What Is a Control Valve Seat Leakage Classification?
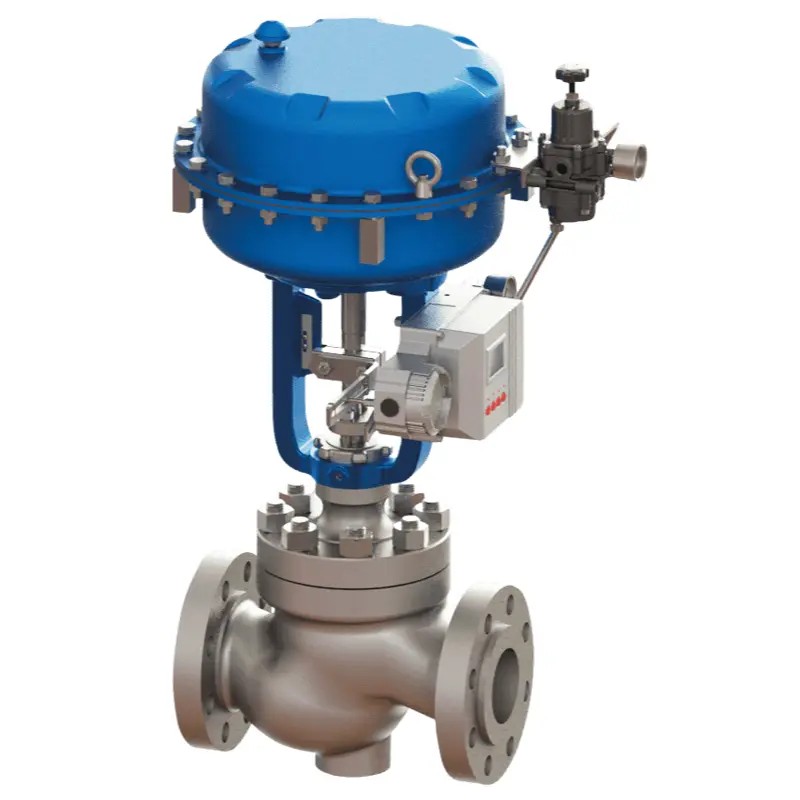
Introduction
Control valves are essential for regulating fluid flow in a wide range of industrial applications. For clean fluids, many valve designs can deliver both accurate flow control and tight shut-off. However, when the media contains solids—as in slurry applications—valve performance becomes more complex. In such demanding environments, no valve design offers perfect performance, and achieving both modulation and isolation becomes a significant challenge.We are a leading control valve manufacturer in China, delivering high-quality valves and precision control actuators designed to meet a wide range of industrial applications.
Standard control valves may provide excellent shut-off initially, but exposure to abrasive fluids can quickly cause erosion, leading to leakage soon after the valve enters service. Therefore, it is not standard practice to rely on a control valve for both regulation and isolation in abrasive service. To ensure effective isolation, manufacturers typically recommend using a dedicated on/off valve in conjunction with the control valve.
In slurry services, metal-seated control valves often exhibit some leakage when closed. Leakage performance is categorized into classes—Class I through Class VI. Classes V and VI are generally associated with isolation valves that incorporate resilient seats (e.g., rubber or urethane). Although some slurry control valves may initially meet Class V shut-off standards, wear typically degrades their performance to Class IV or lower over time.
Understanding Leakage Classifications
Leakage classifications provide a standardized framework for assessing how well a valve seals when fully closed. These classifications help end-users compare valve types and understand performance expectations. Below is an overview of the primary leakage classes:
Class I
This is the baseline leakage classification, allowing the highest level of leakage. These valves are not intended for tight shut-off and are used in non-critical applications where minor leakage is acceptable.
Class II
Offering better sealing than Class I, these valves still permit moderate leakage and are suitable for applications requiring improved, but not strict, shut-off.
Class III
Valves in this class provide better sealing than Class II and are typically used in moderate service conditions where limited leakage is tolerable.
Class IV
A common standard for metal-seated control valves, especially in slurry applications. These valves offer relatively tight shut-off while maintaining durability in abrasive conditions.
Class V
Designed for critical isolation service, Class V valves offer very low leakage. However, in slurry service, metal-seated valves rated to Class V often degrade quickly due to erosion.
Class VI
The highest sealing standard, typically achieved using resilient soft seats. Valves in this class provide bubble-tight shut-off and are ideal for highly sensitive applications, such as food processing or pharmaceuticals.
Key Valve Standards and Testing Specifications
Several industry standards define valve design criteria and leakage testing protocols. Notable standards include:
ASME B16.34
Covers design and pressure ratings for flanged, threaded, and welded valves. It does not define leakage rates but is commonly paired with test standards like API 598.
API 598
A global standard for valve inspection and testing, focusing on isolation valves. It specifies acceptable leakage for both metal- and resilient-seated designs.
MSS SP61
One of the earliest standards for hydrostatic testing of steel valves. Although it’s less used today, it influenced later standards.
ISO 5208
Defines 10 leakage acceptance levels for various valve types. Acceptance criteria are determined between the buyer and the manufacturer.
ANSI/FCI 70-2
The primary standard for control valve seat leakage. It defines the Class I–VI framework and is widely used for internal testing.
ISA S75
Focuses on hydrostatic testing for control valves, particularly external leak testing. It typically references ANSI/FCI 70-2 for seat leakage standards.
These standards help ensure consistent valve performance, safety, and quality across industries.
Factors Influencing Leakage Performance
Several variables impact the sealing performance of control valves, especially in abrasive applications:
Valve Design
The choice between resilient and metal seats directly affects leakage performance. Resilient seats offer tighter sealing but may not withstand high temperatures or abrasive media.
Material Selection
Materials used for sealing surfaces—such as hardened alloys—affect resistance to wear and erosion.
Operating Conditions
Pressure, temperature, and fluid properties (e.g., corrosiveness or abrasiveness) can influence the valve’s ability to maintain shut-off.
Maintenance and Wear
Routine inspection and maintenance are critical. Even the most robust materials will degrade over time, especially under abrasive conditions.
Choosing the Right Valve for Your Application
Selecting an appropriate valve depends on process conditions and the level of shut-off required:
Clean Fluids:
Valves rated to Class V or VI are ideal for clean service where precise control and tight isolation are both needed.
Slurry or Abrasive Applications:
Metal-seated valves with Class IV leakage are often recommended. However, a separate on/off valve should be used for full isolation.
Critical Service:
For industries such as pharmaceuticals or food processing, resilient-seated valves with Class VI ratings provide the necessary bubble-tight performance.
Conclusion
Control valve leakage classification is a vital consideration in valve selection and system design. While clean fluid applications allow for dual functionality—control and isolation—slurry services introduce additional complexity due to erosion and wear.
Metal-seated valves rated for Class IV leakage are standard in abrasive applications, where some degree of leakage is inevitable. For applications requiring near-zero leakage, resilient-seated valves rated to Class V or VI are preferred, although they may not be suitable for high-wear or high-temperature environments.
Ultimately, selecting the right valve involves balancing performance, durability, and shut-off requirements to match the specific operating conditions. By understanding leakage classifications and the factors influencing valve performance, engineers and operators can optimize system reliability and efficiency.Know more about Google SEO Directory
Note: IndiBlogHub features both user-submitted and editorial content. We do not verify third-party contributions. Read our Disclaimer and Privacy Policyfor details.