Behind the Print: Secrets to Mastering Your Plastic Card Printer
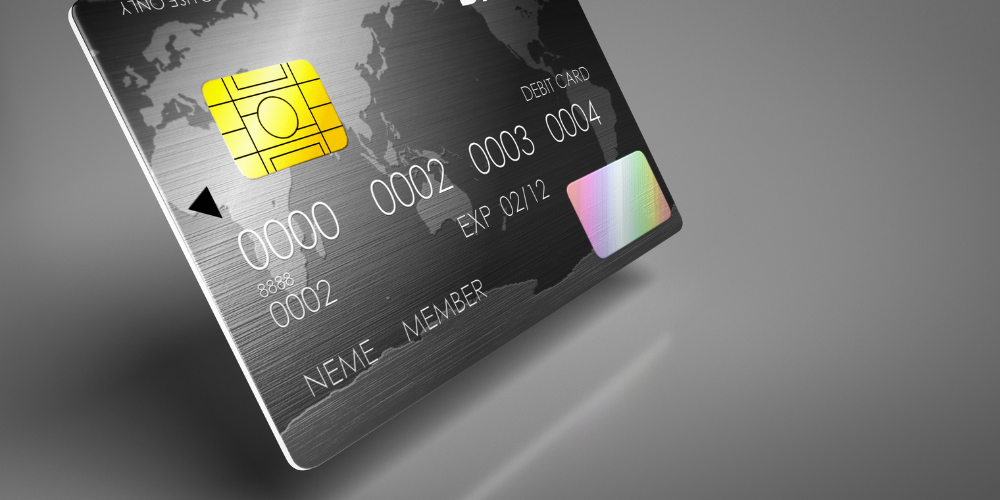
Plastic card printing has evolved from a niche industrial process to an essential business capability that empowers organizations to create professional identification cards, membership badges, loyalty cards, and security credentials in-house. The technology behind modern plastic card printers combines precision engineering with user-friendly interfaces, making it possible for businesses of all sizes to produce high-quality cards that rival professionally manufactured alternatives. Understanding the intricate mechanisms, optimal settings, and advanced techniques that drive successful card printing can transform your output from amateur attempts to professional-grade results. The difference between mediocre and exceptional card printing lies not just in equipment quality but in mastering the subtle art of printer calibration, material selection, and design optimization. This comprehensive exploration reveals the insider knowledge that separates novice operators from true printing professionals, covering everything from basic setup procedures to advanced troubleshooting techniques that ensure consistent, high-quality results every time.
Understanding Printer Mechanics and Technology
Modern plastic card printers utilize sophisticated thermal transfer and dye-sublimation technologies to achieve precise color reproduction and durable card finishes. The printing process involves heated print heads that transfer colored dyes from ribbon cartridges onto blank plastic cards through controlled temperature and pressure applications. Understanding ribbon types, including YMCKO (Yellow, Magenta, Cyan, Black, Overlay) configurations, enables operators to select appropriate consumables for specific printing requirements. Print head alignment and pressure settings directly impact image quality, with minor adjustments significantly affecting color saturation and edge definition. Plastic Card Printer Online provides detailed technical specifications that help users understand their equipment's capabilities and limitations, ensuring optimal performance through proper configuration.
Card Material Selection and Preparation
Choosing appropriate card materials forms the foundation of successful plastic card printing, with various PVC compositions, thicknesses, and surface treatments affecting final results. Standard CR80 cards measuring 85.6mm x 53.98mm accommodate most applications, while specialty materials like composite PVC-PET blends offer enhanced durability for high-wear environments. Surface preparation techniques, including cleaning protocols and static elimination procedures, prevent print defects and ensure consistent adhesion. Pre-printed cards with magnetic stripes, proximity chips, or security features require specialized handling procedures to avoid damage during the printing process. Understanding how different card materials interact with specific ribbon types and print settings prevents costly errors and material waste.
Optimal Print Settings and Configuration
Achieving professional-quality results requires precise calibration of temperature, speed, and pressure settings tailored to specific card materials and ribbon combinations. Color balance adjustments ensure accurate reproduction of corporate logos, photographs, and security elements across different lighting conditions. Print density settings affect both image quality and ribbon consumption, with higher densities producing more vibrant colors but reducing consumable efficiency. Edge-to-edge printing capabilities require careful margin adjustments to prevent print head damage while maximizing card real estate utilization. Plastic Card offers comprehensive guides for optimizing printer settings across various card types and applications, helping users achieve consistent results regardless of project complexity.
Design Optimization Techniques
Effective card design extends beyond aesthetic considerations to encompass technical requirements that ensure optimal printing results. Color management systems prevent color shifts and ensure brand consistency across different printing sessions and equipment. Font selection and sizing considerations account for printer resolution limitations and readability requirements under various lighting conditions. Image resolution optimization balances file size constraints with print quality requirements, typically requiring 300 DPI minimum for professional results. Bleed areas and safety margins accommodate printer tolerances while ensuring critical information remains visible regardless of minor alignment variations. Understanding color gamut limitations helps designers create artwork that translates effectively from screen to printed card.
Advanced Printing Techniques and Features
Modern plastic card printers offer sophisticated features that enhance security, durability, and visual appeal when properly implemented. Holographic overlay applications create tamper-evident security features while adding premium visual effects to standard cards. Multiple overlay options, including UV-resistant and scratch-resistant formulations, extend card lifespan in demanding environments. Dual-sided printing capabilities require careful registration alignment to ensure proper front-to-back positioning of design elements. Encoding capabilities for magnetic stripes, proximity cards, and smart cards demand precise timing coordination between printing and encoding processes. Plastic Business Cards demonstrates advanced applications that showcase the full potential of modern card printing technology.
Maintenance and Troubleshooting Strategies
Preventive maintenance routines significantly extend printer lifespan while maintaining consistent print quality throughout the equipment's operational life. Regular cleaning schedules for print heads, rollers, and internal components prevent dust accumulation and ribbon residue buildup that degrade print quality. Calibration procedures ensure accurate color reproduction and proper card positioning, with regular adjustments compensating for mechanical wear and environmental factors. Common troubleshooting scenarios include ribbon wrinkles, color registration issues, and card feeding problems, each requiring specific diagnostic approaches and corrective actions. Understanding error codes and diagnostic procedures enables operators to resolve issues quickly without requiring external technical support.
Quality Control and Testing Procedures
Implementing systematic quality control measures ensures consistent output quality and identifies potential issues before they affect production batches. Test card protocols verify color accuracy, print registration, and overlay adhesion across different operating conditions. Standardized evaluation criteria help operators maintain consistent quality standards regardless of personnel changes or equipment variations. Documentation procedures track consumable usage, maintenance schedules, and quality metrics to identify trends and optimize operational efficiency. Batch testing protocols prevent large-scale printing errors by validating settings and materials before committing to full production runs.
Cost Management and Efficiency Optimization
Understanding the economics of plastic card printing enables organizations to optimize costs while maintaining quality standards. Ribbon yield calculations help predict consumable costs and plan procurement schedules to avoid production delays. Batch printing strategies minimize setup time and reduce per-card costs through efficient workflow organization. Waste reduction techniques, including proper card handling and storage procedures, maximize material utilization while minimizing environmental impact. Energy efficiency considerations, including standby modes and printing schedule optimization, reduce operational costs without compromising productivity.
Security and Compliance Considerations
Plastic card printing operations often involve sensitive personal information and security credentials requiring strict compliance protocols. Data security measures protect cardholder information throughout the printing process, including secure workstation configurations and access controls. Audit trail requirements document printing activities and consumable usage for compliance reporting and security investigations. Secure disposal procedures for misprinted cards and used consumables prevent unauthorized access to sensitive information. Understanding regulatory requirements for specific industries ensures compliance with applicable standards and regulations.
Future Trends and Technology Evolution
The plastic card printing industry continues evolving with emerging technologies that enhance functionality, security, and environmental sustainability. Digital integration capabilities enable real-time data verification and dynamic card personalization directly from database sources. Contactless technology integration requires specialized equipment and procedures to maintain functionality during printing processes. Sustainability initiatives drive development of eco-friendly consumables and energy-efficient printing technologies. Understanding these trends helps organizations plan equipment upgrades and process improvements that maintain competitive advantages while supporting environmental responsibility goals.
Note: IndiBlogHub features both user-submitted and editorial content. We do not verify third-party contributions. Read our Disclaimer and Privacy Policyfor details.