What Are the Benefits of Using a Tool Setter CNC in Manufacturing?
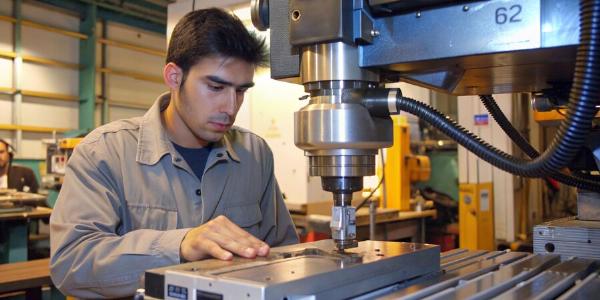
Modern manufacturing demands high precision and efficiency. One key component that significantly enhances these aspects is the Tool Setter CNC. This device ensures tools are accurately set up before use, providing numerous advantages for the manufacturing process. This detailed article will elucidate on the primary benefits of using this tool in manufacturing.
Increased Precision and Accuracy
Tool Setters play a crucial role in ensuring cutting tools are positioned correctly. They use advanced technology to measure and set tool parameters with micron-level precision. This high degree of accuracy is essential for producing high-quality parts and maintaining consistency across large production runs. When tools are accurately set, the chances of errors and defects in the final product are minimized. This precision is particularly important in industries that require intricate and detailed work, such as aerospace and medical device manufacturing.
Reduced Setup Time
Using a Tool Setter CNC dramatically cuts down the time needed to set up machines. Traditional methods are time-consuming and prone to human error. In contrast, a Tool Setter automates this process, allowing tools to be preset outside the machine. This setup not only saves time but also ensures that the data transferred to the CNC machine is error-free, enhancing overall efficiency. With reduced setup times, the production process becomes more streamlined, allowing for quicker turnaround times on projects and increased throughput.
Enhanced Productivity
By minimizing setup times and ensuring precise tool positioning, Tool Setters boost overall productivity. Machines spend more time running and less time being set up, leading to higher output. Operators can also prepare the next tool while the current one is in use, further increasing operational efficiency. This continuous operation without significant downtime ensures that manufacturing processes are more efficient and cost-effective.
Improved Tool Life
Regular monitoring and adjustment of tools using a Tool Setter CNC help extend tool life. The device detects wear and tear, allowing timely maintenance or replacement before significant issues arise. This proactive approach prevents premature tool failure and reduces costs associated with tool replacement and defective parts. By maintaining tools in optimal condition, manufacturers can ensure consistent performance and reduce the frequency of unexpected downtimes.
Better Quality Control
Tool Setters ensure consistent and repeatable measurements, which are crucial for quality control. Accurate tool setup leads to the production of high-quality parts with fewer defects. Additionally, advanced Tool Setters can store measurement data for traceability and quality audits, providing an added layer of assurance. This data can be invaluable during quality inspections or audits, demonstrating adherence to stringent manufacturing standards.
Types of Tool Setters
There are several types of Tool Setters, each suited for different applications:
Presetter: Measures tool geometry outside the machine, ensuring accurate tool positioning.
Contact Tool Setter: Uses physical contact to measure tool length and diameter, offering reliability even in challenging conditions.
Non-contact Tool Setter: Utilizes lasers or optical systems for measurement, ideal for delicate or high-speed tools.
In-process Tool Setter: Adjusts tools during the machining process, ensuring continuous precision without halting production.
Tool Breakage Detection: Detects broken or missing tools to prevent damage, enhancing safety and efficiency.
Wireless/Wired Tool Setters: Provides flexibility in setup and operation, accommodating various manufacturing environments.
These various types cater to specific needs, ensuring optimal performance in diverse manufacturing environments.
Conclusion
Incorporating a Tool Setter CNC in your manufacturing process brings numerous advantages, including enhanced precision, reduced setup times, increased productivity, improved tool life, and superior quality control. By leveraging these benefits, manufacturers can achieve higher efficiency and output, maintaining a competitive edge in the industry. Investing in this tool is a strategic move that pays off through better performance and cost savings. This device ensures that every tool is set up correctly, leading to smoother operations and higher-quality products.
Note: IndiBlogHub features both user-submitted and editorial content. We do not verify third-party contributions. Read our Disclaimer and Privacy Policyfor details.