Understanding USP 1790 Particles for Visual Inspection and Vial Defect Detection in the USA
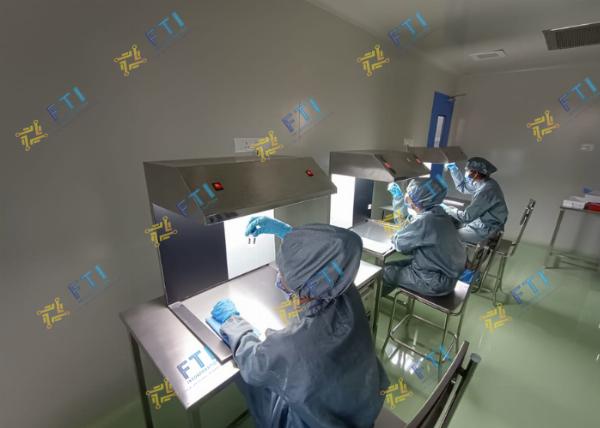
In the world of pharmaceuticals and manufacturing, quality control is paramount. Ensuring the safety and efficacy of products requires rigorous standards and precise inspections. Two critical aspects of this process are USP 1790 particles for visual inspection and vial defect detection in the USA. This article will delve into these concepts, explain their importance, and outline the visual inspection standards that govern these practices.
What is USP 1790 Particles for Visual Inspection?
USP 1790 refers to a standard set by the United States Pharmacopeia (USP) that provides guidelines for the visual inspection of particles in pharmaceutical products. This standard is crucial because it helps ensure that injectable drugs and other sterile products are free from visible particles that could compromise safety or efficacy.
USP 1790 particles for visual inspection involves examining pharmaceutical products under controlled conditions to identify any foreign particles. These particles could be anything from dust to larger, more concerning contaminants that could affect the safety of the drug. The presence of particles in injectable solutions, for example, can lead to severe complications if they are injected into the body.
Visual inspection under USP 1790 guidelines helps manufacturers and quality control teams to:
1. Ensure Product Safety: By detecting and removing particles, manufacturers can prevent potential health risks associated with contaminated products.
2. Maintain Product Quality: Consistent visual inspection helps in maintaining the high quality of pharmaceutical products, which is critical for patient safety.
3. Meet Regulatory Requirements: Compliance with USP 1790 is essential for regulatory approval and market access.
The Importance of Vial Defect Detection in the USA
Vial defect detection in the USA is another crucial aspect of quality control in the pharmaceutical industry. Vials are commonly used for packaging injectable drugs, and any defects in these containers can compromise the integrity of the product inside. Defects can include issues such as cracks, leaks, or improper sealing.
Effective vial defect detection is essential for several reasons:
1. Prevent Contamination: Defects in vials can lead to contamination of the drug, which poses a serious risk to patient health.
2. Ensure Proper Dosage: Leaks or cracks can affect the dosage of the drug, potentially leading to underdosing or overdosing.
3. Maintain Sterility: Vials must remain sterile to ensure that the drug remains safe for use. Defects can compromise this sterility.
To address these issues, advanced inspection techniques and equipment are used in the USA to detect and address vial defects. These methods ensure that only defect-free vials are used, which is crucial for maintaining the overall quality of pharmaceutical products.
Visual Inspection Standards
Visual inspection standards are the benchmarks set to ensure that products meet specific quality criteria through visual examination. These standards are critical for maintaining the safety and efficacy of pharmaceutical products. The standards provide a framework for identifying defects and ensuring that products are free from contaminants.
Visual inspection standards typically involve the following:
1. Inspection Conditions: Products are inspected under controlled lighting conditions to make sure that all particles and defects are visible. This includes using appropriate magnification and ensuring the environment is free from distractions.
2. Inspection Procedures: Procedures are outlined to guide inspectors on how to conduct the visual checks systematically. This includes protocols for examining different types of products and defects.
3. Acceptance Criteria: Standards define what constitutes an acceptable level of particles or defects. For instance, there are limits on the number and size of particles allowed in injectable solutions.
The visual inspection standards are designed to be thorough and precise, ensuring that products meet safety requirements before they reach consumers.
Key Aspects of USP 1790 and Vial Defect Detection
1. Training and Expertise: Inspectors must be properly trained to identify particles and defects accurately. Expertise in handling and examining pharmaceutical products is essential for effective quality control.
2. Technology and Equipment: Modern visual inspection often involves advanced technologies like automated inspection systems, which enhance accuracy and efficiency. For vial defect detection, equipment such as cameras and sensors are used to detect imperfections that are not easily visible to the naked eye.
3. Documentation and Compliance: Proper documentation of inspection results is vital for regulatory compliance and quality assurance. Records help in tracking quality trends and addressing issues promptly.
Challenges and Solutions
Both USP 1790 particles for visual inspection and vial defect detection in the USA come with their challenges:
1. Particle Detection: Small particles can be difficult to detect visually, especially in large volumes. Solutions include using high-resolution imaging systems and improving training for inspectors.
2. Vial Defects: Detecting subtle defects in vials requires precision. Advanced inspection systems and regular calibration of equipment help address this challenge.
3. Standard Compliance: Adhering to visual inspection standards requires continuous monitoring and updating of procedures. Regular audits and reviews ensure that standards are consistently met.
Conclusion
In the pharmaceutical industry, ensuring product safety and quality is non-negotiable. USP 1790 particles for visual inspection and vial defect detection in the USA are critical components of this process, helping to maintain the high standards required for pharmaceutical products. By adhering to visual inspection standards, manufacturers can detect and address issues before products reach consumers, ensuring safety and efficacy.
The effective implementation of these practices requires a combination of skilled personnel, advanced technology, and rigorous standards. As the pharmaceutical industry continues to evolve, maintaining high-quality inspection processes will remain essential for protecting public health and ensuring the reliability of pharmaceutical products.
Contact Us:
Phone:
+91 8200487148, +918200487148, +91 9638344845, +919638344845)
[email protected] | [email protected]
Indian Address
Forensic Technological Innovation, Incubated at National Forensic Sciences University,
Sector 9, Gandhinagar Gujarat 382007, India.
USA office: 58 Albert Ct, City: Randolph
State: New Jersey
Zip code: 07869 USA
Note: IndiBlogHub features both user-submitted and editorial content. We do not verify third-party contributions. Read our Disclaimer and Privacy Policyfor details.