Automotive Stud Welding Equipment Revolutionizing the Car Manufacturing Process
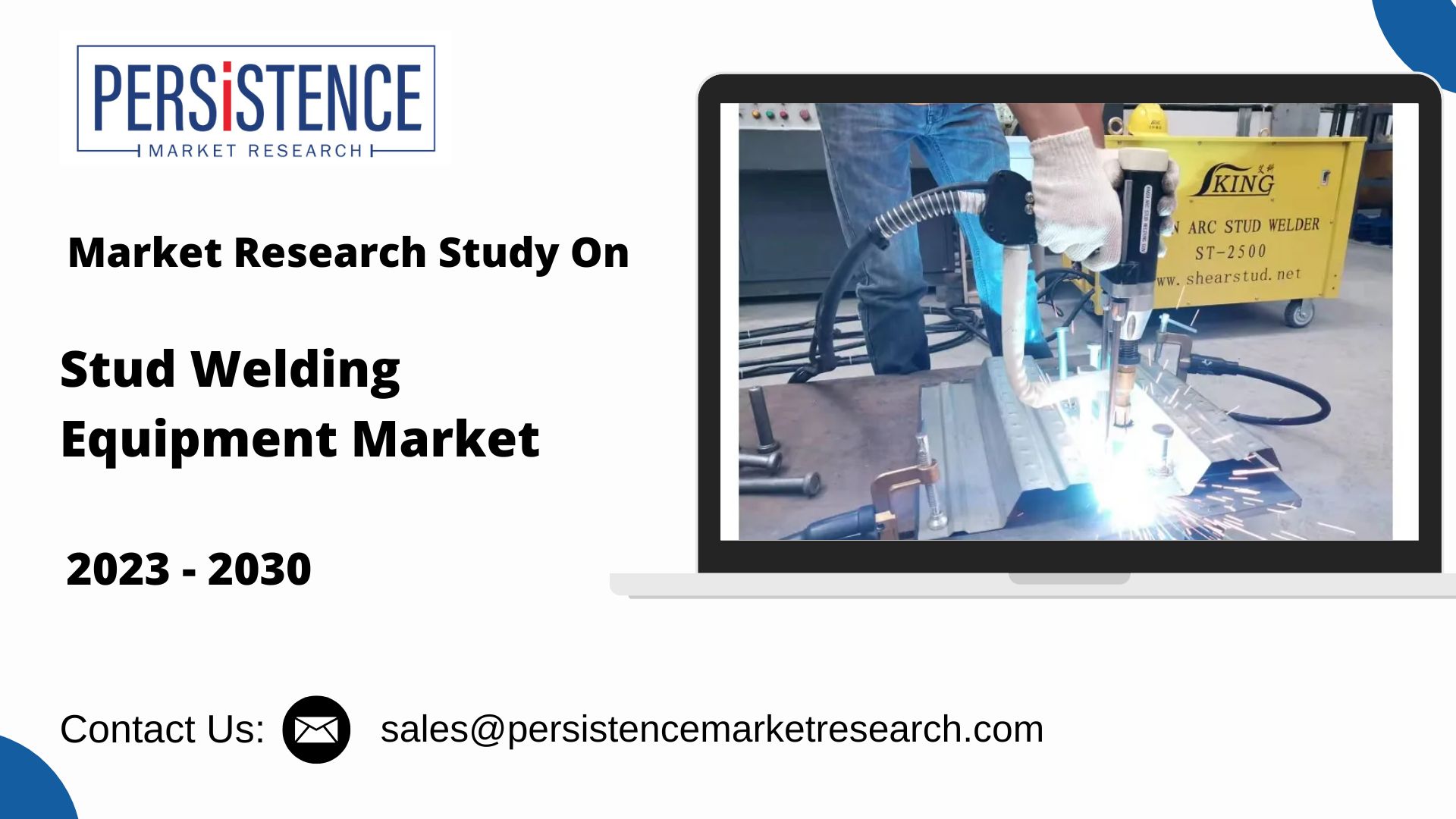
The automotive industry has long been at the forefront of adopting innovative technologies to improve manufacturing efficiency, product quality, and safety. One such technology that has revolutionized the car manufacturing process is stud welding equipment, particularly in the form of automatic and resistance welding systems.
This advanced welding technique, which is used to join metal studs to a base material using electrical resistance, has become a game-changer in automotive production due to its speed, precision, and cost-effectiveness. In this article, we explore how automotive stud welding equipment market is transforming the car manufacturing process, driving efficiency, and enhancing the overall quality of vehicles.
1. High-Speed Production for Automotive Manufacturers
Stud welding equipment is renowned for its speed and efficiency. In the automotive industry, where time is of the essence, the ability to weld a metal stud to a vehicle’s frame or body in just a few seconds makes stud welding a critical tool. The process eliminates the need for time-consuming manual methods, allowing for faster production rates without sacrificing quality.
Impact on Car Manufacturing: Stud welding equipment allows car manufacturers to meet high-volume production demands, reducing cycle times and boosting throughput. This capability is essential for mass production environments, where minimizing downtime and maximizing productivity are key to profitability.
2. Enhanced Structural Integrity and Durability
One of the key advantages of stud welding in the automotive industry is its ability to produce strong, durable welds with minimal risk of defects. The resistance welding process creates a solid bond between the stud and base material, which is critical in automotive manufacturing where structural integrity is paramount. Whether it’s securing fasteners to the vehicle chassis, attaching body panels, or connecting electrical components, the strength of the weld ensures the vehicle’s components stay intact and perform reliably under stress.
Impact on Car Manufacturing: In the automotive sector, stud welding helps to reinforce the structural integrity of vehicles. Strong, reliable welds prevent failure in key areas like the chassis, bodywork, or suspension, ensuring long-term performance and safety. This reliability is particularly important in safety-critical components where any failure could have catastrophic consequences.
3. Precise, High-Quality Welds
Automotive stud welding systems are designed for precision, allowing for consistent, high-quality welds every time. Unlike traditional welding methods, which may introduce imperfections such as spatter, cracks, or distortion, stud welding creates clean, precise welds that require minimal post-weld processing. This is essential in automotive manufacturing, where aesthetic and functional quality is non-negotiable.
Impact on Car Manufacturing: The precision of stud welding ensures that parts are welded to exact specifications without the risk of visual defects or weak spots in the welds. As a result, manufacturers can ensure the finished vehicles meet the highest standards of quality, improving both the aesthetic appeal and functional durability of the final product. This consistency also reduces the risk of rework and returns due to defective welds, resulting in cost savings for manufacturers.
4. Minimal Heat-Affected Zones (HAZ)
In traditional welding processes, the heat generated can affect the surrounding material, leading to distortion or weakened metal. However, stud welding minimizes the heat-affected zone (HAZ) by applying heat directly to the point of contact between the stud and the base material. This means that the surrounding metal remains largely unaffected by thermal stress, helping to preserve the integrity of the base material.
Impact on Car Manufacturing: The minimized heat-affected zone is particularly beneficial in automotive manufacturing, where thin materials or high-strength alloys are often used. The reduced risk of warping or distortion allows manufacturers to maintain the precise dimensions and strength of the vehicle’s components, leading to better overall product quality and lower scrap rates.
5. Flexibility and Versatility for Different Automotive Applications
Stud welding equipment is highly versatile and can be used for a variety of applications in automotive manufacturing. Whether it’s welding electrical components to the body, attaching insulation or brackets, or securing body panels, stud welding can handle a wide range of materials, including mild steel, stainless steel, and aluminum. Additionally, it can be used with both small and large studs, making it suitable for a variety of automotive components, from tiny electrical fasteners to larger structural components.
Impact on Car Manufacturing: The flexibility of stud welding equipment means it can be employed in numerous areas of car production, reducing the need for multiple different welding processes. This versatility streamlines the manufacturing workflow and allows automotive manufacturers to use a single, efficient technology for multiple tasks, further improving productivity.
6. Reduced Need for Consumables and Maintenance
Unlike other welding processes, stud welding does not require consumables like filler rods or gases. This eliminates additional costs and reduces the environmental impact of the welding process. Additionally, the equipment itself requires minimal maintenance, with modern stud welding machines being designed for durability and long-term use. This makes stud welding an economical solution for automotive manufacturers, particularly in high-volume production environments.
Impact on Car Manufacturing: The reduced reliance on consumables helps automotive manufacturers save on material costs and reduces waste generation, contributing to a more sustainable production process. Moreover, the low maintenance requirements of stud welding equipment ensure fewer operational disruptions, improving uptime and overall efficiency.
7. Automation and Integration with Production Lines
The automotive industry has increasingly embraced automation, and stud welding systems are no exception. Many modern stud welding machines can be easily integrated into automated production lines, allowing for fully automated welding processes. This automation ensures consistent quality, reduces the potential for human error, and increases production efficiency.
Impact on Car Manufacturing: Automated stud welding systems can work seamlessly within a fully integrated production line, enabling manufacturers to achieve high levels of precision and speed while reducing the need for manual labor. This level of automation is particularly beneficial for mass production environments, where achieving consistent results across thousands of units is essential. Additionally, automation helps automotive manufacturers maintain competitiveness by reducing labor costs and minimizing the risk of human error.
8. Reduced Environmental Impact
As the automotive industry faces increasing pressure to reduce its environmental footprint, stud welding offers several advantages in terms of sustainability. The process requires fewer consumables, generates less waste, and operates without the need for harmful gases or flux. Additionally, the energy consumption of stud welding systems is relatively low, contributing to a reduction in overall manufacturing energy usage.
Impact on Car Manufacturing: Stud welding equipment helps automotive manufacturers meet their sustainability goals by reducing the amount of material waste, energy consumption, and environmental pollutants produced during the welding process. By adopting more eco-friendly welding techniques, manufacturers can improve their environmental footprint, aligning with both regulatory requirements and consumer preferences for sustainable products.
9. Cost-Effectiveness in High-Volume Production
Stud welding equipment provides significant cost savings in high-volume production due to its speed, low operational costs, and reduced need for consumables. The minimal downtime and fast cycle times associated with stud welding ensure that manufacturers can maintain high productivity levels while minimizing labor and material costs.
Impact on Car Manufacturing: The ability to weld quickly and efficiently with minimal material waste allows automotive manufacturers to lower their production costs. These savings can be passed on to consumers or reinvested into further innovation, allowing manufacturers to remain competitive in a crowded and cost-sensitive market.
10. Improved Safety and Worker Protection
Safety is always a priority in automotive manufacturing, and stud welding systems offer several advantages in this regard. The process involves minimal exposure to hazardous materials, such as high temperatures or toxic gases, compared to traditional welding methods. Furthermore, automated stud welding systems reduce the need for human intervention, lowering the risk of workplace accidents.
Impact on Car Manufacturing: By reducing the potential for safety hazards associated with welding, stud welding equipment helps automotive manufacturers create a safer working environment for their employees. This improves worker health and morale while reducing the likelihood of work-related injuries or accidents, which can result in costly downtime and compensation claims.
Conclusion
Automotive stud welding equipment is revolutionizing the car manufacturing process by enhancing speed, precision, quality, and efficiency. As the automotive industry continues to evolve, the demand for advanced welding technologies like stud welding will only grow. From improving structural integrity to reducing production costs, the advantages of stud welding are clear, making it an essential tool for modern automotive manufacturing. As manufacturers continue to seek ways to streamline their operations, reduce waste, and improve safety, stud welding technology will remain a key driver of innovation in the automotive sector.
Note: IndiBlogHub features both user-submitted and editorial content. We do not verify third-party contributions. Read our Disclaimer and Privacy Policyfor details.