polymer Solution Preparation
The first step in the process is the preparation of the polymer solution, which serves as the base material for the hollow fibers. The polymer is dissolved in a solvent to create a viscous solution that will be fed into the spinning machine. The selection of the polymer material depends on the intended application, as different polymers have different mechanical properties, chemical resistances, and thermal behaviors.
2. Extrusion and Spinneret Design
Next, the polymer solution is forced through a spinneret—a device that has tiny holes designed to shape the fibers. A key feature of hollow fiber spinning is the spinneret’s ability to control the formation of the hollow core. This is achieved by using a dual or concentric spinneret. The concentric spinneret consists of an inner nozzle and an outer nozzle. The polymer solution is extruded through the outer nozzle, while a core fluid, such as air or nitrogen, is introduced through the inner nozzle. This process results in a hollow structure as the polymer solution forms around the core fluid during extrusion.
3. Cooling and Solidification
Once the polymer solution is extruded, it travels through a cooling zone. This zone typically involves a series of water baths or air jets that cool the polymer and cause it to solidify. The cooling process is critical to the formation of the hollow fiber. The core fluid that was introduced during the extrusion process helps maintain the hollow space inside the fiber as it solidifies.
4. Post-Spinning Stretching
After the fiber is formed, it often undergoes a stretching process. This is done to elongate the fiber and improve its strength and uniformity. Stretching also helps control the fiber's diameter and the degree of hollow core formation. The extent of stretching and the rate at which it occurs are carefully monitored to ensure that the fibers maintain their intended properties.
5. Winding and Collection
Once the hollow fibers have been stretched and cooled, they are wound onto spools for further processing or direct use in manufacturing. Depending on the end use, the fibers may undergo additional treatments, such as heat setting or chemical modifications, to enhance their properties.
Key Advantages of Hollow Fiber Spinning Machines
The ability to create hollow fibers with a high degree of precision offers several distinct advantages:
Increased Surface Area: The hollow structure increases the fiber's surface area without significantly increasing its weight. This is particularly beneficial in applications like filtration, where a larger surface area improves efficiency.
Light Weight: Hollow fibers are lighter than solid fibers, making them ideal for applications in industries such as aerospace and automotive, where reducing weight is a priority.
Enhanced Strength-to-Weight Ratio: Due to the hollow structure, these fibers tend to have a superior strength-to-weight ratio, making them highly durable yet lightweight.
Customization of Properties: The hollow fiber spinning process allows manufacturers to adjust the diameter of the hollow core, giving them the ability to fine-tune the properties of the fiber. This can be crucial for applications in medical devices or filtration systems where specific requirements must be met.
Applications of Hollow Fiber Spinning Machines
Hollow fiber technology has a broad range of applications that take advantage of the unique properties of hollow fibers:
Medical Devices: Hollow fibers are widely used in medical applications such as hemodialysis, where they form the basis of dialyzers. Their large surface area and ability to facilitate selective filtration are essential in this life-saving treatment.
Filtration Systems: In water treatment and air purification, hollow fiber membranes are used to separate contaminants from liquids or gases, offering high filtration efficiency.
Textile Industry: Hollow fibers are used in insulation materials, clothing, and sportswear, where lightweight and breathable fabrics are required.
Energy Sector: Hollow fiber membranes can be used in gas separation processes, enhancing energy efficiency in various industrial processes.
Conclusion
The hollow fiber spinning machine is a testament to the complexity and innovation of modern manufacturing technologies. The combination of polymer science, fluid dynamics, and mechanical engineering results in a machine that produces fibers with unique properties that are indispensable across numerous industries. By understanding the science behind these machines, we can appreciate how they contribute to advancements in technology, medicine, and everyday life.
Note: IndiBlogHub features both user-submitted and editorial content. We do not verify third-party contributions. Read our Disclaimer and Privacy Policyfor details.